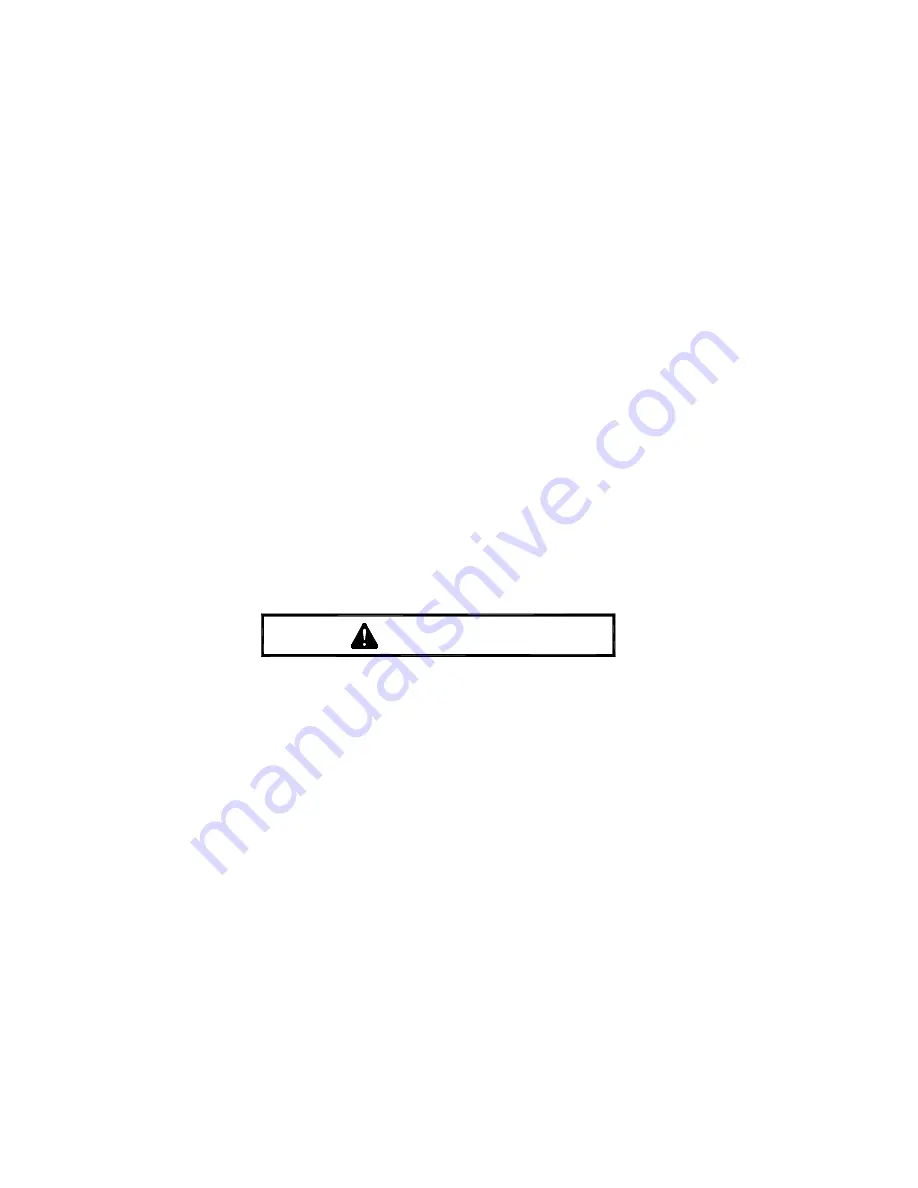
2
Vacuum System Operation
and Maintenance Manual
VAC-CON
Safety Instructions
Most accidents that involve product operation, maintenance and repair are caused by failure to observe basic safety
rules or precautions. An accident can often be avoided by recognizing potentially hazardous situations before an
accident occurs. A person must be alert to potential hazards. This person should also have the necessary training,
skills and correct tools to perform these functions properly.
Improper operation, lubrication, maintenance or repair on this product can be dangerous and could result in injury
or death.
DO NOT operate or perform any lubrication, maintenance or repair of this product until you have read and
understood the information provided to you by the manufacturer.
Safety precautions and warnings are provided in this manual and on the equipment. It is your responsibility to read
and understand these precautions for your own safety. If these warnings are not followed, bodily injury or death
could occur to you or other persons.
The hazards are identified by the
safety alert symbol
and followed by a
signal word
such as
CAUTION,
WARNING OR DANGER
as shown below.
WARNING
The message that appears under the
signal word
explains the hazard and can be either written or pictorially
presented.
Vac-Con Inc. cannot anticipate every possible circumstance that might involve a potential hazard. The warnings in
this publication and on the product are therefore not all inclusive. If a tool, procedure, work method or operating
technique that is not specifically recommended by Vac-Con Inc. is used, you must satisfy yourself that it is safe by
the operation, lubrication, maintenance or repair procedure that you choose.
The information, specifications and illustrations in this publication are based on the information that was available at
the time the publication was written. The specifications, torque values, pressures, measurements, adjustments,
illustrations, tools, part numbers and other items may change at any time. These changes can affect the service that
was given to the product. Always contact your Vac-Con Inc. dealer to obtain the most complete and current
information before starting any repair.