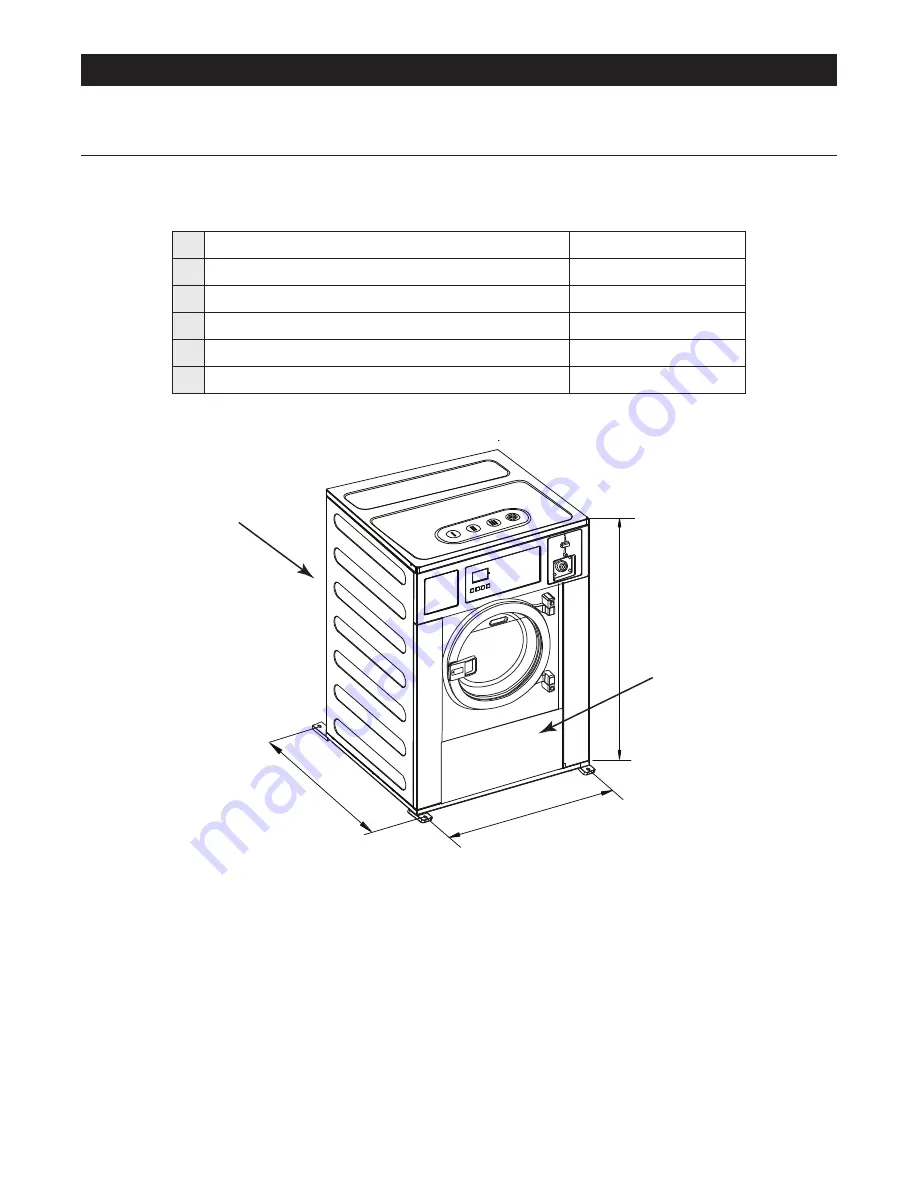
9
Part. 14000101
Rev. 12/2019
®/™ ©2019 Unity Laundry Systems. All rights reserved.
03 INSTALLATION
3.1 REQUIREMENTS OF INSTALLATION LOCATION
The machine must be installed meeting the minimum distances specified to guarantee the proper operation and maintenance
access of the machine.
A
Working area in front of machine - in (mm)
39.4 (1,000)
B
Maintenance area behind machine - in (mm)
31.5 (800)
C
Width - in (mm)
34.6 (880)
D
Depth - in (mm)
34.2 (870)
E
Height - in (mm)
55.1 (1,400)
F
Distance between machines - in (mm)
0 (0)
D
E
F
C
A
B