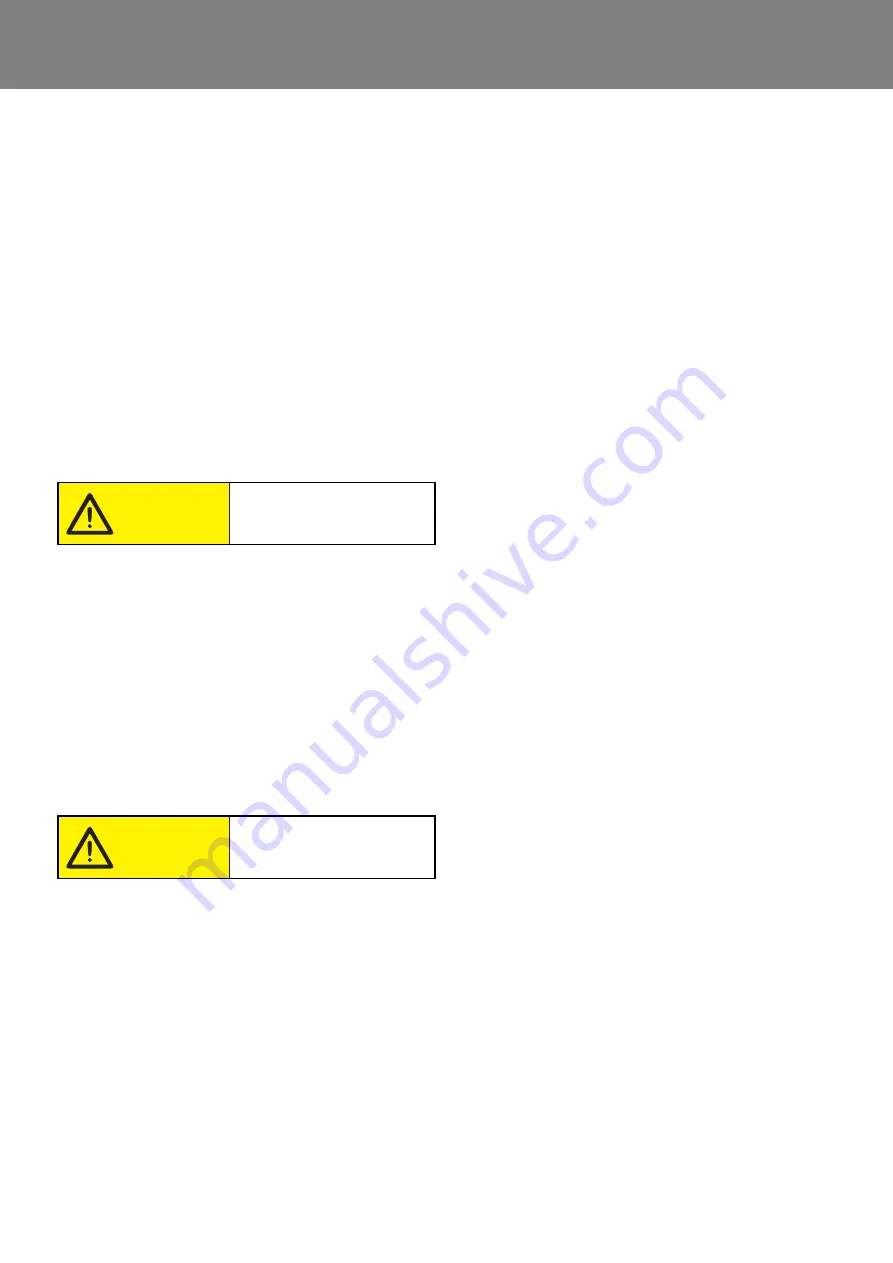
810
Thermo E+ 120/200/320
8 Repairs
NOTE:
–
The combustion chamber should be inserted into the
heat exchanger in such a way that its welding seam is
positioned between 2 and 10 o clock (not upwards!)
(
). A position change during maintenance is
permissible and affects the expected service life of the
combustion chamber positively.
–
Position the cut-outs in the combustion chamber head
as shown in
. Dripping from nozzle fuel is so
collected in a reservoir between disc and burner head
and will be burned at the next burner operation
instead to soil the heater.
2. Install burner (see
8.14 Heat exchanger removal and
installation
The combustion chamber and heat exchanger can
bevery hot. If necessary, let them cool down.
Removal
1. Disconnect the heater from the vehicle electrical sys-
tem (
Observe
!).
2. Unplug connector of the temperature sensors (3,
3. Remove combination nuts (2) and separate burner (1)
from the heat exchanger.
4. If necessary, loosen the exhaust line clamp on the
exhaust outlet (3,
).
5. If existing, close water taps.
Risk of injuries if coolant temperature is increased.
6. Loosen hose clamps on the coolant hoses, pull
coolant hoses from the coolant inlet (5) and the
coolant outlet (6) and seal with blank plugs.
7. Remove screws and washers of the heat exchanger
stand (4).
8. Pull combustion chamber (1) out of the heat
exchanger (2).
9. If necessary remove temperature sensors (see
).
10. Remove heat exchanger from vehicle.
Installation
1. Position the combustion chamber (1) correctly into the
heat exchanger (2) (see
).
2. If necessary install the temperature sensors (see
).
3. Bring heat exchanger (2) into installation position and
mount stand (4) using screws, nuts and washers to
the vehicle according to the mounting points used.
4. If necessary, secure the exhaust line using a clamp to
the exhaust outlet (3).
5. Fit coolant hoses (7) onto the coolant inlet (5) and the
coolant outlet (6) and secure with hose clamps (8).
6. f available, open water taps.
7. Bring burner (1,
) in assembly position and
ensure center alignment and correct fit.
8. Place nuts (2) and alternately tighten them slightly.
9. Tighten nuts (2). For tightening torque, refer to
10. Connect the heater with the vehicle electrical system.
11. Bleed coolant ciruit (see
).
ATTENTION:
The two combination nuts M8, connecting the burner
head and the heat exchanger, must be tightened to
torque, see
, each and additional are to be
secured using thread lock.
8.15 Heater removal and installation
ATTENTION:
The fuel supply system must be subsequently
bleeded (see
The coolant circuit must be subsequently bleeded
(see
Removal
)
Installation
1. Install heat exchanger (see
2. Install burner (see
.).
Risk of burns!
Caution!
Risk of scalds!
Caution!
Summary of Contents for Thermo E+ 120
Page 64: ...memos...