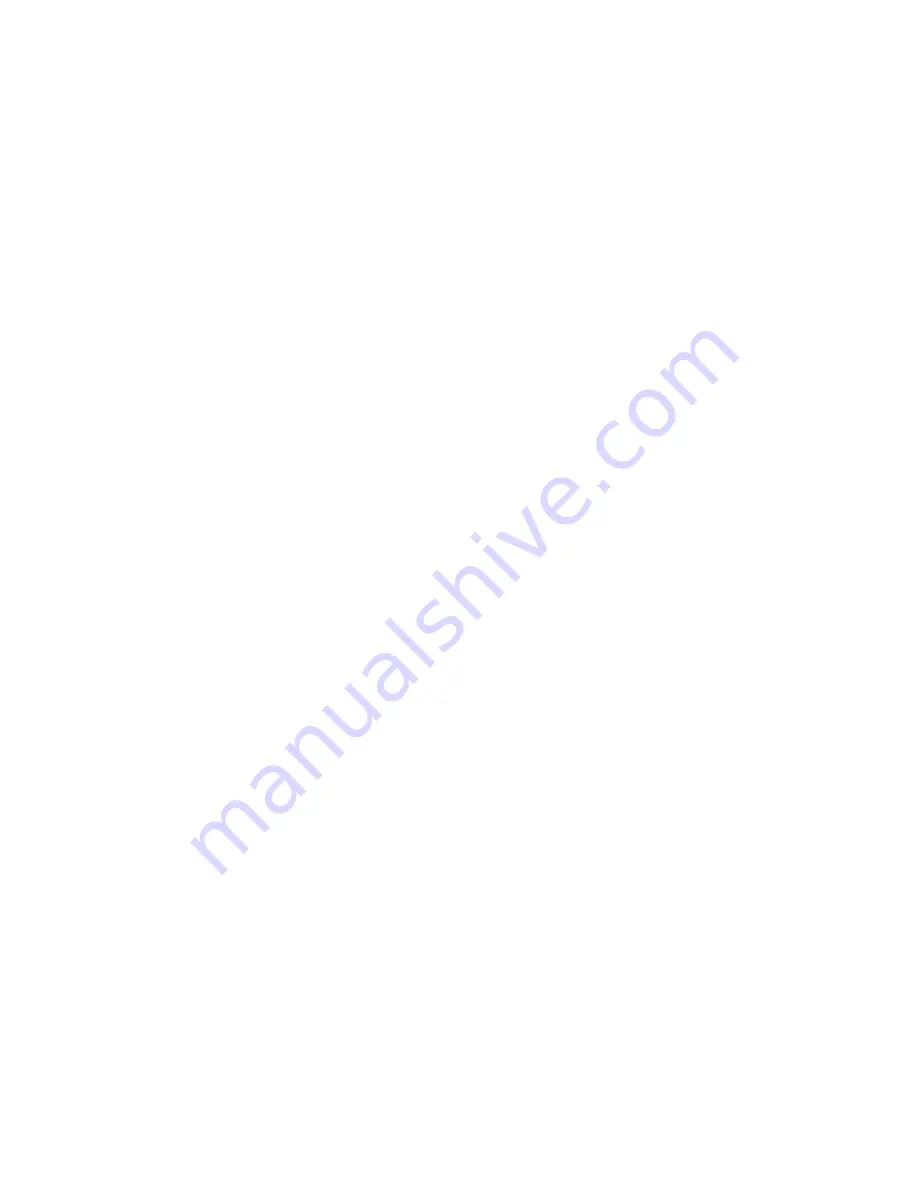
6
5. DESIGN
5.1. A boiler heat exchanger is made of carbon steel sheet and pipes, with fittings welded
together and fixed by reinforced ties - pos. 11.
Other boiler components and units are connected to the heat exchanger with standard or
special fasteners.
Pipelines are connected to the boiler by means of thread joints - pos. 15, 16, 17, 18 19.
5.2. The front part of the boiler has two doors: an upper door - pos. 21, for closing a combustion
gas circulation chamber - pos. 4, and for funnel cleaning, pos. - 3, 5; and a lower door - pos. 22, for
closing a combustion chamber hole - pos. 2, and for fuel loading. Both doors’ opening direction
can be easily changed during operation, by reversing positions of hinges - pos. 26 and a clamping
unit - pos. 27.
The lower door has an inspection hole to monitor the combustion process, which is closed
by a rotating cover - pos. 23.
For safe opening, both doors are provided with handles, pos. 28, with the mounting location
subject to the door opening direction.
5.3. The bottom part of the boiler is equipped with a fan - pos. 32, which delivers air through the
air channel - pos. 12 under boiler fire-grates - pos. 13. The delivered air flow is adjusted with
valves - pos. 31.
5.4. For a better heat removal, funnels of the boiler convective part, pos. 3; 5 are equipped with
smoke spins - pos. 7.
Beside boiler flue pipes, the boiler is connected with a position lock - pos. 9, through a flue
pipe - pos. 6, which is provided with a traction control valve - pos. 8. For cleaning a soot or ash
deposit, this interim flue pipe is provided with a manhole closed with a lid - pos. 10
th
5.5. The entire outer surface of the boiler is insulated with 50 mm heat insulation layer - pos. 29,
from the outside sealed with decorative coating - pos. 30.
5.6. For boiler incoming flow temperature and pressure control, the boiler surface is equipped
with: thermometer - pos. 34 and a contact pressure gauge - pos. 35 with a threaded tap - pos. 36.
5.7. For air supply fan control and boiler emergency mode alarms, the boiler is equipped with a
control console - pos. 33, which, by means of wires and cables, is connected to the fan - pos. 32,
the contact pressure gauge - pos. 35, a temperature sensor, inserted in a slot - pos. 20, and power
line 220V, 50Hz.
5.8. For boiler transfer from one place to another or for loading, the boiler is fitted with two lifting
loops - pos. 38.
5.10. Junction pipes:
-
pos. 15 - return water to boiler
-
pos. 16 – feed water from boiler
-
pos. 17 - draining valve (tap)
-
pos. 18 - safety valve
-
pos. 37 - bypass line for non-return valve
-
pos. 39 - draining valve (not indicated in the Picture, behind the fan)
Note: upon continuous boiler upgrading, there may be slight deviations from the boiler
design, provided in these instructions, without impairing any technical or operational features.
5.11. High-wear components
The list of the components is provided in Table 5.1. Their durability depends mainly on the type
and quality of fuel used, as well as on proficiency of service staff.