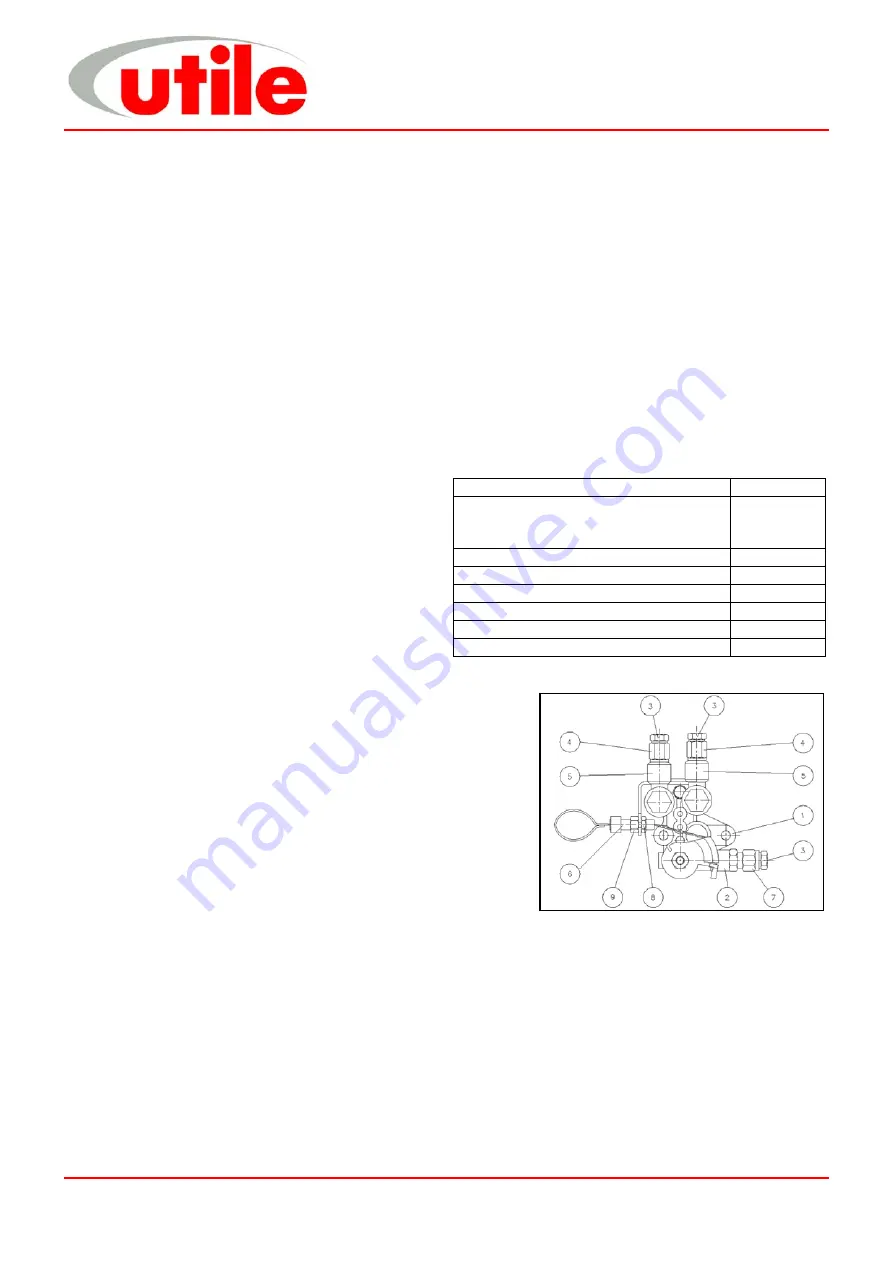
The Utile Engineering Co. Ltd.
27/11/03
Irthlingborough, Northamptonshire. England
Tel: +44 (0) 1933 650216
Fax: +44 (0) 1933 652738
9
IC162
Operating Notes
Daily, check the oil drip rate through the indicator. Fill the oil tank.
After the initial running in period, check the belt tension. Belt squeal denotes a loose belt that requires
tightening.
Inspect the filter fitted to the inlet, regularly clean and renew the element when necessary.
Excessive discharge temperature for normal operation as indicated by the rise in temperature shown in the
log book indicates inadequate cooling, faulty lubrication or a dirty intake filter. The machine should be
stopped and inspected.
Check the machine internally for wear every 10,000 running hours. (see Inspection and Service)
The blade depth should be checked after the initial 2,000 running hours and thereafter every 5,000 running
hours for wear and renew if the rubbing tips have worn to a depth of 83mm. (see Check Blade Wear).
Condensate if allowed to enter the machine can cause severe blade wear.
If adjustment of the oil drip rate is required (see lubrication).
Stopping Procedure
Proceed as follows: -
i. Trip out or Stop the drive motor.
ii. If machine is on a standby service, run for a few minutes each week.
Lubrication
Prime oil pipes prior to initial start and every time
machine is dismantled for service, as serious damage
will occur if the machine runs unlubricated. The
lubrication system is a total loss system, recycling of oil
is not recommended
Standard lubricator drip rate is 45 - 50 dpm each feed at
1000rpm using the standard S8899 drip indicators and
can be increased / decreased pro-rata with the speed.
The recommended grade of oil is
Shell Rimula 15W/40
the typical physical characteristics are shown above: -
Oil pump adjustment
The pump is adjusted to the correct flow rate when despatched from
our works. If it found necessary to alter the oil feed, then proceed as
follows using fig. 7:
1.
Loosen off locking nut (8) from adjusting screw-retaining
bracket.
2.
To decrease flow, back off external nut (9) towards shoulder of
adjusting screw.
To increase flow, tighten external nut (9) onto adjusting
screw-
retaining bracket.
3.
Tighten locking nut (8) onto adjusting screw-retaining
bracket.
Lubricator Maintenance
Refill the oil reservoir regularly to ensure that the oil level is not allowed to fall to a point where air can be drawn
into the oil pump. Use only clean, new oil of the recommended grade. At least once a year, or if the machine has
been out of use for a long period, the oil pump must be thoroughly flushed out with petrol/kerosene to clear any oil
residues that may have solidified in the control ducts. For this operation we recommend the following procedure: -
1.
Stop the machine and disconnect all the oil pipes from the oil pump.
2.
Remove oil reservoir, drain oil and wash out with petrol/kerosene. Drain again ensuring all oil residues are
removed. Replace reservoir and reconnect the oil feed pipe (oil reservoir to oil pump).
3.
Fill the reservoir with petrol/kerosene to cover oil filter element. Loosen oil feed pipe connection at oil pump
end until all air has been expelled. Re-tighten pipe.
4.
Start the machine under no load condition and run until petrol/kerosene begins to flow from oil pump
discharge points. This operation takes approximately 10 – 15 minutes and providing the machine is run
under no load conditions, no damage will occur.
5.
Stop machine, drain oil reservoir and fill with recommended grade of oil. Ensure all oil pipes are primed.
Reconnect oil delivery pipes (oil pump to machine) and start up.
Operating Notes
Stopping Procedure
Lubrication
Fig. 7
Operating Notes
Stopping Procedure
Lubrication
SAE Viscosity Grade
15W/40
Kinematic Viscosity
@ 40ºC cSt
100ºC cSt (IP71)
100.1
14.5
Viscosity Index
(IP226)
135
Pour Point
ºC (IP15)
-27
Density
@ 15ºC kg/l (IP365)
0.890
Flash Point
(PMCC) ºC (IP34)
226
Sulphated Ash
% wt (IP163)
1.1
Total Base Number
mg KOH/g (IP276)
8.0