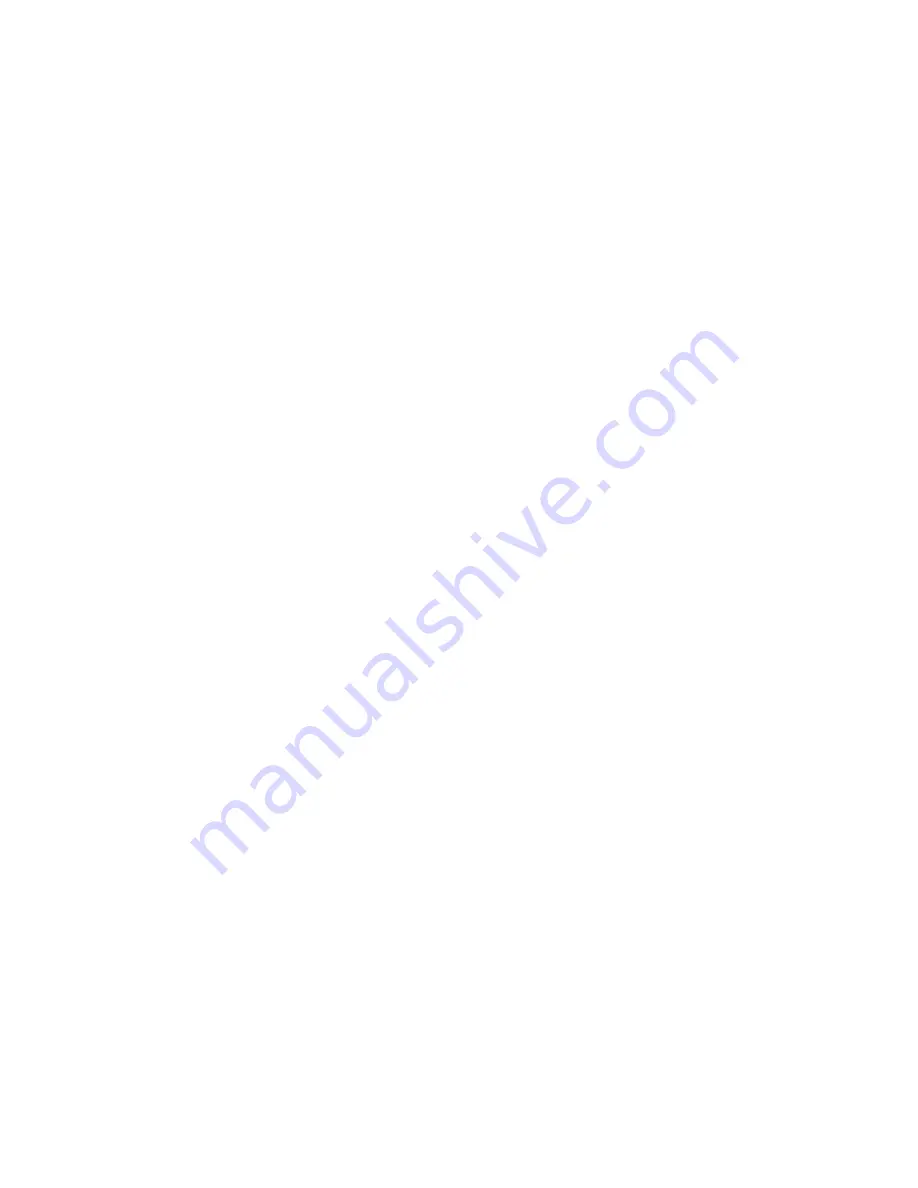
4-3
T-288
4. Backseat filter-drier inlet or outlet valve,
depending upon which one will be used.
5. With manifold set valves frontseated, connect
the high side manifold hose (red) to the filter
drier inlet or outlet valve, whichever one was
backseated in step 4.
6. Frontseat filter drier valve one turn to read high
pressure.
