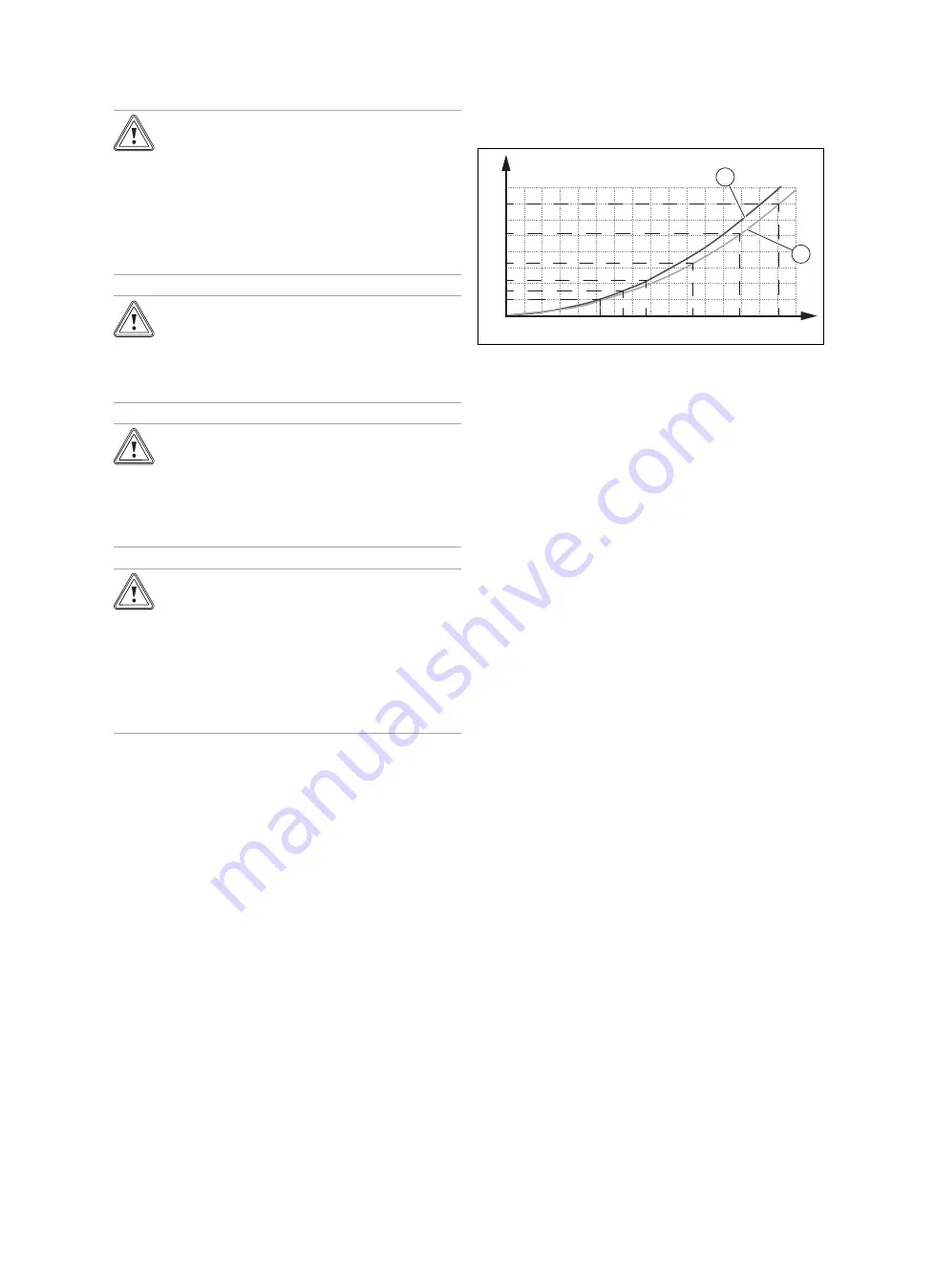
5 Installation
10
Installation and maintenance instructions ecoFIT pure 0020230535_05
Caution.
Risk of material damage caused by
residues in the pipelines.
Welding remnants, sealing residues, dirt or
other residues in the pipelines may damage
the product.
▶
Flush the heating installation thoroughly
before installing the product.
Caution.
Risk of material damage due to heat trans-
fer during soldering.
▶
Only solder connectors if the connectors
are not yet screwed to the service valves.
Caution.
Risk of material damage caused by
changes to the pipes that have already
been connected.
▶
Only bend connection pipes if they have
not yet been connected to the product.
Caution.
Risk of damage caused by incorrect gas
installation.
Excess test pressure or operating pressure
may cause damage to the gas valve.
▶
Check the leak-tightness of the gas valve
using a maximum pressure of 11 kPa
(110 mbar).
▶
Make sure that the existing gas meter is capable of
passing the rate of gas supply required.
▶
Install the following components:
–
Drain cocks at the lowest points in the heating install-
ation (
→
current version of "BS 2879")
–
A heating pump in the heating flow
–
A bypass that is at least 1.5 m away from the product
–
A stop cock in the gas pipe
–
Where applicable, a flow regulator valve to adjust the
flow rate
Pressure loss
from the product
0
50
100
150
200
250
300
350
400
0
200
400
600
800
1000 1200 1400 1600
430
424
418
415
412
435
A
B
1
2
A
Flow rate [l/h]
B
Pressure loss [mbar]
1
Pressure loss
–
ecoFIT
pure 412 - 418
2
Pressure loss
–
ecoFIT
pure 424 - 435
The flow rate must not fall below the value in the diagram.
▶
Check that the volumetric capacity of the expansion ves-
sel is sufficient for the system volume.
5.2
Installing the heating pump
▶
Only use pumps that have an in-rush current
≤
10/15 A.
▶
When designing/selecting the pump, note the pressure
loss of the product.
▶
Install the pump in the heating flow.
▶
Install the pump upstream and downstream of the pump
isolation valves.
▶
Set the pump so that the temperature difference between
the flow and return is no more than 20 °C when the max-
imum flow temperature is set.
–
The flow rate specified in the technical data is
reached.