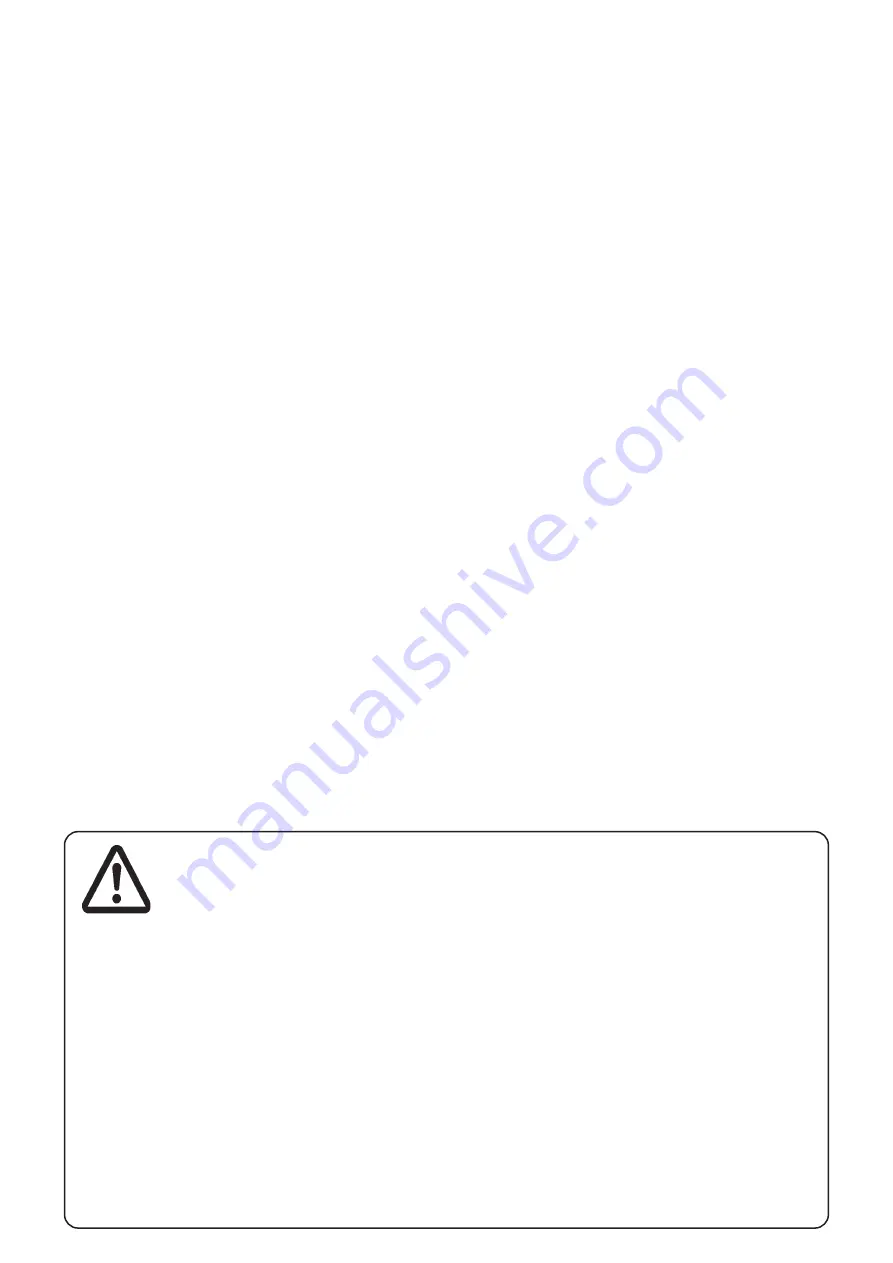
page 25 of 80
• The equipment is designated for a low degree of mechanical stress
and has to be installed in a way so that it cannot be damaged from
outside.
Pumping units have to be installed so that they are protected against
shocks from the outside and against glass splinters in the event of
breakage (implosion).
• The equipment is designated for an ambient and gas inlet temperature
during operation of +10 to +40°C. Never exceed these ambient and
gas inlet temperatures. If pumping / measuring gases which are not
potentially explosive, extended gas inlet temperatures are permissible.
See instructions for use, section “Gas inlet temperatures” or “Techni-
cal data”.
After any intervention at the equipment (e.g., repair / maintenance) the ul-
timate vacuum of the pump has to be checked. Only if the pump achieves
its specified ultimate vacuum is the pump’s leak rate low enough to en
-
sure that no explosive atmospheres will occur in the interior of the equip-
ment.
After any intervention at the vacuum sensor, the leak rate of the equip-
ment has to be checked.
Attention: This manual is not available in all
languages of the EU. The user must not op-
erate the device if he does not understand
this manual. In this case a technically cor-
rect translation of the complete manual has
to be available. The manual must be com-
pletely read and understood before opera-
tion of the device. All specified measures
must be applied, or else must be replaced
by equivalent measures at the user’s own
risk.