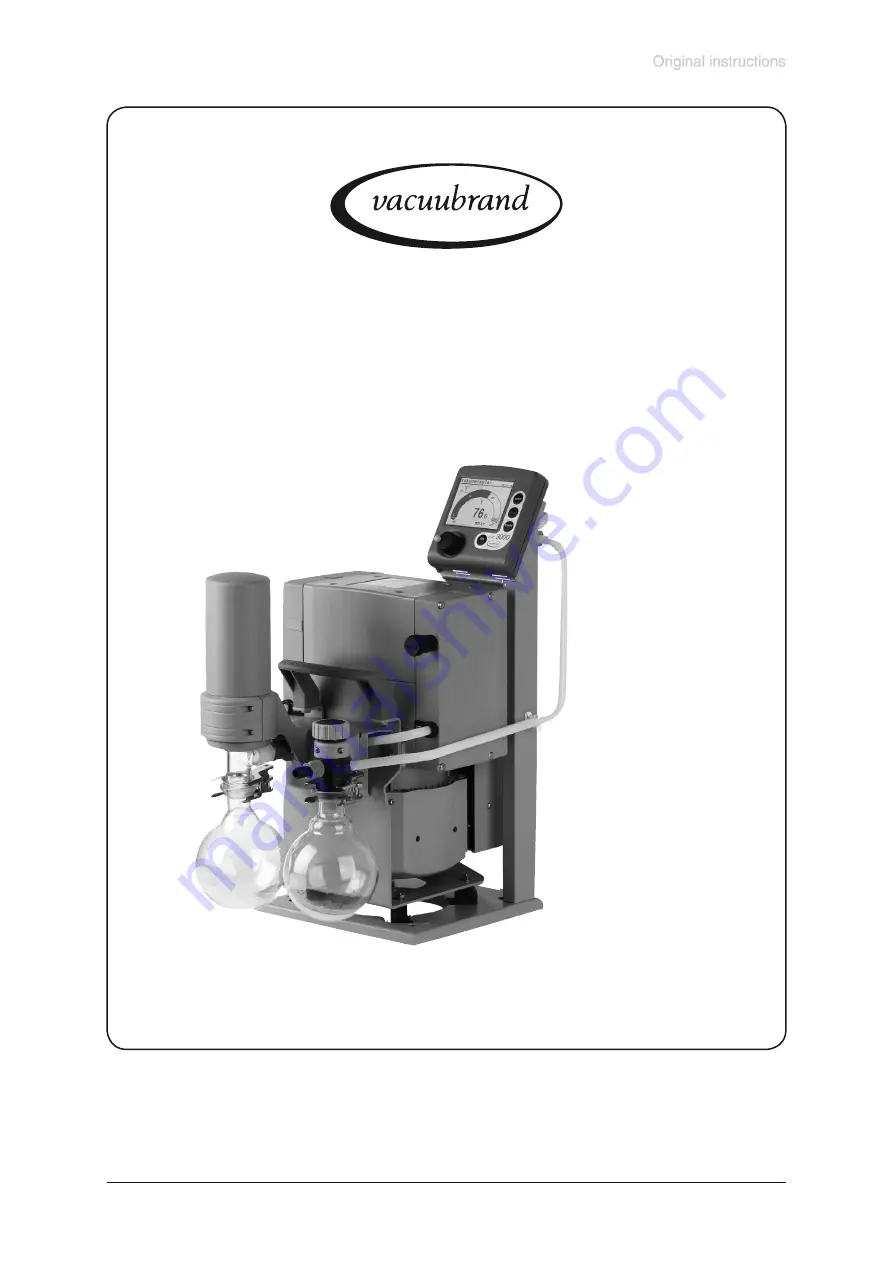
Documents are only to be used and distributed completely and unchanged. It is strictly the users’ responsibility to check carefully
the validity of this document with respect to his product. Manual-no.: 999164 / 19/05/2009
page 1 of 75
Speed controlled chemistry diaphragm pumps
and chemistry pumping units
Instructions for use
Technology for Vacuum Systems
ME 4C NT VARIO
MZ 2C NT VARIO
MD 4C NT VARIO
MV 10C VARIO-B
MD 12C VARIO-B
PC 3002 VARIO
PC 3003 VARIO
PC 3004 VARIO
PC 3010 VARIO
PC 3012 VARIO