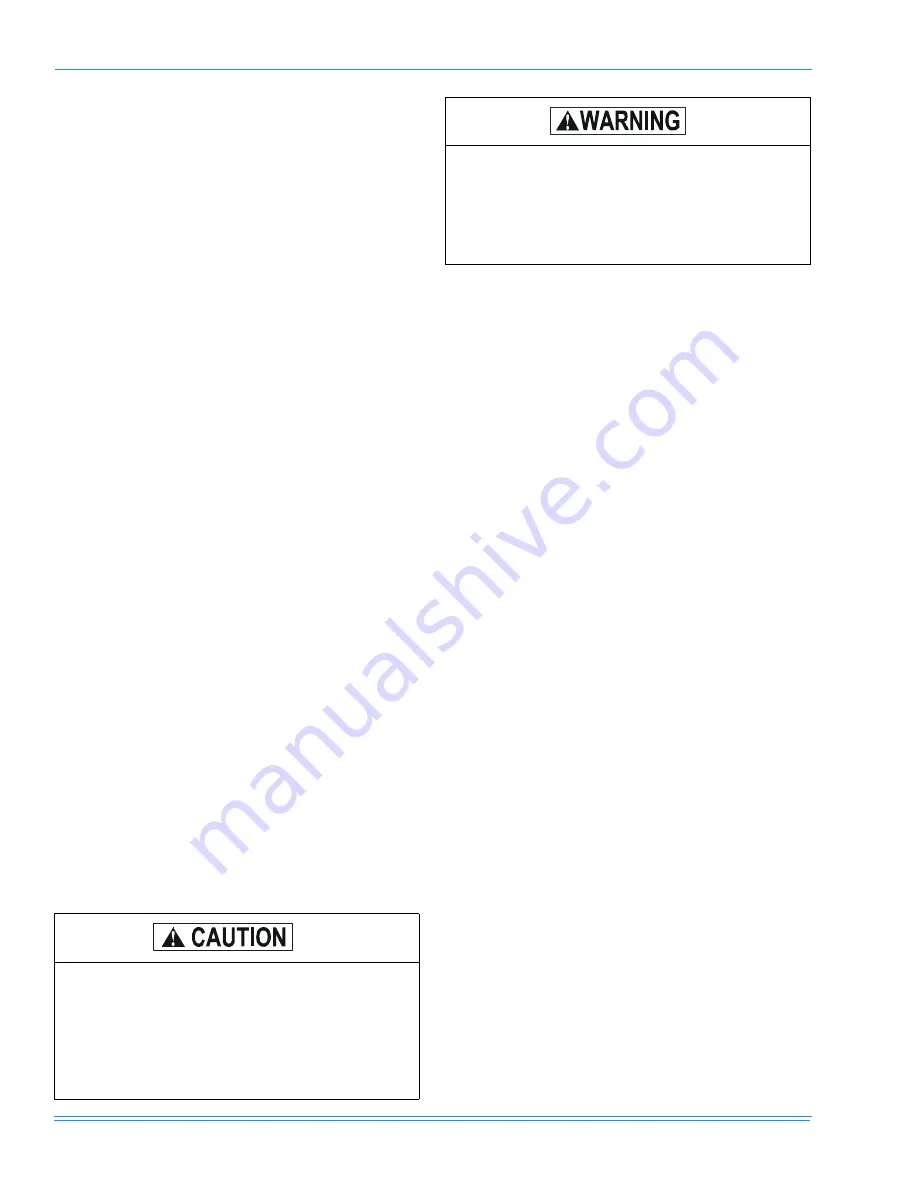
284806-YIM-B-0707
20
Unitary Products Group
FACTORY-INSTALLED VFD
The factory-installed VFD is mounted in the Blower
Access Compartment above the blower assembly. The
drive comes wired from the factory to include both 3-
phase power and control connections (run permit sig-
nal, speed reference signal & fault signal).
All required drive parameters are pre-programmed at
the factory, except in the case of 208-volt applications,
in which the parameter that defines motor nameplate
voltage must be changed to a value of 208.00 and the
parameter that defines motor-rated current must be
changed to the appropriate value appearing on the
motor's nameplate. Refer to the enclosed drive mate-
rial or access the UPGnet Commercial Product Catalog
website for instructions on changing parameter set-
tings.
For units also equipped with gas/electric heat, a termi-
nal block located in the unit's control box and con-
nected to the VAV board's "VAV BOX" terminal, must
be field wired to the building's VAV boxes to ensure
fully open dampers during heating operation.
MANUAL BYPASS
An optional, factory-installed manual bypass switch
available with factory-installed VFD can be found in the
Blower Motor Access compartment and has the follow-
ing three positions:
•
DRIVE
- routes power through the VFD for modu-
lating control of the indoor blower motor.
•
LINE
(or BYPASS) - routes power directly to the
motor which provides full-speed motor operation
and complete electrical isolation of the drive.
•
TEST
- routes power to the VFD but not to the
motor to allow for drive programming and/or diag-
nostics.
If a drive failure occurs, the unit does not automatically
switch to bypass mode. The LINE/DRIVE/TEST switch
must be manually switched to the LINE (BYPASS)
position. If there is a call for the fan, the indoor blower
motor will run at full-speed while in the bypass mode.
BAS-READY VFD
Factory-installed VFD is also available with 'BAS-
ready' models. Terminal blocks are provided in the con-
trol box (in place of the VAV control board) for field wir-
ing of a customer-installed BAS to receive 24 VAC
power and to connect to the following control signals:
•
a duct static pressure transducer input signal (0-5
VDC)
•
an economizer actuator input signal (2-10 VDC)
•
an economizer actuator output signal (2-10 VDC)
•
a VFD speed reference output signal (2-10 VDC)
The use of shielded cable is recommended for the
above control wiring connections.
NOTE:
Factory-installed VFD is not available with fac-
tory-installed BAS options due to space limita-
tions in the control box.
A solid-state, lock-out relay (LR) and 100-
μ
F, 50 VDC
capacitor must be field-supplied and installed to pro-
vide a means to transmit a potential fault signal back to
the BAS controller. The specific relay part number
required will depend upon the need for either AC-out-
put or DC-output. See price pages for further details.
Once the appropriate relay and capacitor are obtained,
install the capacitor across LR terminals '3' & '4' and
make the following wiring connections:
•
LR '1' to BAS controller
•
LR '2' to BAS controller
•
LR '3' to UCB 'X'
•
LR '4' to UCB 'C'
'VFD-READY' FOR CUSTOMER-INSTALLATION
Units configured as 'VFD-ready' provide provisions for
a customer-installed drive. The physical dimensions of
VFDs can vary greatly among manufacturers, horse-
power ratings and voltage requirements. Keep in mind
that drive manufacturers also require various minimum
clearances to allow for adequate internal cooling of the
drive during operation.
If the unit is operated with the manual bypass
switch in the LINE (BYPASS) position and
there are VAV boxes present in the duct sys-
tem, then boxes must be driven to the full-open
position using a customer-supplied power
source to prevent over-pressurizing and possi-
ble damage to the ductwork.
Before beginning any service, disconnect all
power to the drive. Be aware that high voltages
are present in the drive even after power has
been disconnected. Capacitors within the drive
must be allowed to discharge before beginning
service.