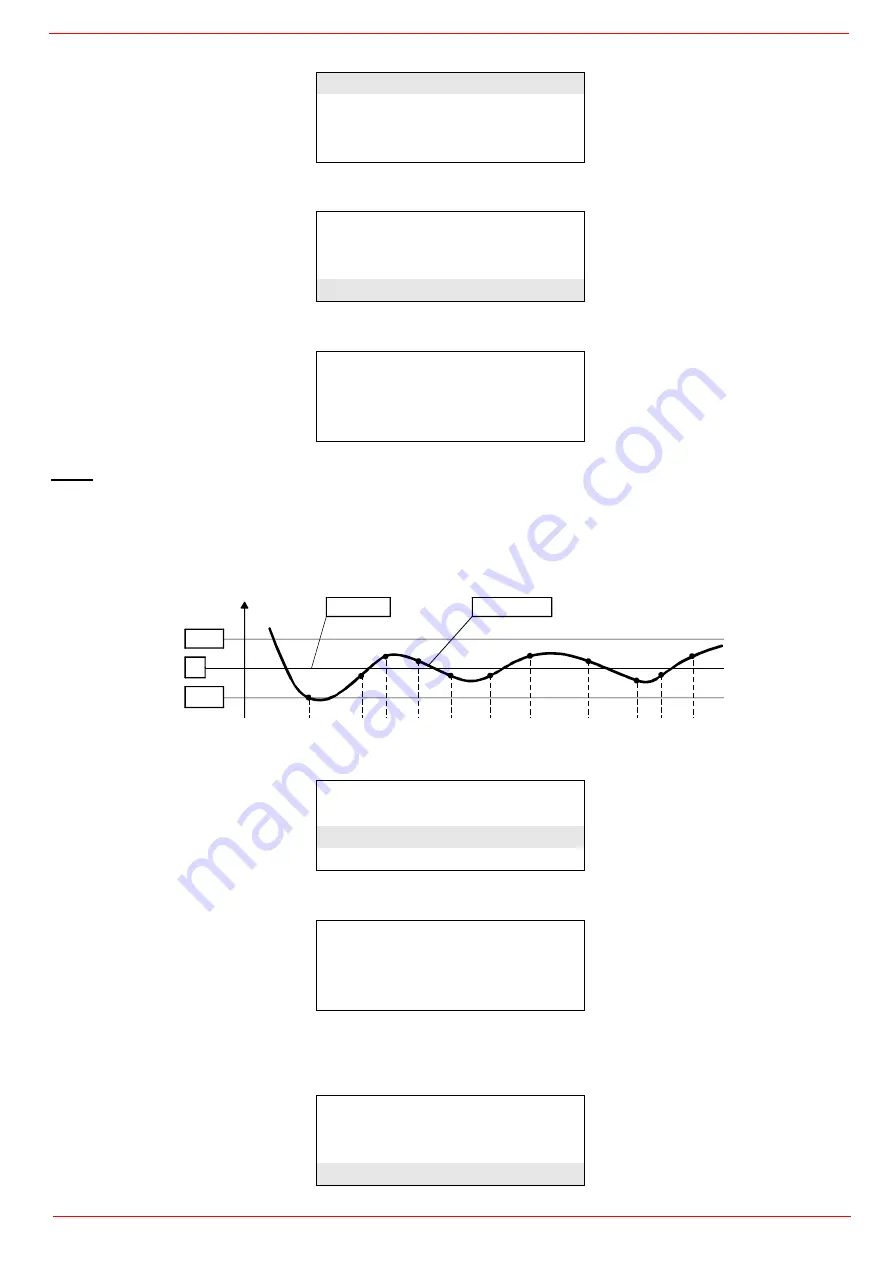
PART III: OPERATION
38
Choose “ControllerParam” and press ENTER: the following menu is shown:
Choose “
SetPointW1
” and press ENTER:
Curr:
it shows the current set-point; use the arrows keys to change.
NOTE:
the availabel range for this parameter depends on the probe provided; the unit measure of the detected value and its limits are
bound up with parameters set at the “Service” level.
Once the new set-point is set, confirm by pressing ENTER, otherwise exit without changings by pressing ESC.
Press ESC to exit the set-point programming mode.
Once the temperature set-point W1 is imposed, set the Switch-on (SDon) and the Switch-off (SDoff) point of the 2-position controller:
To set these values, select the item SD_ModOn (SDOn), by scrolling down the “Load controller” menu with the arrow keys and press
ENTER:
the display will show:
The deafult value for this parameter is1% that is, the burner will light again at a temperature 1% lower than the set-point. Change value,
if needed, by means of the arrow keys; press ENTER to confirm and the press ESC to exit. Press only ESC to exit without changing.
Now choose SD_ModOff always scrolling down theLoad Controller menu, by menas of the arrow keys, and press ENTER.
ControllerParam
Configuration
Adaption
SW Version
ContrlParamList
MinActuatorStep
SW_FilterTmeCon
SetPointW1
SetpointW1
Curr:
90°
New:
90°
SetpointW1
SetpointW2
SD_ModOn
SD_ModOff
SD_ModOn
Curr::
1.0%
New:
1.0%
SetpointW1
SetpointW2
SD_ModOn
SD_ModOff
Setpoint
Actual value
SDoff
W
SDon
Summary of Contents for HR2050
Page 45: ...PART III OPERATION 45 Pump flow rate Nozzle flow rate...
Page 57: ......
Page 58: ......
Page 59: ......
Page 62: ...Annex1 Example for motor cable...
Page 63: ......
Page 64: ...Annex 2 Example for sensor cable...
Page 65: ......
Page 66: ......
Page 70: ......