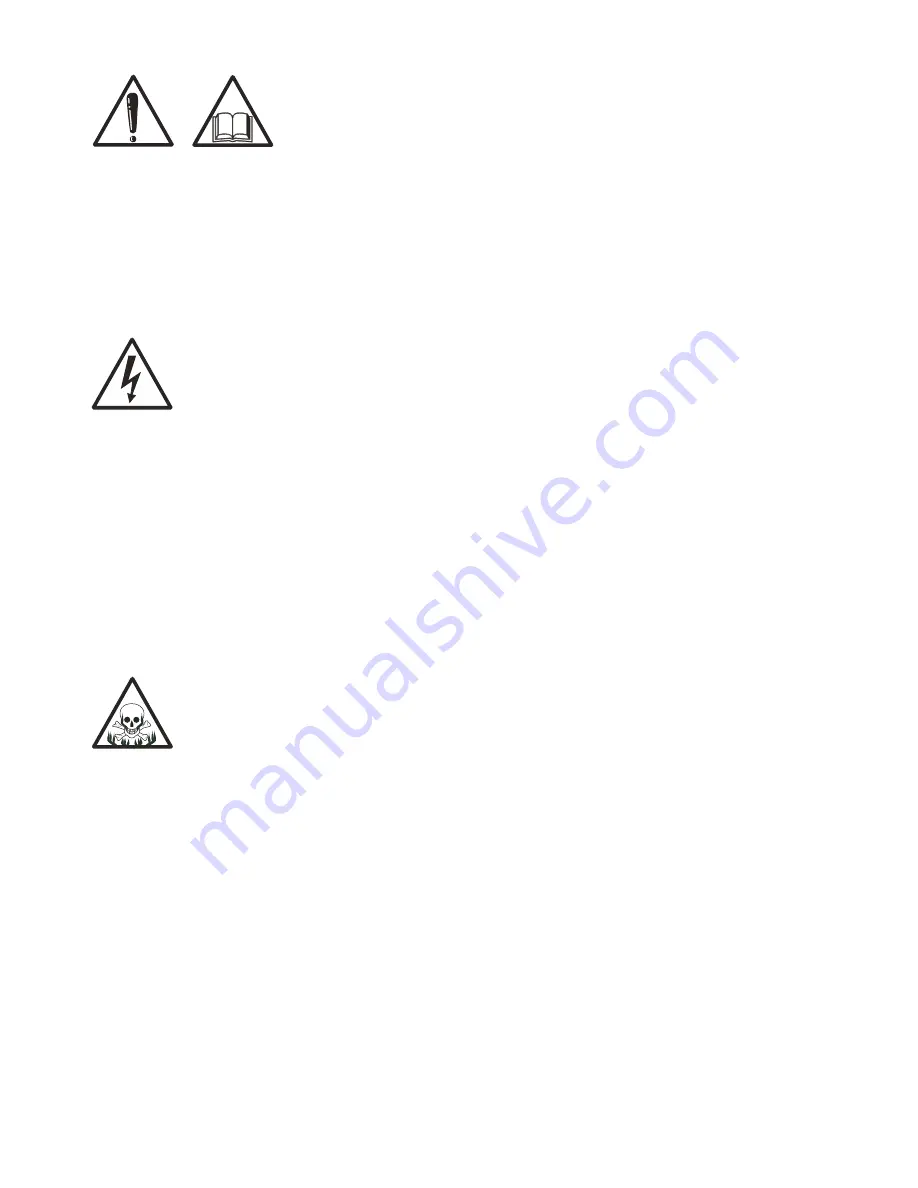
4
SAFETY
IMPORTANT:
BEFORE INSTALLING, OPERATING OR CARRYING OUT
MAINTENANCE ON THE PLASMA CUTTER, READ THE CONTENTS OF THIS
MANUAL CAREFULLY, WHICH MUST BE STORED IN A PLACE FAMILIAR TO ALL
USERS FOR THE ENTIRE OPERATIVE LIFE-SPAN OF THE MACHINE.
PAY PARTICULAR ATTENTION TO THE SAFETY RULES.
THIS EQUIPMENT MUST BE USED SOLELY FOR PLASMA CUTTING.
Electric shock: It can kill. Touching live electrical parts can cause fatal shocks or severe
burns. The plasma nozzle and work circuit is electrically live whenever the output is on.
The input power circuit and internal machine circuits are also live when power is on.
Do not touch live electrical parts or electrodes with bare skin, gloves or wet clothing.
Incorrectly installed or improperly grounded equipment is dangerous.
• Connect the primary input cable according to Australian and New Zealand standards and regulations.
• Disconnect power source before performing any service or repairs.
• Avoid all contact with live electrical parts of the welding circuit, torch nozzle and work piece with bare
hands. The operator must wear dry welding gloves while he/she performs the plasma cutting task.
• Isolate yourselves from both the earth and the work piece.
• Keep cords dry, free of oil and grease, and protected from hot metal and sparks.
• Frequently inspect input power cable for wear and tear, replace the cable immediately if damaged,
bare wiring is dangerous and can kill.
• Do not use damaged, under sized, or badly joined cables.
• Do not drape cables over your body.
• We recommend (RCD) safety switch is used with this equipment to detect any leakage of current to earth.
Fumes and gases are dangerous. Plasma cutting produces fumes and gases. Harmful
fumes and metallic powders are produced during the cutting operation. Metals which are
painted or coated or which contain mercury, zinc, lead and graphite may produce harmful
concentrations of toxic fumes during cutting. Breathing these fumes and gases can be
hazardous to your health.
• Do not breathe the smoke and gas generated whilst welding or cutting, keep your head out of the fumes
• Keep the working area well ventilated, use fume extraction or ventilation to remove welding fumes and
gases.
• In confined or heavy fume environments always wear an approved air-supplied respirator.
Cutting fumes and gases can displace air and lower the oxygen level causing injury or death.
Be sure the breathing air is safe.
• Do not cut in locations near de-greasing, cleaning, or spraying operations. The heat and rays of the arc
can react with vapours to form highly toxic and irritating gases.
• Materials such as galvanized, lead, or cadmium plated steel, containing elements that can give off toxic
fumes when cuttung. Do not cut these materials unless the area is very well ventilated, and or wearing
an air supplied respirator.
• Always read the Material Safety Data Sheets (MSDS) that should be supplied with the material you are
using.These MSDSs will give you the information regarding the kind and amount of fumes and gases that
may be dangerous to your health.
MACHINE OPERATING SAFETY
Plasma cutting equipment can be dangerous to both the operator and people in or near the surrounding
working area, if the equipment is not correctly operated. Equipment must only be used under the strict and
comprehensive observance of all relevant safety regulations. Read and understand this instruction manual
carefully before the installation and operation of this equipment.
Summary of Contents for RazorCut 45 KUPJRRW45
Page 16: ...16 Spare Parts IdentiFIcation KUPJRRW40...
Page 22: ...22 NOTES...
Page 23: ...23 NOTES...