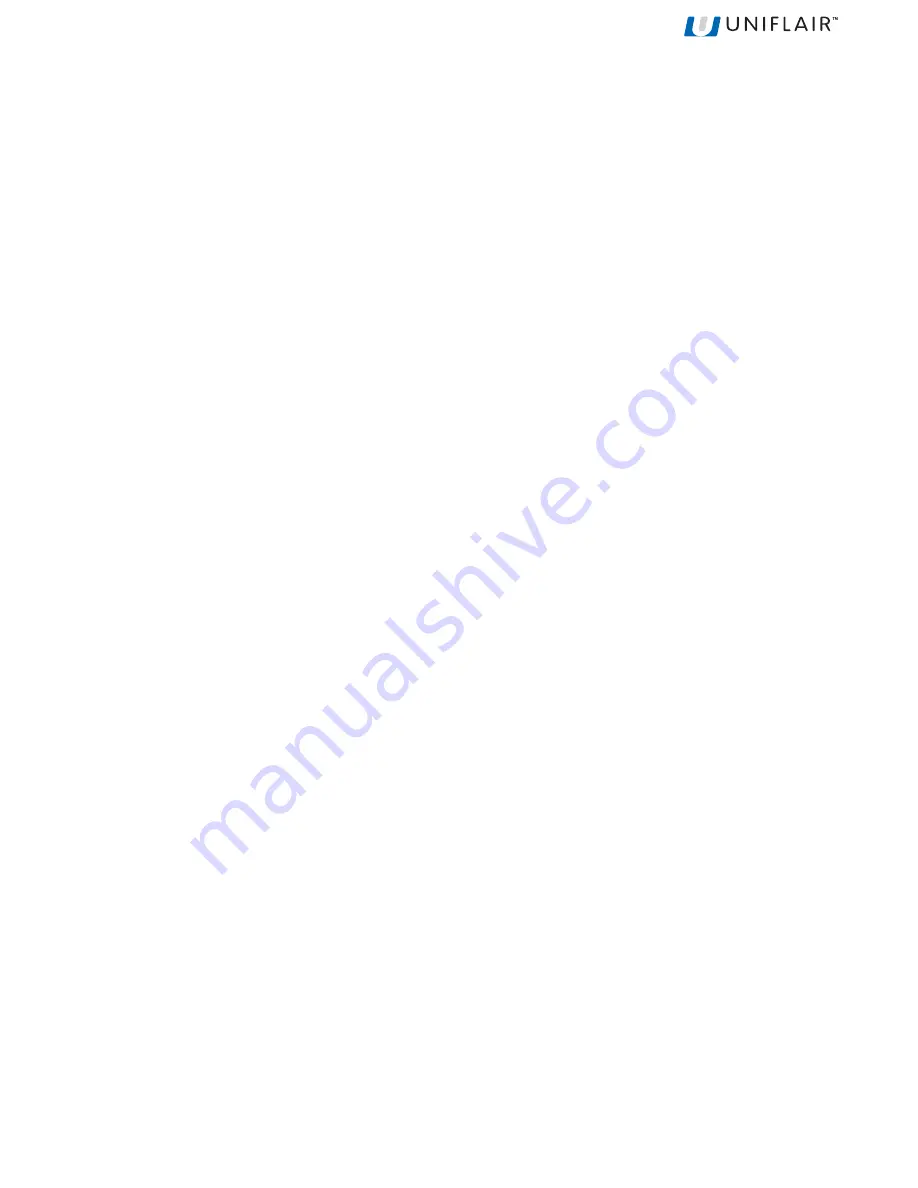
3
GENERAL INSTRUCTIONS
4
Information contained in the manual
4
Symbols
4
Storage
4
Storage after use
4
Disposal
4
Disposal of the machine
4
SAFETY
6
General Instructions
6
Warning for lifting and transportation
6
Warnings for installation
6
Intended use
6
Warnings for use
6
Safety during maintenance work
6
INTRODUCTION
7
Presentation of the system
7
LEONARDO EVOLUTION - DIRECT EXPANSION
10
Technical characteristics
10
Operating description
13
Name and description of the principle components
14
Checks to be made on delivery
17
Unloading the unit
17
Characteristics of the installation area
17
Positioning of the unit
17
Door opening and removal of the panels
18
Door opening
18
Internal protection panels
19
Electrical connections
20
Connection to the drains
21
Connection to the gas drain
21
Refrigerant connections on air cooled units
22
Choosing the diameter of the discharge tube
22
R407C
23
R410A
24
BACKFLOW LINE DIMENSIONING (LIQUID)
27
Type of oil recommended with COPELAND
compressors
29
Type of oil recommended with MANEUROP
compressors
29
Type of oil recommended with SANYO compressors 29
Type of oil recommended with Scrolltech HCJ 072-HLJ
083 compressors
29
Connection for water cooled units
30
MANUAL START UP AND SHUT DOWN OF THE UNIT 31
SETTING AND ADJUSTMENT
32
Selecting the power supply of the fans
32
Setting the regulation and safety devices
35
Setting the pressostatic valve (optional on chilled water
cooled models only)
35
Setting the air flow sensor
35
Setting the dirty filter sensors
35
MAINTANENCE
36
Three-monthly checks
36
Six-monthly checks
36
Annual checks
36
Checks to be performed every sixty months
36
Cleaning and repalcing the filters
36
Troubleshooting
38
LEONARDO EVOLUTION - CHILLED WATER
42
Technical characteristics
42
Operating description
43
Name and description of the principle components
44
Checks to be made on delivery
46
Unloading the unit
46
Characteristics of the installation area
46
Positioning of the unit
46
Opening of the door and removal of the panels
47
Internal protection panels
48
Electrical connections
49
Connection to the water drain
50
Hydraulic connections
51
Filling the hydraulic circuit
51
Filling the primary circuit
51
Filling the hydraulic circuits of the conditioners
51
MANUAL START UP AND SHUT DOWN OF THE UNIT 52
SETTING AND ADJUSTMENT
53
Selecting the power supply of the fans
53
Setting the regulation and safety devices
57
Setting the air flow sensor
58
Setting the dirty filter sensors
58
MAINTENANCE
58
Three-monthly checks
58
Six-monthly checks
58
Annual checks
58
Cleaning and replacing the filters
59
Servomotor and chilled water valve
60
Servomotor and hot water valve
60
Troubleshooting
61
LEONARDO EVOLUTION ENERGY SAVING
63
Technical characteristics
63
Operating description
64
Name and description of the principle parts
65
LEONARDO EVOLUTION TWIN-COOL
69
Technical characteristics
69
Operating description
71
Name and description of the principle components
72
ACCESSORIES
77
Humidifier
77
Operating principle
78
Feed water
78
Connections
78
Maintenance
79
Electric heaters
80
Temperature and humidity sensor
81
Connection to fresh air intake
82
Maintenance
83
Discharge temperature threshold sensor (only on
CHILLED WATER models)
83
Contents