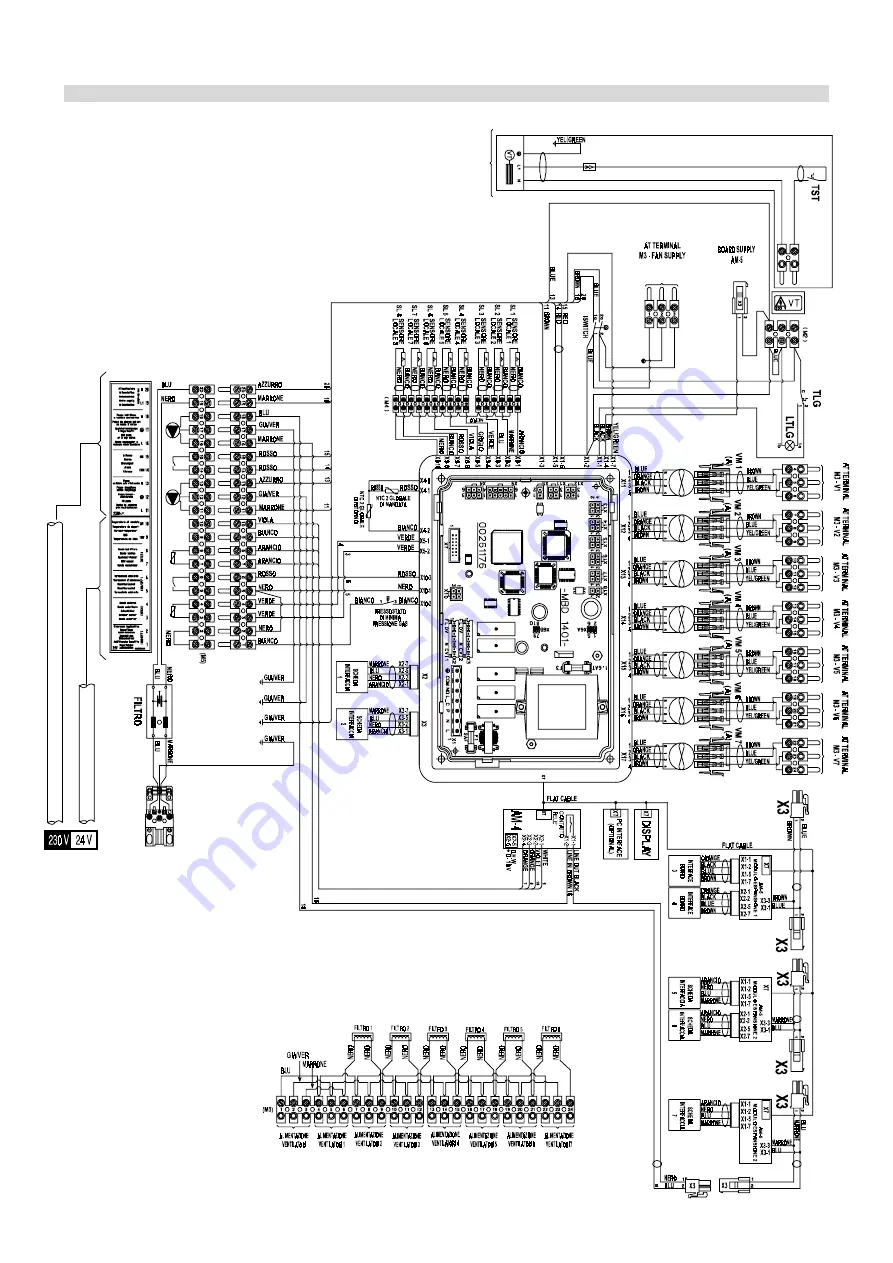
25
Fig. 14
2.6.1 - WIRING DIAGRAM
SE
CU
RIT
Y
TH
ER
M
O
ST
AT
TRAN
SF
O
R
M
AT
O
R
RE
D
BL
UE
BL
UE
TA
NG
EN
TIA
L FA
N
K
IT
BRO
W
N
AL
IM
EN
TA
ZIONE
23
0 V
- 50
H
z
RED
BROWN
BRO
W
N
BL
UE
BRO
W
N
BR
O
W
N
BL
UE
YE
L/G
R
EEN
RE
D
BL
AC
K
BR
O
W
N
00331506
C
O
N
D
O
T
T
O
C
A
VI
2
30
V
C
O
ND
O
T
T
O
CA
V
I 2
4
V
HIG
H
LIM
IT
TH
E
RM
O
ST
AT
GE
N
ER
A
L
LA
M
P H
IG
H
LI
M
IT G
EN
ER
A
L
T
H
ER
M
O
ST
AT
E