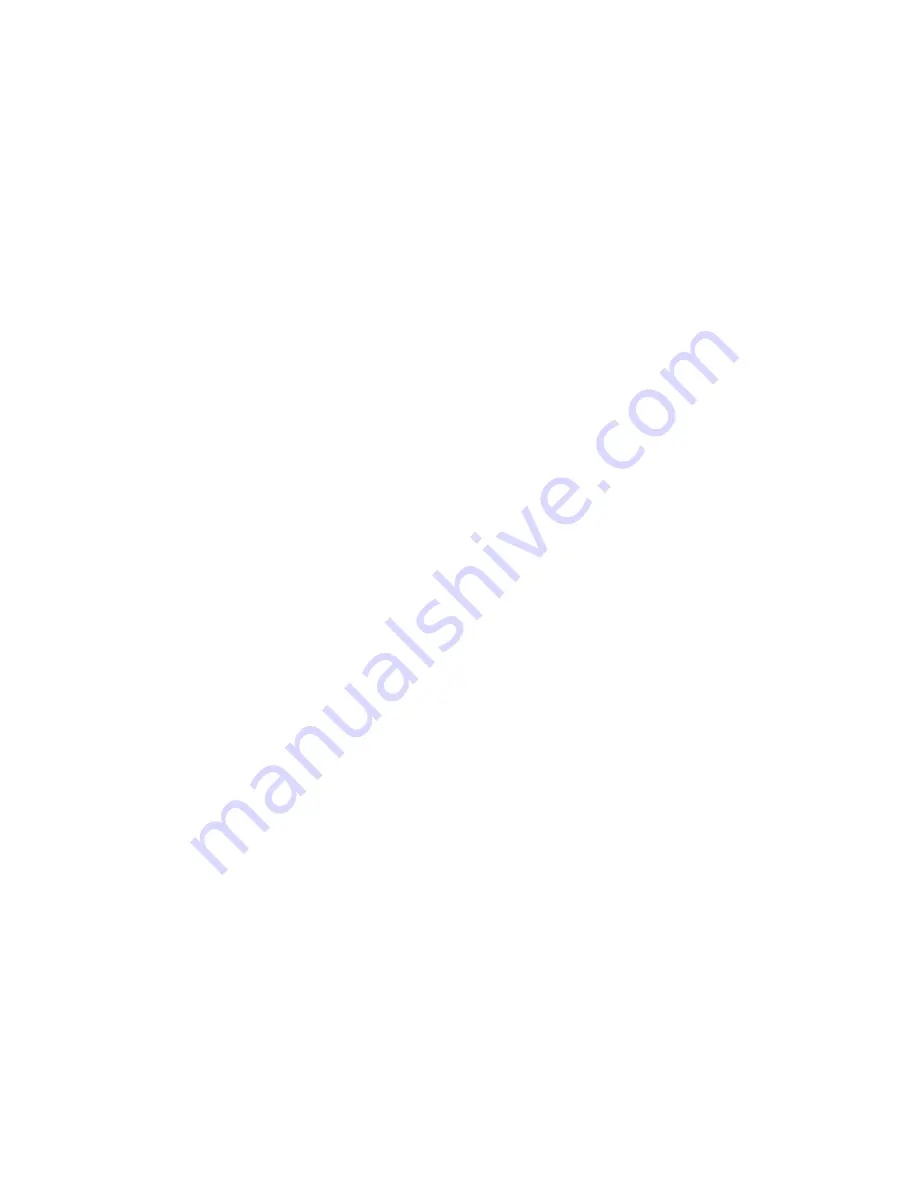
4-13
T-288
Figure 4-11. Model 05G Compressor
b. Installing
NOTE
It is important to check the compressor oil
level of the new compressor.
1. The
original
unloader
valves
must
be
transferred to the replacement compressor.
The plug arrangement removed from the
replacement
is
installed
in
the
original
compressor as a seal. If piston is stuck, it may
be extracted by threading a socket head cap
screw into top of piston. A small Teflon seat ring
at bottom of piston must be removed.
NOTE
The service replacement compressor is
sold without shutoff valves (but with valve
pads). These should be placed on the old
compressor before shipping. Check oil
level in service replacement compressor. If
none add the applicable amount outlined in
section 1.2.b.
2. Remove the high pressure switch and install
on new compressor after checking switch
setting (refer to section 4.11).
3. Install compressor in unit by reversing step
4.18.a. It is recommended using new locknuts
when
replacing
compressor.
Install
new
gaskets on service valves and tighten bolts
uniformly.
4. Attach two lines to the suction and discharge
service valves.
Dehydrate
and evacuate
compressor to 500 microns (29.90” Hg
vacuum = 75.9 cm Hg vacuum). Turn off valves
on both lines to pump.
5. Fully backseat (open) both suction and
discharge service valves.
6. Remove vacuum pump lines and install
manifold gauges.
7. Start unit and check for noncondensibles
8. Check refrigerant level and add if necessary.
9. Check compressor oil level. (Refer to section
4.18.2.) Add oil if necessary.
10. Check compressor unloader operation.
11. Check refrigerant cycles.
4.18.2 Checking the Compressor Oil Level
NOTE
It may be necessary to preheat the coach
and/or operate the system in the Reheat
Mode to keep the compressor fully loaded
throughout this procedure.
a. Operate the coach for at least one-half hour at
fast idle engine speed with the temperature
controls at coolest setting and the compressor
fully loaded (six cylinder operation).
b. Ensure the system is fully charged, as
indicated in section 4.9, and the compressor
crankcase is warm to the touch after fifteen
minutes of operation.
NOTE
If the compressor is not level, an average
between both sight glasses will have to be
made to determine proper oil level.
c. Shut off the A/C system and immediately
record the oil level in the compressor oil level
sight glass(es). The correct level should be
between the “Min” and “Max” marks
on
compressor crankcase adjacent to the sight
glasses. If the oil level is below the “Min” mark,
add oil to the compressor, as outlined in the
following section. If the oil level is above the
“Max” mark, remove oil. If proper oil level is
obtained, the coach can be released into
service.
4.18.3 Adding Oil to the Installed Compressor
CAUTION
The appropriate compressor oil must be
used according to the refrigerant used in the
system. (Refer to section 1.2.b.)
There are three methods of adding oil to the
compressor , as outlined in the procedures that
follow. The oil sump method, paragraph a., is the
preferred method.
a. Oil Sump Method
1. With the system off, connect manifold gauge
set to the compressor service valves. Connect
the blue hose to the suction port and red hose
to the discharge port. (See Figure 4-2.)
2. Frontseat (clockwise) the compressor suction
and discharge service valves.
3. Reclaim the refrigerant in the compressor.
Shut off the reclaimer
and verify that
the
Summary of Contents for Carrier TRANSICOLD 68RM35-604-20
Page 1: ...T 288 Rearmount 68RM35 604 20 R 134a NYCDOT...
Page 20: ...2 3 T 288 Figure 2 2 Automatic High Speed Cool Mode Operation with Reheat TDR 10 SEC...
Page 21: ...2 4 T 288 Figure 2 3 Automatic High Speed Cool Mode Operation No Reheat TDR 10 SEC...
Page 22: ...2 5 T 288 Figure 2 4 Automatic High Speed Heat Mode Operation Below 45_F Ambient TDR 10 SEC...
Page 43: ...5 3 T 288 Figure 5 2 Electrical Schematic Diagam Based on Drawing 68RM35 1038 12 TDR 10 SEC...