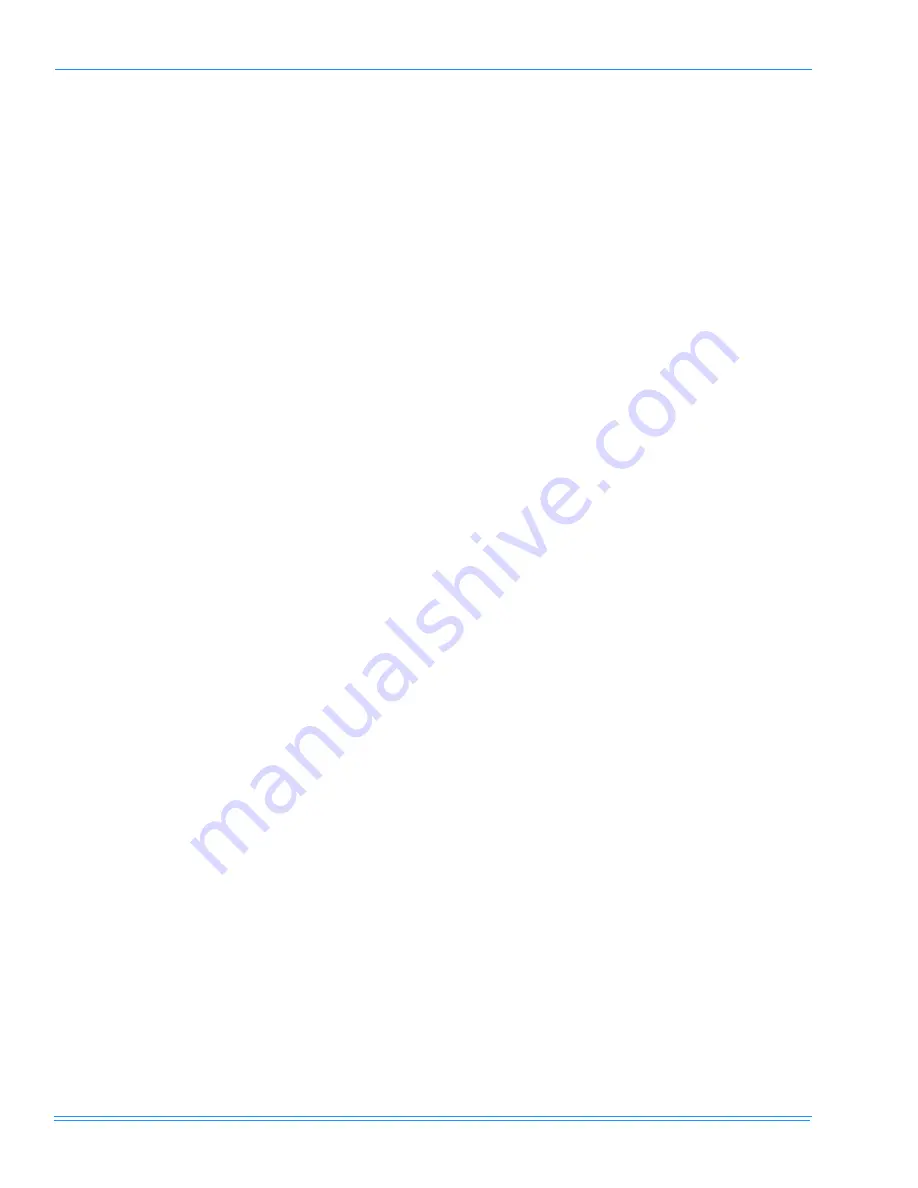
284806-YIM-B-0707
56
Unitary Products Group
3.
If M1 is pulled in and voltage is supplied at M1,
lightly touch the compressor housing. If it is hot, the
compressor may be off on inherent protection.
Cancel any calls for cooling and wait for the inter-
nal overload to reset. Test again when cool.
4.
If M1 is not pulled in, check for 24 volts at the M1
coil. If 24 volts is present and M1 is not pulled in,
replace the contactor.
5.
