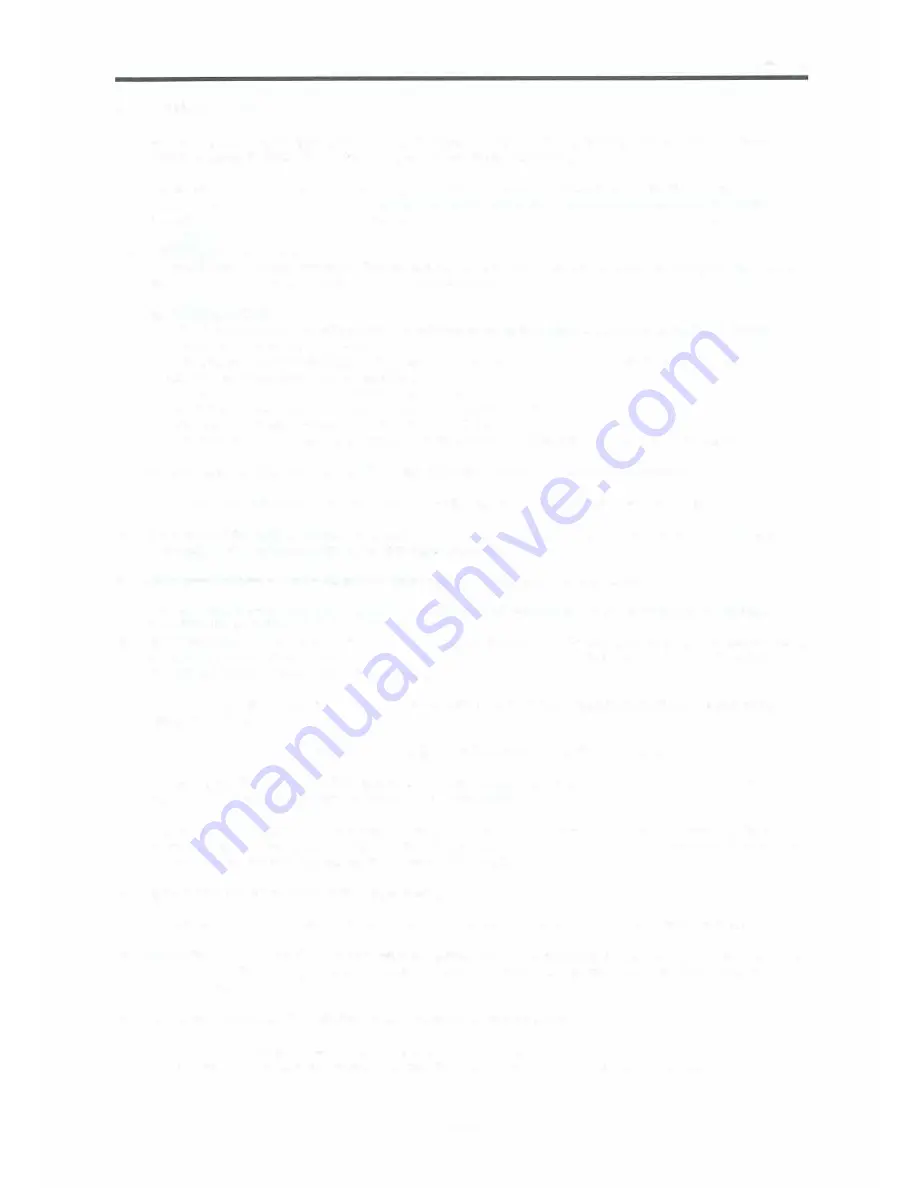
ENGLISH
9. LUBRICATION:
For Air Motor
- Supply light turbine oil properly through air inlet or line lubricator before and atter operation. (For
example, Mobile Turbine Oil #32, Shell Turbine Oil #32 and/or equivalents)
For Bearings
- Supply high quality grease properly (For example, Shell Alvania No. 2, Mobilplex 2 and/or
equivalents) once every three months and when the tool is overhauled. Over-greasing will cause dull motion or
healing.
10. DISPOSAL OF TOOL:
The tool is made of steel, aluminum alloy, casting iron, plastic, rubber and so on. When disposing the tool, make
sure not to cause pollution to human being and environment.
11. MAINTENANCE:
• At least once very three months regular or periodical overhaul by a competent person is needed f or better
performance and trouble-less operation.
• All the spindles, collet chuck, collet chuck nul or other machine parts on insert tools fil should be periodically
inspected and maintained in good condition.
• Use only Uryu's genuine spare parts for replacement.
• Ensure that the data marking on the tool is kepi in a legible condition.
• Maintenance and repair records should be kepi on all tools.
• For further information, contact at any time your nearest URYU distributor or direct to URYU in Japan
Operator's Safety Manuals for URYU DIE Grinders------------------------------------
1.
The air pressure at the tool air inlet shall not exceed the maximum operating pressure 0.63 MPa.
2.
Air hoses and lineshall be relieved of compressed air before being disconnected or disjointed, unless there is an
automatic closing valve protection at the joint being separated.
3.
An accessible means for shutting off air supply should be provided at each tool station.
4.
Air hoses shall be blown out before connection to the tool, and when not in use the air inlet shall be plugged.
5.
Hose coupling shall be securely fitted to the tool and take off point. It an air hose and fittings are not correctly used
or improperly installed, the air hose may come off and whip. Air hose and fittings must be inspected regularly for
damage and wear. Replace them when necessary.
6.
Do not use other than permitted insert tools with correct shank diameter. Cutting-off wheel and routing cutter
wheel shall not be used.
7.
Make sure that allowed speed of the insert tool is higher !han the speed of the die grinder.
8.
Always ensure thai the collet in the machine is the correct size for the shank. It is dangerous to reduce shank
diameter or to force point etc. into an incorrectly matched collet.
9.
When using the mounted point, pay particular attention to the faet that allowed speed of the mounted point is
lowered because of increase of the length of the shaft between the end of the collet and mounted point (overhang).
Make sure !hat minimum gripping length of 10mm is observed.
10. tightened so thai the mounted point is gripped firmly.
11. Do not use incorrectly mounted or damaged insert tools as !his may result in excessive vibration in the collet.
12. Before the to Ensure !hat the collet is compatible with the shank size of the insert tools and collet nul is correctly ol
is connected to the air supply, check the throttle for proper operation (i.e., throttle moves freely and returns to
closed position.)
13. Operators of Pneumatic Die Grinders shall be instructed in their proper use.
A) Keep hands and clothing away from the working end of the tool.
8) Never wear loose-fitting clothes and be careful thai long hair is not drawn in the tool during the operation.
Page2
Summary of Contents for UG-25NA
Page 7: ......