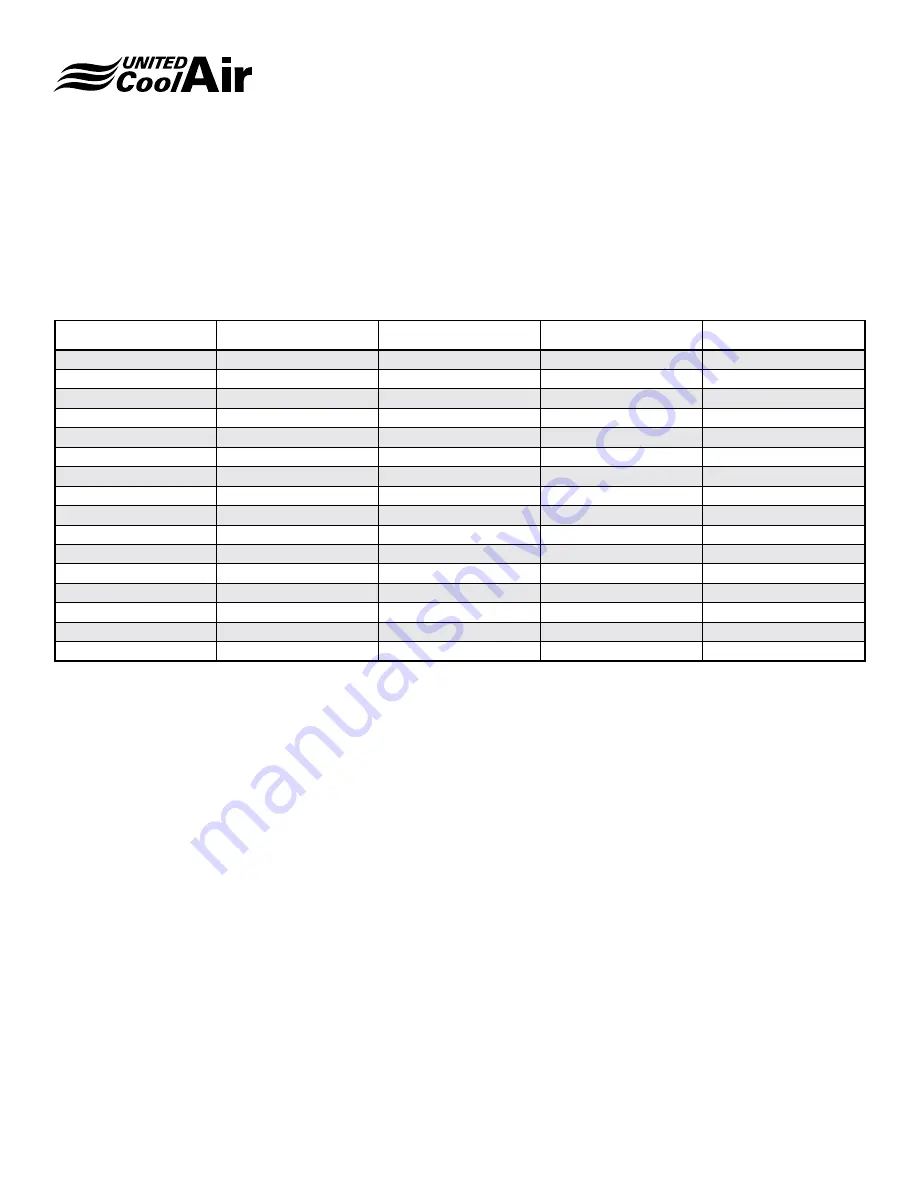
Installation, Operation and Maintenance Manual
VariCool
®
VAV
9
Subject to change without notice.
10.20-IM (0818)
UNIT WEIGHT
Table 3 – Unit Weight shows the weights of each model The
weight of each unit is listed as a standard VariCool without
options Table 4 – Optional Component Weight references
the weights of each optional component or upgrade package
When calculating the weight for each unit, the weight of each
optional component must be added to the standard VariCool
unit weight shown in Table 3
MODEL
BLOWER (lbs)
EVAPORATOR (lbs)
CONDENSER (lbs)
TOTAL (lbs)
AVW08
588
521
592
1701
AVW10
617
550
642
1809
AVW12
699
562
732
1993
AVW16
757
619
796
2172
AVW20
1134
856
910
2900
AVW24
1270
954
1046
3270
AVW26
1305
954
1196
3455
AVW30
1305
989
1216
3510
AVW32
1735
1256
1697
4688
AVW36
1787
1325
1673
4785
AVW40
1805
1387
1847
5039
AVW44
1953
1422
1899
5274
AVW48
1953
1479
1942
5374
AVW52
2087
1489
2227
5803
AVW56
2155
1535
2247
5937
AVW60
2155
1593
2287
6035
Table 3 – Unit Weight
Summary of Contents for AVW08
Page 2: ......