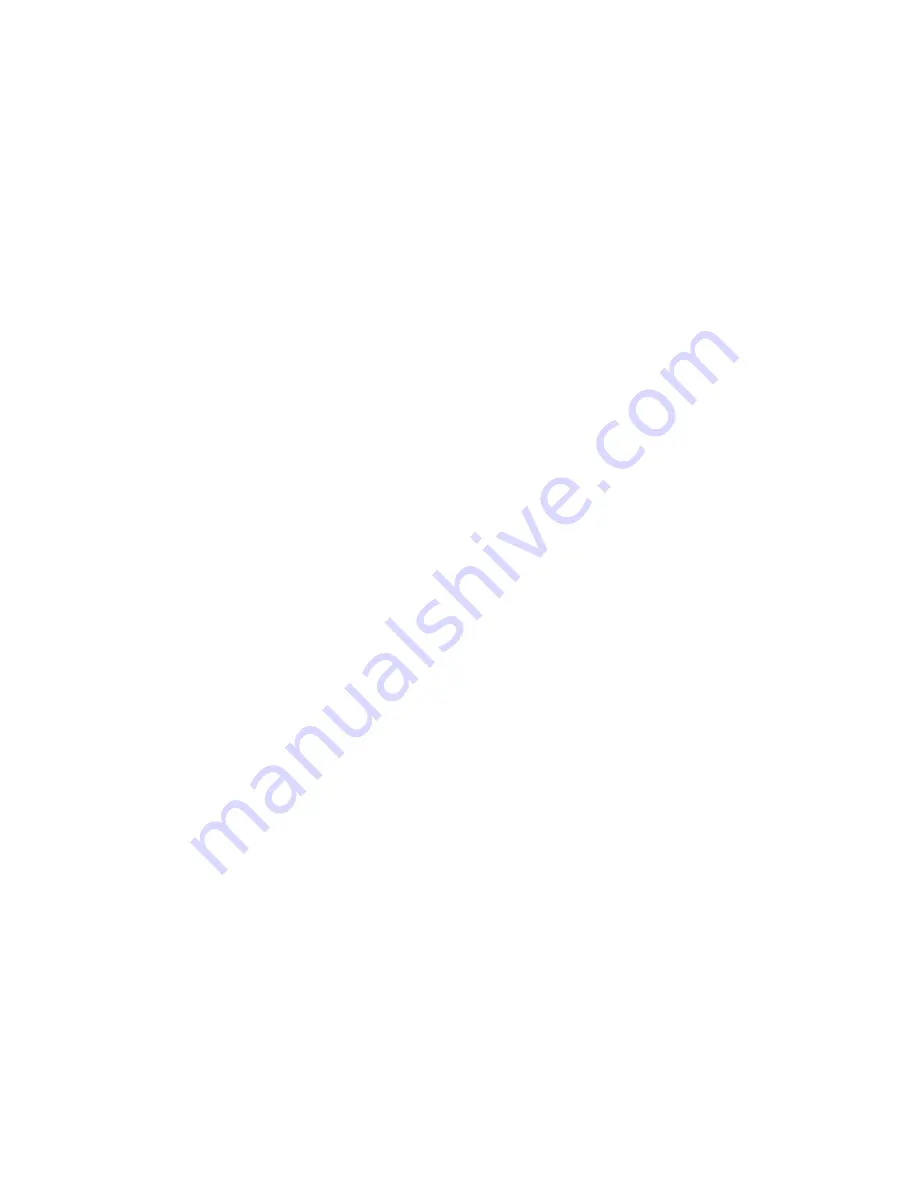
34
At initial set up and at regular intervals we recommend to check for gas leakage.
Recommended procedure is as follows:
1. Connect the regulator and gas hose assembly and tighten all connectors and clamps.
2. Slowly open the cylinder valve.
3. Set the flow rate on the regulator to approximately 8-10 l/min.
4. Close the cylinder valve and pay attention to the needle indicator of the contents pressure
gauge on the regulator, if the needle drops away towards zero there is a gas leak.
Sometimes a gas leak can be slow and to identify it will require leaving the gas pressure in the
regulator and line for an extended time period. In this situation it is recommended to open the
cylinder valve, set the flow rate to 8-10 l/min, close the cylinder valve and check after a
minimum of 15 minutes.
5. If there is a gas loss then check all connectors and clamps for leakage by brushing or spraying
with soapy water, bubbles will appear at the leakage point.
6. Tighten clamps or fittings to eliminate gas leakage.
Important:
We strongly recommend that you check for gas leakage prior to operation of
your machine. We recommend that you close the cylinder valve when the machine is not
in use. Welding Guns Of Australia PTY LTD, authorised representatives or agents of
Welding Guns Of Australia will not be liable or responsible for the loss of any gas.
ATTENTION! - CHECK FOR GAS LEAKS
Summary of Contents for KMM180
Page 35: ......