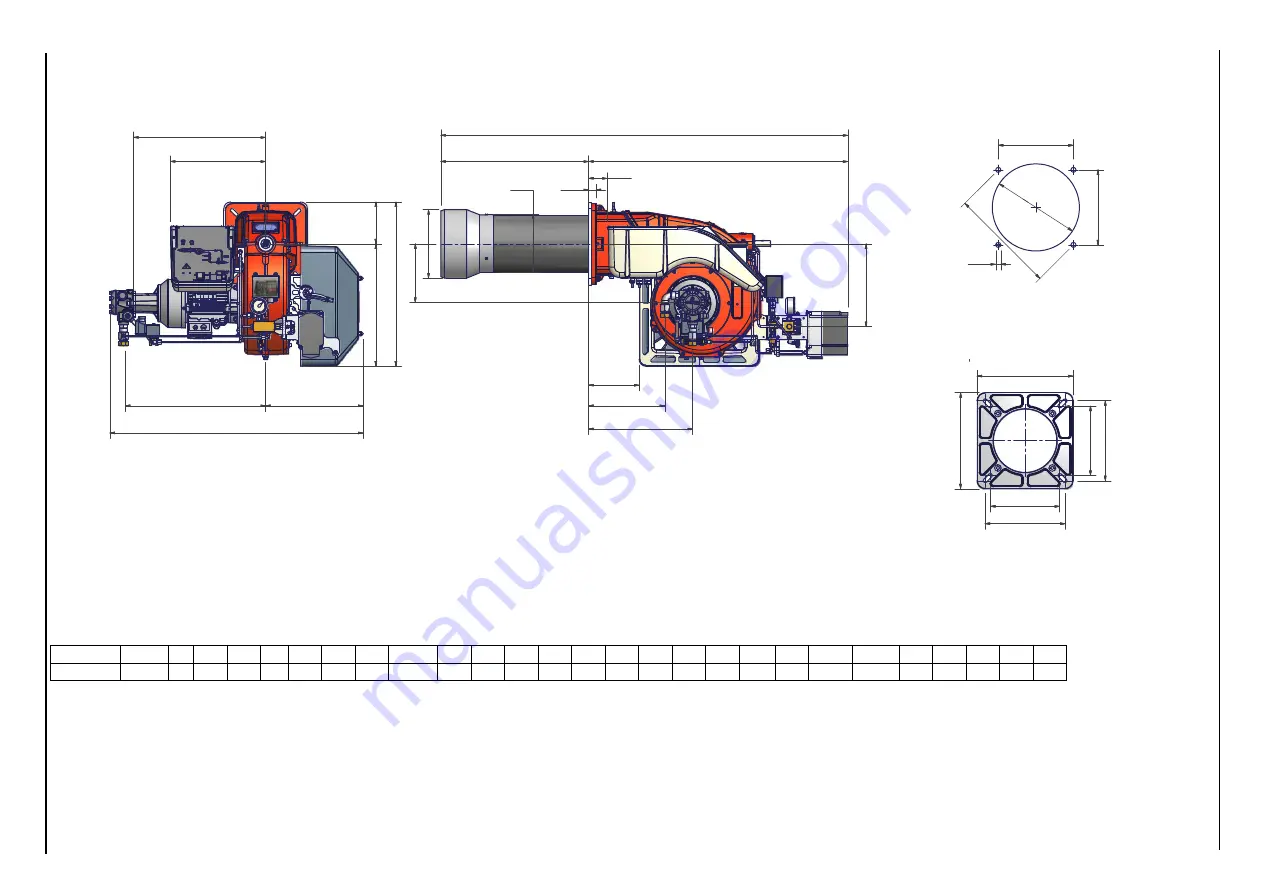
PART I: SPE
CIFICA
TIONS
7
Overall dimensions (mm)
Progressive/Fully modulating version
A
AA AB AC AD AE AH AM
B
BB
C
CC
D
F
G
H
K
L
M
N
Omin Omax
P
T
W
Y
Z
RG75
1508
69 282 217 28 527 385 307
547
489 960 352 938 361 254 270 300 453 M10 330
216
250
233 187 608 221 155
CC
Z
AE
D
F
W
G
B
Y
AD
AA
C
A
AB
A
C
L
T
A
M
AH
BB
M
H
P
P
N
K
K
O min
O max
O
m
in
O
m
a
x
Burner flange
Boiler recommended drilling tem-