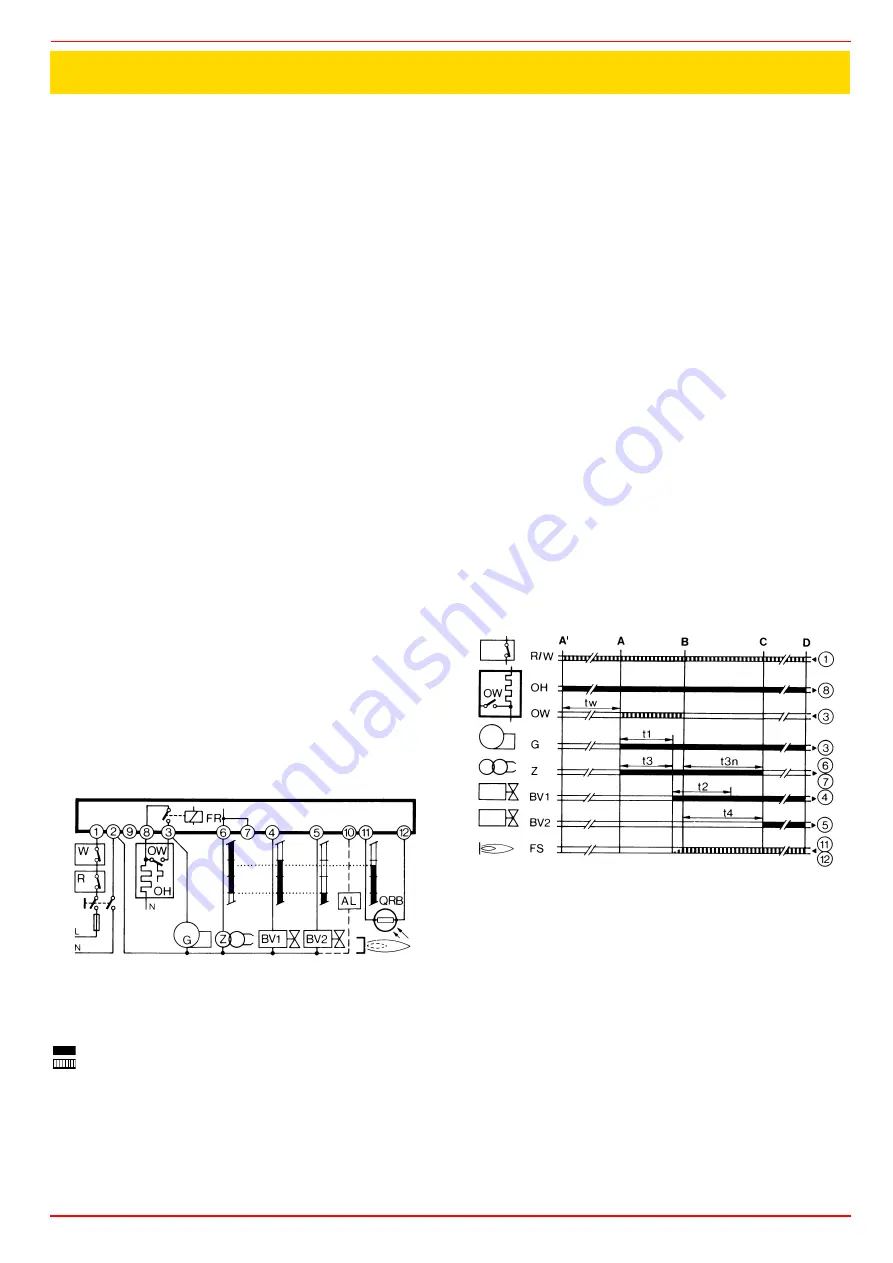
SIEMENS OIL BURNERS AUTOMATIC CONTROLLER LOA24
Use
LOA... safety devices are intended for use solely with QRB... photoresi-
stors, for lighting and controlling low capacity forced air light oil burners
with max. capacity 30 kg/h in accordance with standard DIN 4787.
The One or two flamess are lit through electrical connections with or
without post-ignition.
To replace LAl... AND LAB.. WITH LOA...
LOA... models can be used as replacement for LAl... and LAB.. controllers
by means of the adapter KF8819 and without the need to change the
electrical wiring. Because the LOA is smaller in dimensions, when it is
used with the adapter the external dimensions are almost identical, which
means that there is no need to move the reset button.
Performance
The controllers just need plugging in, so they can be mounted in almost
any position: on the burner, on the electrical panel or on the control panel.
The casing is made of robust heat-resistant plastic and contains:
z
the thermic programmer operating a multiple switch control system
with ambient temperature compensator
z
flame signal amplifier with flame relay
z
warning light indicating lockout and associated sealed reset button.
The plug-in socket, also made of robust heat-resistant plastic, contains
the 12 terminals and also:
z
3 neutral terminals, ready wired up to terminal 2
z
4 earth terminals for earthing the burner
z
2 supplementary terminals numbered “31” and “32”.
The socket has two openings at the bottom for the leads; 5 others with
threaded connection for cable holders PG11 or 3/4UNP for non-metallic
sleeves are located on a mobile stuffing box, one on either side and 3 on
the front.
There are two flexible metal tongues on the sides of the socket for moun-
ting.
To dismantle it only requires gentle pressure with a screw driver in the slot
of the mounting guide. The base dimensions of the socket are exaclty the
same as for types LAB/LAI and there is no difference in the diameter of
the reset button, the two mounting screws and the flange of the burner
earth.
Safety at low voltage levels
Safety devices against any reduction in the mains voltage operate on a
special electronic circuit which, in the event of the power supply falling
below 165V~, stops the burner switching on without releasing the fuel and
locks out the apparatus.
Wiring diagram of the programme
To ensure correct wiring it is essential to observe local standards and fol-
low the instructions of the burner manufacturer with regard to assembly
and start-up.
Program's legend:
Controller output signals
Required input signals
A’Burner start up with light oil pre-heater OH
A
Burner start-up without light oil pre-heater
B
Flame lit
C
Normal operation
D
Normal stop through R
tw
Oil pre-heating time until operational all clear given through
contact OW
tl
Pre-purge time
t3
Pre-ignition time
t2
Safety time
t3n
Post-ignition time
t4
Interval between the flame lighting and energising of solenoid
2a at terminal 5
Internal layout
AL
Optical alarm
BV.
Fuel valve
EK
Reset button
FR
Flame relay
fr
Flame relay contacts
FS
Flame alight signal
G
Burner motor
K
Flame relay anchor to delay the tzl command in the event of a
premature flame signal or endorse it where the signal is
correct.
OH
light oil pre-heater
OW
Operational all-clear contact
QRB Photo-resistant cell (flame detector)
R
Thermostat or pressure switch
TZ
Thermo-electric programmer (bimetal system)
tz..
TZ contacts
V
Flame signal amplifier
W
Safety thermostat or pressure switch
Z
Ignition transformer
The above are safety devices!
To tamper with them in any way may have unforeseeable conse-
quences!
Do not open them!
Technical characteristics
Voltage
220V -15%..240V+10% or
100V -15%...110V+10%
Frequency
50...60Hz +/- 6%
External fuse
max.10A slow action
Contact flow:
- terminal 1
5A
- terminal 3
5A (incl.capacity absorbed by motor and
pre-heater)
Terminal flow:
terminals 4, 5 &10
1A
terminals 6&7
2A
terminal 8
5A
Absorbed cap
3VA
Protection
IP40
Premitted temp:
operational
-20...+60°C
transport & storage
-50...+60°C
APPENDIX