Failing the above, if voltage is supplied at M1, M1
is pulled in, and the compressor still does not oper-
ate, replace the compressor.
6.
If 24 volts is not present at M1, check for 24 volts at
the UCB terminal, C1. If 24 volts is present, check
for loose wiring between C1 and the compressor
contactor.
7.
If 24 volts is not present at the C1 terminal, check
for 24 volts from the room thermostat at the UCB
Y1 terminal. If 24 volts are not present at the UCB
Y1 terminal, the UCB may have faulted. Check for
24 volts at the Y1 ECON terminal. If 24 volts is not
present at Y1 “ECON”, the UCB has faulted. The
UCB should de-energize all compressors on a loss
of call for the first stage of cooling, i.e. a loss if 24
volts at the Y1 terminal.
8.
If 24 volts are present at the UCB Y1 terminal, the
compressor may be out due to an open high-pres-
sure switch, low-pressure switch, or freezestat.
Check for 24 volts at the HPS1, LPS1, and FS1
terminals of the UCB. If a switch has opened, there
should be a voltage potential between the UCB ter-
minals, e.g. if LPS1 has opened, there will be a 24-
volt potential between the LPS1 terminals.
9.
If 24 volts is present at the UCB Y1 terminal and
none of the protection switches have opened, the
UCB may have locked out the compressor for
repeat trips. The UCB should be flashing a code. If
not, press and release the ALARMS button on the
UCB. The UCB will flash the last five alarms on the
LED. If the compressor is locked out, remove any
call for cooling. This will reset any compressor lock
outs.
NOTE:
While the above step will reset any lock outs,
compressor #2 will be held off for the ASCD,
and compressor #1 may be held off for a por-
tion of the ASCD. See the next step.
10. If 24 volts is present at the UCB Y1 terminal and
none of the switches are open and the compressor
is not locked out, the UCB may have the compres-
sor in an ASCD. Check the LED for an indication of
an ASCD cycle. The ASCD should time out within
5 minutes. Press and release the TEST button to
reset all ASCDs.
11. If 24 volts is present at the UCB Y1 terminal and
the compressor is not out due to a protective
switch trip, repeat trip lock out, or ASCD, the econ-
omizer terminals of the UCB may be improperly
wired. Check for 24 volts at the Y1 “OUT” terminal
of the UCB. If 24 volts is present, trace the wiring
from Y1 “OUT” for incorrect wiring. If 24 volts is not
present at the Y1 “OUT” terminal, the UCB must be
replaced.
12.
For units without economizers
: If 24 volts is present
at the Y1 “OUT” terminal, check for 24 volts at the
Y1 “ECON” terminal. If 24 volts is not present,
check for loose wiring from the Y1 “OUT” terminal
to the Mate-N-Lock plug, the jumper in the Mate-N-
Lock plug, and in the wiring from the Mate-N-Lock
plug to the Y1 “ECON” terminal.
For units with economizers
: If 24 volts is present at
the Y1 "OUT" terminal, check for 24 volts at the Y1
"ECON" terminal. If 24 volts is not present, check
for loose wiring from the Y1 "OUT" terminal to the
Mate-N-Lock plug, a poor connection between the
UCB and economizer Mate-N-Lock plugs, loose
wiring from the Mate-N-Lock plug to the
economizer, back to the Mate-N-Lock plug, and
from the Mate-N-Lock plug to the Y1 "ECON"
terminal. The economizer control may have faulted
and is not returning the 24 volts to the Y1 "ECON"
terminal even though the economizer is not
providing free cooling. To test the economizer
control, disconnect the Mate-N-Locks and jumper
between the WHITE and YELLOW wires of the
UCB's Mate-N-Lock plug.
13. The UCB can be programmed to lock out compres-
sor operation during free cooling and in low ambi-
ent conditions. These options are not enabled by
default. They can be checked by local distributors.
For units with factory installed economizers, the
UCB is programmed to lock out compressor opera-
tion when the LAS set point is reached.
For units without factory installed or with field
installed economizers, the UCB allows compressor
operation all the time. This programming can be
checked or changed by the local distributor.