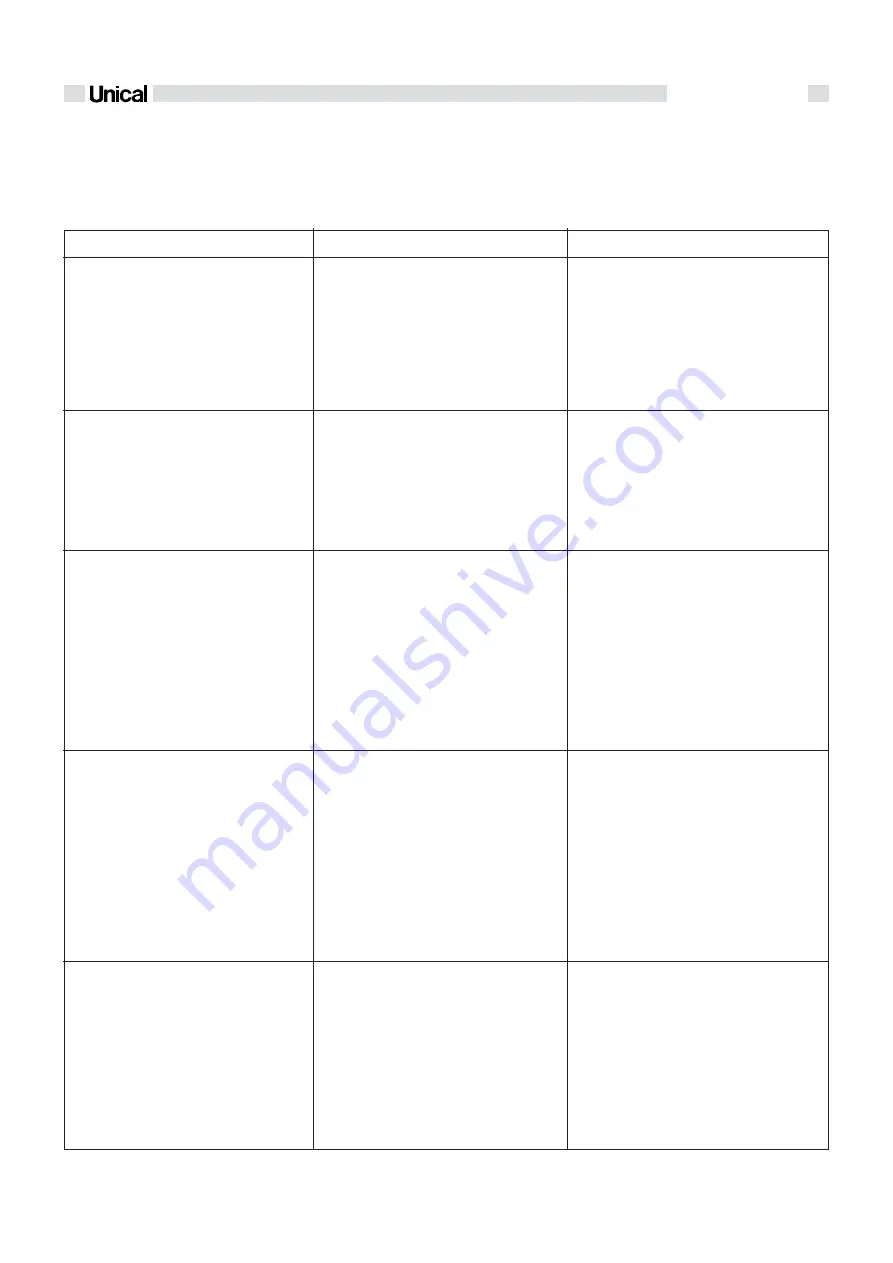
29
Service info
2.9
FINDING CHART AND CORRECTIVE ACTIONS
In the table of faults and corrective actions, we intend to give some technical informations related to the solution of faults wich can happen
during the operation or the putting into operation.
SOLUTIONS
a)
Replace the transformer
b)
Reconnect or replace the ignition leads
c)
Replace the electrode(s)
d)
Replace the electronic PCB
a)
Open the gas shut-off valve
b)
Plug the pluginto the gas train
c)
Adjust the pot.meter nr. 3 in a clock wise
direction to increase in anticlockwise di-
rection to decrease the gas quantity du-
ring ignition.
d)
Replace the gas train
a)
Reconnect or replace the cable
b)
Replace the electrode
c)
Reposition the electrode
d)
Check the burner input at minimum rate
e)
Replace the electronic PCB
a)
Check the chimney and the combustion air
intake grates
b)
Check the temperature sensor and ascer-
tain that the pump is not blocked
a)
Check the good operation of the air pres-
sure switch and replace if necessary..
b)
Reconnect or replace the silicone pipes.
c)
Check all the air/smoke ducts, clean or
replace if necessary.
d)
Replace the fan.
e)
Replace the electronic PCB
POSSIBLE CAUSES
a)
The ignition transformer is faulty
b)
The ignition leads are interrupted or discon-
nected
c)
The ignition electrodes have the insulator
broken or are in short circuit with earth
d)
The electronic board is faulty
a)
The gas shut-off valve is closed
b)
The plug to the gas train is not connected
c)
the soft light is incorrectly adjusted
d)
The gas train is faulty
a)
The detection electrode cable is faulty or not
connected
b)
The detection electrode is broken inside the
insulator (if only the insulator is broken does
not matter)
c)
The detection electrode is in short circuit with
earth
d)
The input at the minimum rate is not enough
e)
The PCB does not detected the flame
a)* The chimney draught is not correct
b)
The H.L. thermostat has cut in.
An over heating of the heat exchanger oc-
currend.
a)* The flue gas pressure switch is faulty.
b)* The silicon pipes are disconnected or bro-
ken.
c)* There is insufficient combustion air suction
or flue gas discharge.
d)* The fan does not work.
e)* The PCB is faulty
BOILERS STATUS
The boiler is in lock-out position and the red
light
G
is on.
INCONVENIENT:
The burner does not ignite because there
is no spark at the ignition electrodes
After the removal of the fault’s cause press
the reset button on the control panel to resto-
re
The boiler is in lock-out position and the red
light
G
is on.
INCONVENIENT:
The burner does not ignite even if there is
the spark at the ignition electrode
After the removal of the fault’s cause press
the reset button on the control panel to resto-
re
The boiler is in lock-out position and the red
light
G
is on.
INCONVENIENT:
The burner ignites for a few seconds and
then goes out
After the removal of the fault’s cause press
the reset button on the control panel to resto-
re
The boiler is in lock-out position and the red
light
G
is on.
INCONVENIENT:
The boilers does not try to make the igni-
tion procedure because:
- The smoke thermostat has cut the cir-
cuit (only for boilers Logamax U014 - Lo-
gamax U014 K - Logamax U014 VMC - Lo-
gamax U014 K VMC)
- The H.L. thermostat has cut the circuit
After the removal of the fault’s cause press
the reset button
L
on the control panel to
restore
The boiler is in permanent lock-out.
The red light
G
in on and the green light
F
is
blinking
INCONVENIENTS:
The smoke pressure
switch did not give the permission for the
burner ignition
Reset from this status can be done by
swtching OFF and ON the main switch
A
* These conditions are detected as
ignition failure
(vedi 2.10.3)
Summary of Contents for RTN 24
Page 35: ...35...