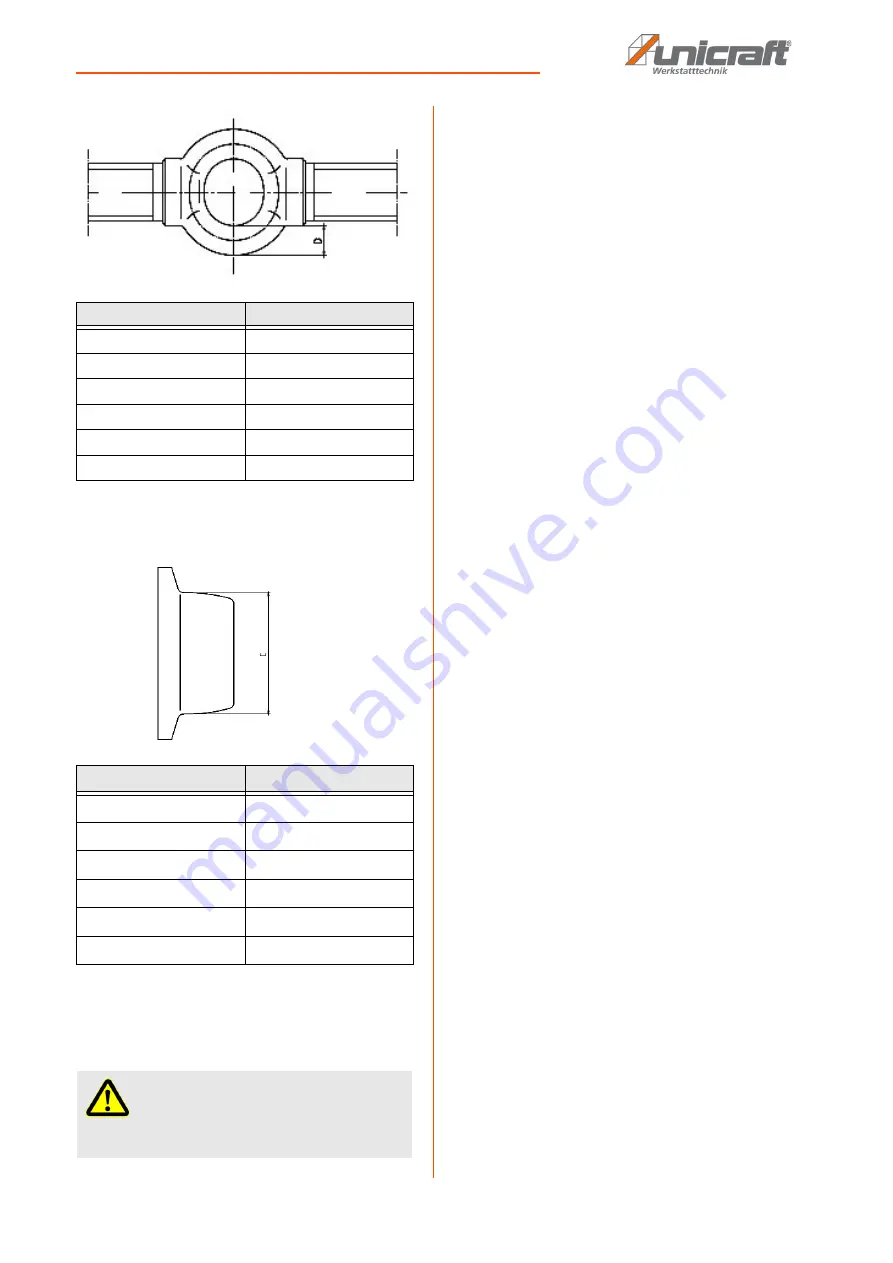
10
RFW-Series | Version 1.01
Inspecting the roller driver
Fig. 6: Thickness of the loop
Wear measurement and replacement of guide rollers
Fig. 7: Diameter of guide roller (running surface) C
The guide rollers must be replaced in the event of wear
to the limit values (see table, C).
9 Inspecting the roller driver
The use of the roller driver is possible after: UVV
"Winches, lifting and pulling equipment" BGV D8 (VBG
8), UVV "Cranes" BGV D6 (VBG 9)
Inspection by a specialist prior to initial commissioning
and after major changes when used in accordance with
BGV D8 § 23 (VBG 8 § 23)
Testing in accordance with BGV D6 § 25 (VBG 9 § 25)
by an authorised expert before initial commissioning
and after major modifications.
Periodic inspections of equipment, cranes and suppor-
ting structures by a specialist once a year. In severe
operating conditions, e.g. frequent operation at full load,
dusty or aggressive environment, high switching fre-
quency, high duty cycle, test distances must be shor-
tened.
Expert
for the testing of cranes, only the experts au-
thorised by the employers' liability insurance
associations are considered in addition to the
TÜV experts.
Specialists
are customer service fitters of the manufactu-
rer or specially trained technical personnel.
The inspection shall be documented in an inspection
book.
The test is essentially a visual and functional test. It ex-
tends to the inspection of the condition of the com-
ponents and equipment, the completeness and effec-
tiveness of the safety equipment and the completeness
of the inspection book.
10 Disposal, reusing used machines
In your own interest and to protect the environment
make sure that all machine components are exclusively
disposed of in as intended and permitted.
10.1 Decommissioning
Disused machines must be decommissioned immedi-
ately to prevent misuse at a later point and putting the
environment or persons at risk.
Step 1: Remove all environmentally hazardous process-
ing materials from the used machine.
Step 2: If necessary, disassemble the machine into as-
semblies and components that are easy to han-
dle and suitable for recycling.
Step 3: The machine components and processing mate-
rials must be disposed of using the intended
disposal methods.
Model
D [mm]
Limit value
RFW 0,5
11,0
RFW 1
15,0
RFW 2
18,0
RFW 3
23,0
RFW 5
25,0
Model
C [mm]
Grenzwert
RFW 0,5
49,5
RFW 1
63,5
RFW 2
75,0
RFW 3
94,0
RFW 5
114,0
ATTENTION!
Only use original parts from the manufacturer as
spare parts.