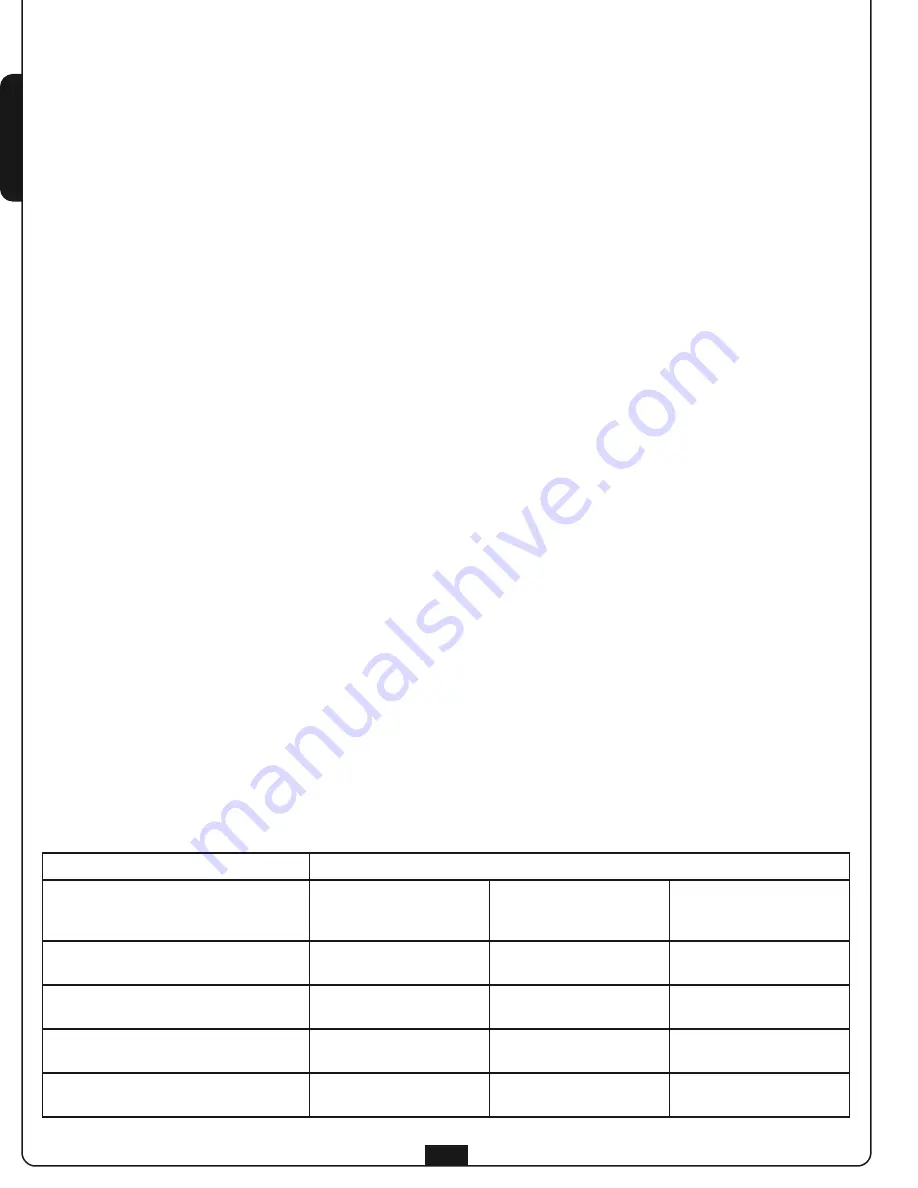
EN
GLIS
H
42
1 - GENERAL SAFETY INFORMATION
Prior to proceeding with installation, it is essential the instructions be read in full, since they contain important information
regarding safety, installation, use and maintenance.
• Anything not expressly described in these instructions is prohibited; unforeseen uses may be a source of danger to people and property.
• Do not install the product in explosive environments and atmospheres: the presence of inflammable gases or fumes is a serious safety
hazard.
• Do not make any modifications to any part of the automation device, or the accessories connected to it, unless described in this manual.
• Any other modifications will void the warranty on the product.
• The installation steps should be conducted so as to avoid rainy weather, which can expose electronic circuits to dangerous water
seepage.
• All operations requiring the casing of the device to opened should be performed with the control unit disconnected from the electricity
supply and with a warning notice displayed, for example: ”CAUTION, MAINTENANCE IN PROGRESS”.
• Avoid exposing the device close to sources of heat and flame.
• In the event of interventions on automatic or differential breakers or fuses, it is essential that faults be identified and resolved prior to
resetting. In the case of faults that cannot be resolved using the information to be found in this manual, consult the V2 customer
assistance service.
• V2 declines all responsibility for failure to comply with good construction practice standards in addition to structural deformation of the
gate that might occur during use.
• V2 reserves the right to make modifications to the product without prior warning.
• Installation/maintenance personnel should wear individual protection devices (IPDs), such as overalls, safety helmets, boots and gloves.
• The ambient operating temperature should be that indicated in the technical characteristics table.
• The automation device should be shut down immediately in the event of any anomalous or hazardous situation; the fault or malfunction
should be immediately reported to the person responsible.
• All safety and hazard warnings on the machinery and equipment should be complied with.
• Electromechanical actuators for gates are not intended to be used by people (including children) with diminished physical, sensory or
mental capacity, or lacking in experience or knowledge, unless they are under supervision or have been instructed in use of the actuator
by a person responsible for safety.
• DO NOT introduce objects of any kind into the compartment below the motor cover.
The compartment should remain free in order to aid with motor cooling.
1.1 - PRELIMINARY CHECKS AND IDENTIFICATION OF THE TYPE TO BE USED
The automation device should not be used until installation, as specified in “Testing and start-up”, has been performed.
It should be remembered that the device does not compensate for defects caused by improper installation, or poor maintenance, thus,
prior to proceeding with installation, ensure that the structure is suitable and meets current standards and, if necessary, perform any
structural modifications aimed at the implementation of safety gaps and the protection or segregation of all crushing, shearing and transit
zones, and verify that:
• The gate has no friction points, either during closing or opening.
• The gate is well balanced, i.e. there is no tendency to move spontaneously when stopped in any position.
• The position identified for fixing the motor reducer allows easy and safe manual manoeuvring, compatible with the size of the motor
reducer itself.
• The support on which the automation device will be fixed is solid and durable.
• The mains power supply to which the automation device is connected has a dedicated safety earthing system and differential breaker
with tripping current less than or equal to 30 mA (the breaker gap distance should be greater than or equal to 3 mm).
Warning: The minimum safety level depends on the type of use; please refer to the following outline:
Closure use type
Type of activation commands
Group 1
Informed people
(use in private area)
Group 2
Informed people
(use in public area)
Group 3
Informed people
(unlimited use)
Man-present command
A
B
Not possible
Remote control and closure in view
(e.g. infrared)
C
or
E
C
or
E
C
and
D
or
E
Remote control and closure not in view
(e.g. radio)
C
or
E
C
and
D
or
E
C
and
D
or
E
Automatic control
(e.g. timed closure control)
C
and
D
or
E
C
and
D
or
E
C
and
D
or
E
Summary of Contents for ZARISS-M
Page 2: ......
Page 14: ...ENGLISH 52 Phase power supply 230Vac Earth Neutral power supply 230Vac ...
Page 42: ...ENGLISH 80 ...