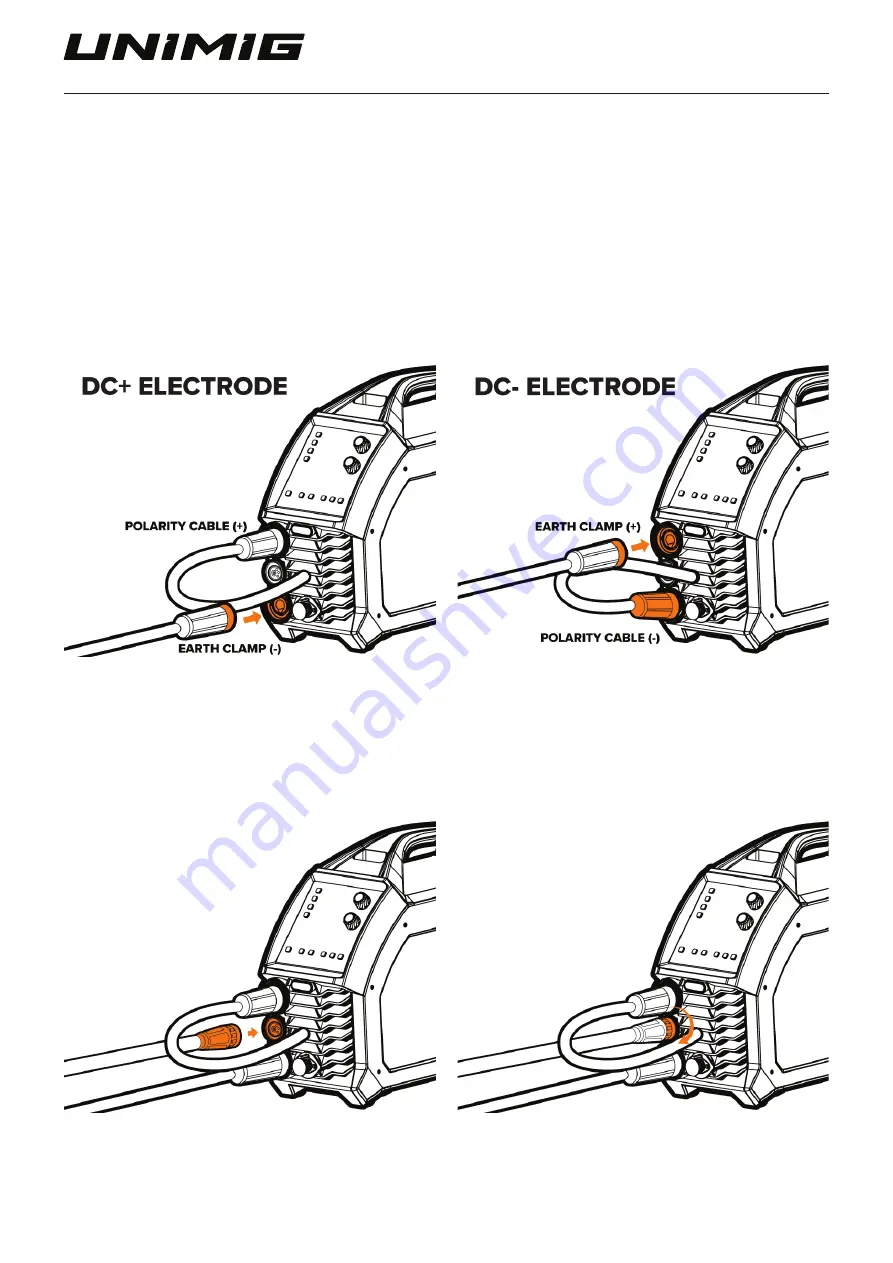
19
RAZOR MULTI 175/220
OPERATING MANUAL
5.
Based on what type of wire you wish to run, you need
to set the machine up in either DC Electrode
(+)
or DC
Electrode
(-)
. Most MIG welding is done with DCEP
(+)
, so plug the polarity cable into the
(+)
dinse port.
Connect the earth clamp into the
(-)
dinse port.
6.
For DCEN
(-)
, plug the polarity cable into the
(-)
dinse
port, and the earth clamp into the
(+)
dinse port. DCEN
is used primarily for gasless flux-cored welding.
7.
With the polarity cable and the earth clamp installed
into the correct dinse ports, now install the MIG torch
into the Euro Connect Port. Ensure you line up the
internal ports correctly.
8.
With the torch correctly lined up and pressed inwards,
twist the locking nut to finish the torch installation.
(GAS-SHIELDED)
(GASLESS)
Summary of Contents for RAZOR MULTI 175
Page 1: ...MULTI U11007K U11008K Operating Manual ...
Page 51: ...51 RAZOR MULTI 175 220 OPERATING MANUAL 23 Wiring Diagrams ...
Page 52: ...52 RAZOR MULTI 175 220 OPERATING MANUAL 24 Machine Breakdown and Parts List ...
Page 54: ...54 RAZOR MULTI 175 220 OPERATING MANUAL Notes ...
Page 55: ...55 RAZOR MULTI 175 220 OPERATING MANUAL Notes ...