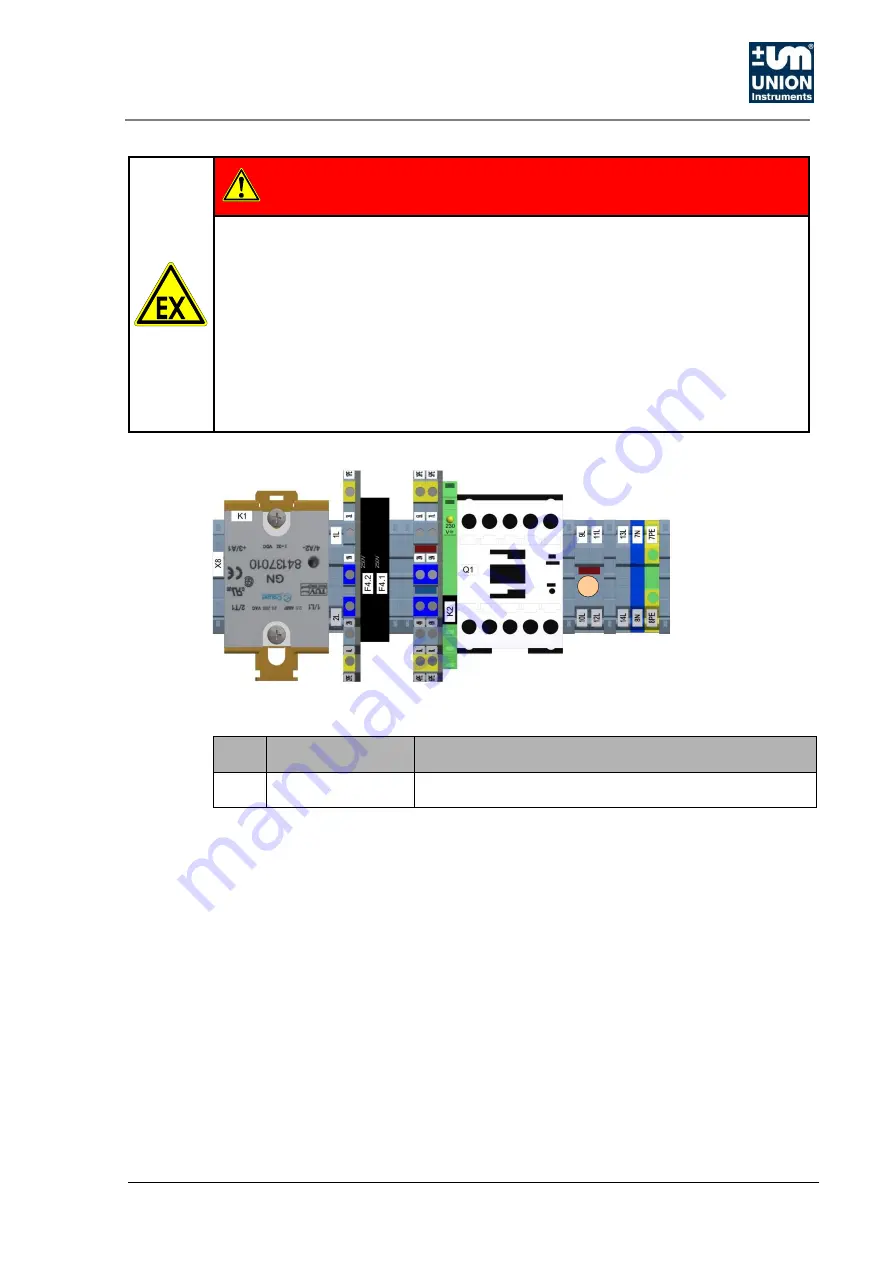
OPERATING INSTRUCTIONS
CWD2005 SPC
chapter
— page:
7
—3
DANGER
Risk of explosion!
If the pressure monitoring system is bridged for maintenance/service work, the
device can be operated permanently without compressed air purging and
overpressure.
There is no protection against explosions!
•
Bridging only for service and maintenance work!
•
Bridging only by authorised trained staff!
•
Use suitable measures /warnings to prevent permanent operation!
Fig. 7.1:
Top hat rail X8, Service bridge
Item
No.
Designation
Function / activity
1
Service bridge
bridge pressure monitoring system, combustion
calorimeter can be used without protection system
1
Summary of Contents for CWD2005 SPC
Page 1: ...Feb 2017 V1 02 OPERATING INSTRUCTIONS AND SAFETY NOTES CWD2005 SPC...
Page 4: ...OPERATING INSTRUCTIONS CWD2005 SPC...
Page 10: ...OPERATING INSTRUCTIONS CWD2005 SPC chapter page 2 2...
Page 42: ...OPERATING INSTRUCTIONS CWD2005 SPC chapter page 5 18...
Page 56: ...OPERATING INSTRUCTIONS CWD2005 SPC chapter page 7 8...
Page 58: ...OPERATING INSTRUCTIONS CWD2005 SPC chapter page 8 2...
Page 60: ...OPERATING INSTRUCTIONS CWD2005 SPC chapter page 9 2...
Page 63: ...OPERATING INSTRUCTIONS CWD2005 SPC chapter page 10 3...