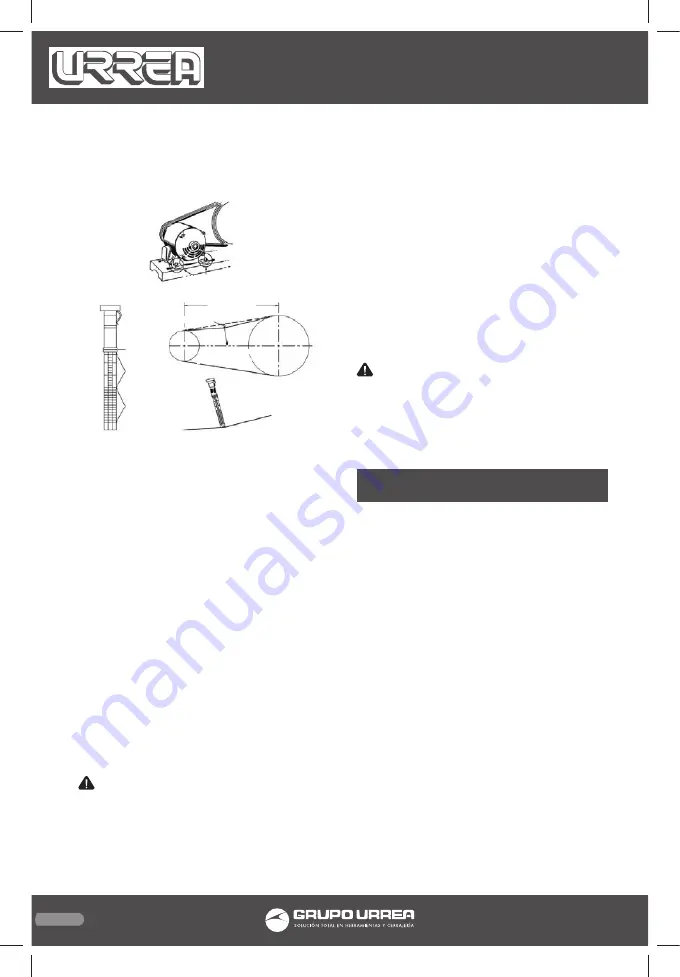
18
Otherwise, the motor can be easily moved by
placing a prying tool beneath it. A commer-
cially available spreader or other belt tension-
ing device can also be helpful.
Follow the procedures outlined below to cor-
rectly set and measure tension.
1. Measure the span length (t) of the drive.
2. Determine the amount of deflection (in
inches) required to measure deflection force
(in pounds) by multiplying the span length (t)
by 1/64. For example, a 32” span length multi-
plied by 1/64 equals 1/2” of deflection required
to measure deflection force.
3. Lay a straight edge across the top outer sur-
face of the belt drive from pulley to sheave.
4. At the center of the span, perpendicular to
the belt, apply pressure to the outer surface of
the belt with a tension gauge. Force the belt
to the predetermined deflection calculated in
step 2. Compare the reading on the tension
gauge to the BELT TENSION TABLE in the DIA-
GRAMS & TABLES section.
Ensure the pulley and sheave are properly
aligned and the motor anchor screws are ad-
equately retightened prior to restarting the
compressor.
CAUTION: Improper pulley/sheave align-
ment and belt tension can result in motor over-
load, excessive vibration, and premature belt
and/or bearing failure.
TANK INSPECTION
The life of an air receiver tank is dependent
upon several factors including, but not limited
to, operating conditions, ambient environ-
ments, and the level of maintenance. The exact
effect of these factors on tank life is difficult
to predict; therefore, URREA recommends that
you schedule a certified tank inspection within
the first five years of compressor service. To ar-
range a tank inspection, contact your closest
service center.
If the tank has not been inspected within the
first 10 years of compressor service, the re-
ceiver must be taken out of service until it has
passed inspection. Tanks that fail to meet re-
quirements must be replaced.
WARNING: Failure to replace a rusted air
receiver tank could result in air receiver tank
rupture or explosion, which could cause sub-
stantial property damage, severe personal
injury, or death. Never modify or repair tank.
Obtain replacement from service center.
TROUBLE SHOOTING:
AIR COMPRESSOR
POWER ON, BUT MOTOR DID NOT RUN,
AND FUSE BREAK OR SWITCH OFF AT
SAME TIME
Input power cable is too long ,or too small. Use
the standard power cable.
Input power voltage is too low. Check the
power voltage.
Outdoor temperature is too low. Use the
heater or change the oil.
The fuse or the over load protector is too
small. Inspect the fuse or over load protector.
Motor problems. Change motor.
The short cut in the power circuit. Inspect the
short cut protectors.
The problem of air switch. Change the air
switch.
THE AIR COMPRESSOR DID NOT WORK IF
THE POWER ON
Power cable is not connect firmly. Connect the
power cable with machines.
Air switch is in “off’ condition. Put the air
switch in “on”.
Air pump do not have the oil[ grease. Fill in the
oil in the middle of oil glass.
ANCHOR BOLTS
BELT SPAN (t)
DIRECTION OF
FORCE APPLIED
DEFLECTION
O-RINGS
DEFLECTION
FORCE SCALE
DEFLECTION
DISTANCE
SCALE
COMP8115 manual.indd 18
30/11/15 5:13 p.m.