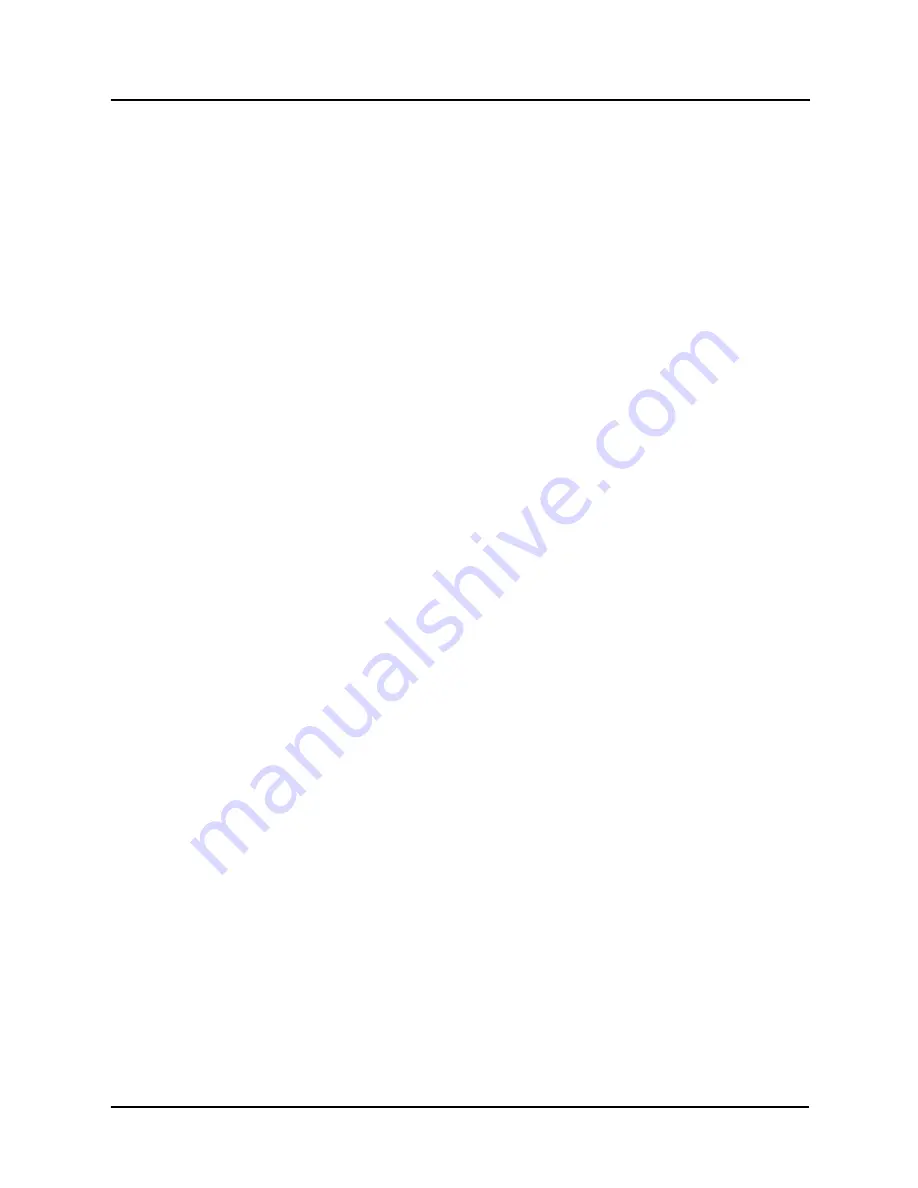
X5 AC Drive User’s Manual
Chapter 4: Connections
DPD00089A
-
29 -
© 2009 Vacon Incorporated All Rights Reserved
4.1
Introduction
This chapter provides information on connecting power and control wiring to the X5 AC drive.
4.2
General Wiring Information
4.2.1 Wiring Practices
When making power and control connections, observe these precautions:
• Never connect input AC power to the motor output terminals T1/U, T2/V, or T3/W. Damage
to the drive will result.
• Power wiring to the motor must have the maximum possible separation from all other power wiring.
Do not run in the same conduit; this separation reduces the possibility of coupling electrical noise
between circuits.
• Cross conduits at right angles whenever power and control wiring cross.
• Good wiring practice also requires separation of control circuit wiring from all power wiring. Since
power delivered from the drive contains high frequencies which may cause interference with other
equipment, do not run control wires in the same conduit or raceway with power or motor wiring.
4.2.2 Considerations for Power Wiring
Power wiring refers to the line and load connections made to terminals L1/R, L2/S, L3/T, and T1/U,
T2/V, T3/W respectively. Select power wiring as follows:
1. Use only UL-recognized wire.
2. Wire voltage rating must be a minimum of 300 V for 230 Vac systems and 600 V (Class 1 wire) for
460 or 575 Vac systems.
3. Wire gauge must be selected based on 125% of the continuous input current rating of the drive. Wire
gauge must be selected from wire tables for 75 °C insulation rating, and must be of copper construction.
The 230 V 7.5 and 15 HP models, and the 460 V 30 HP models require 90 °C wire to meet UL
requirements. See
for the continuous output ratings for the drive.
4. Grounding must be in accordance with NEC and CEC. If multiple X5 drives are installed near each
other, each must be connected to ground. Take care not to form a ground loop.
See
for a summary of wiring specifications.