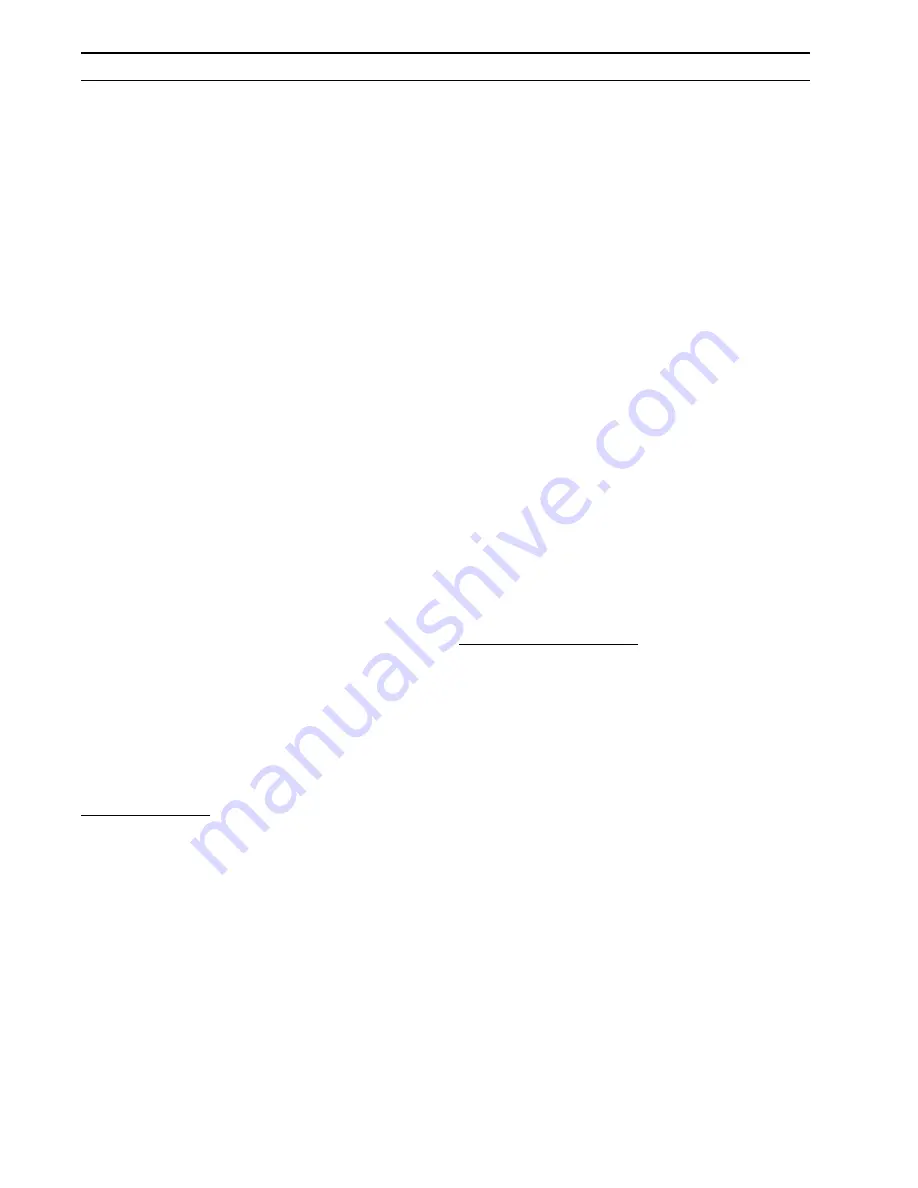
SECTION 5 – SWING DRIVE
5-4
USTC
January 15, 2001
4. Pour approximately 1 tablespoon of ATF Type
F over the friction plates or until the fluid level
is even with the top friction plate.
5. If replacing piston o-rings be sure the two o-
rings are nearest each other with the two backup
rings to the outside.
6. Gently slide piston into case until the large o-
ring tuoches the case. Press down firmly on
piston with the heel of both hands to squeeze o-
rings into the case and seat piston against the
friction plates.
7. If removed, insert the ten springs into the piston.
8. Lay the cover gasket on the case and align the
holes.
9. Set cover over the input end of the shaft. The
bearing should start over the shaft before the
cover touches the spring.
10. Start four cover bolts through the cover and
gasket and into case by hand. Alternately tighten
the cover bolts 1/2 turn at a time until cover is
tight against the case. Torque bolts to 110 lb-ft.
IMPORTANT: Either bolt motor to the brake or plug
the input pilot in the cover before turning brake
upside down or excess fluid will run out.
GEAR REDUCER HUB
The gear reducer transfers power from the motor to
the swing bearing. Motor output speed is reduced
from 36:1 ratio. Motor output torque is consequently
increased by the same ratio.
Hub Disassembly
1. Position reducer over suitable container and
remove magnetic drain plugs from cover and
case. Allow oil to completely drain. Then re-
install drain plugs.
2. Remove cover bolts and lock washers. Carefully
remove cover ensuring that mating surfaces are
not damaged. Discard o-ring seal.
3. Remove input thrust washer and carefully re-
move input gear segment. Discard thrust washer.
4. Remove primary carrier assembly together with
sun gear. Be careful not to damage gear teeth.
5. Remove and discard bolts retaining bearing
retainer plate to output shaft.
6. Place hub in a suitable hydraulic press with the
pinion gear portion of the output shaft down and
blocks supporting the case.
7. Using a suitable drift, carefully press output
shaft from the secondary carrier by applying
pressure to the output shaft. Ensure that the
output shaft is not damaged.
8. Remove roller bearing cone and oil seal from
the output shaft. Discard seal. If applicable,
remove shims from output shaft.
9. Carefully lift secondary carrier assembly out of
case, ensuring that planet and case gear teeth are
not damaged.
10. If necessary, remove roller bearing cone from
secondary carrier.
11. If necessary, remove roller beraring cups from
hub case, ensuring that bearing surfaces on case
are not damaged.
Cleaning and Inspection
1. Thoroughly clean all parts in an approved
cleaning solvent.
2. Inspect bearing cups and cones for damage,
pitting corrosion or excessive wear. If necessary,
replace bearings as a complete set.
3. Inspect bearing mounting surfaces on case,
output shaft and secondary carrier. Replace
components as necessary.
4. Inspect all geared components for chipped or
broken teeth and for excessive or uneven wear
patterns.
5. Inspect primary and secondary planet carriers
for damage, especially in roll pin and planet pin
hole areas. Ensure that gear apertures are not
damaged. Replace as necessary.
6. Inspect all planet pins for scoring or other dam-
age. Replace as necessary.