4.4
SYSTEM PUMPDOWN
To service or replace the filter-drier, expansion
valve, evaporator coil, or suction line; pump the
system refrigerant into condenser coil and receiver
tank as follows:
a. Attach the gauge manifold as outlined in
section 4.3.
b. Disconnect low pressure switch quick connect.
Install a jumper wire across switch connection
to prevent the switch from disengaging the
clutch.
c. Start the unit in A/C by placing the driver’s A/C
switch in the cool position. The thermostat
should be set below ambient temperature to
ensure A/C operation.
d. Run unit for 5 -- 10 minutes to allow system to
stabilize.
e. Frontseat (close) the liquid line valve at the
inlet of the filter-drier.
f.
Observe the suction gauge. The pressure will
drop off noticeably. Stop the unit when a 0 to 10
in. vacuum is reached.
g. Stop the unit. Observe the suction gauge. If the
reading increases, restart the unit until the
specified vacuum is achieved.
h. Repeat the above step until the specified
vacuum is maintained after stopping.
i.
Ensure that system pressure is zero psig or
below.
4.5
REMOVING REFRIGERANT CHARGE
A refrigerant recovery system is the recommended
method for removing refrigerant charge. For the
recovery system procedure, refer to instructions
provided by the manufacture.
A refrigerant recovery system should always be
used whenever removing contaminated
refrigerant from the system.
If a recovery system is not available, proceed as
follows:
a. Equipment Required
1. Appropriate evacuated returnable refrigerant
cylinder, preferably a 60 -- 120 lb net capacity
may be used. Refrigerant removal will be faster
and more complete with the larger cylinder.
WARNING
Do not use a disposable refrigerant container
to store the refrigerant, an explosion may
occur.
2. Gauge manifold set.
3. Vacuum pump, preferably 5 cfm (8.5 m
3
/hr)
or larger. CTD P/N 07-00176-01.
4. Weight scale (0 to 100 lb = 0 to 46 kg range,
minimum).
5. A standard 1/4 in. charging hose.
b. To remove the refrigerant charge:
1. Install a manifold gauge set as outlined in
section 4.3.
2. Connect evacuated refrigerant cylinder to the
liquid line valve at the inlet valve of the
filter-drier. The service line to the liquid valve of
the cylinder should be attached loosely. Crack
open the liquid line valve momentarily to purge
service line at cylinder. Tighten connection at
cylinder.
3. Place evacuated refrigerant cylinder on scale
and note weight of empty cylinder. Leave
cylinder on scale.
4. Frontseat liquid line valve at the inlet of the
filter- drier.
5. Run the unit in high speed cool with the
condenser coil completely blocked off. Head
pressure will quickly rise. Stop the unit when
the system pressure reaches 150 psig (for
R-134a) using the rear control switch.
6. Fully open the refrigerant cylinder liquid valve.
Liquid refrigerant will flow from the liquid line
valve to the cylinder. Head (discharge)
pressure will drop.
7. Monitor weight of the refrigerant cylinder to
determine how much refrigerant is being
removed. Shut off cylinder valve when the
scale weight has stabilized, indicating the
refrigerant flow into the cylinder has stopped.
Run the unit for a few more minutes to
Summary of Contents for Carrier TRANSICOLD 68RM35-604-20
Page 1: ...T 288 Rearmount 68RM35 604 20 R 134a NYCDOT...
Page 20: ...2 3 T 288 Figure 2 2 Automatic High Speed Cool Mode Operation with Reheat TDR 10 SEC...
Page 21: ...2 4 T 288 Figure 2 3 Automatic High Speed Cool Mode Operation No Reheat TDR 10 SEC...
Page 22: ...2 5 T 288 Figure 2 4 Automatic High Speed Heat Mode Operation Below 45_F Ambient TDR 10 SEC...
Page 43: ...5 3 T 288 Figure 5 2 Electrical Schematic Diagam Based on Drawing 68RM35 1038 12 TDR 10 SEC...