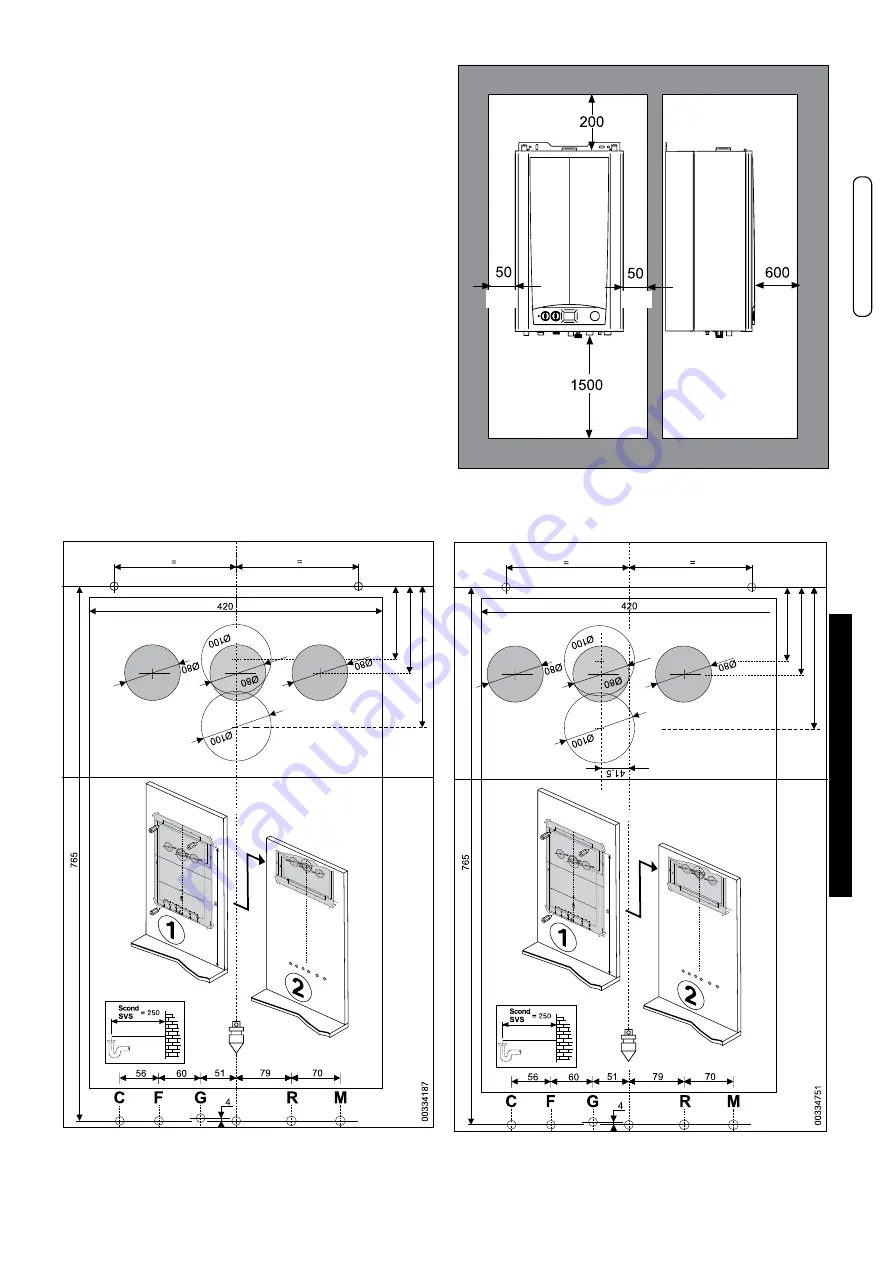
19
ENGLISH
Installation Instructions
(200)
(200)
3.5 - POSITIONING THE BOILER
Clearance
105
125
200
105
125
200
KONm 18 - 24
KONm 28 - 35
When choosing the place of the installation of the
appliance, follow the safety instructions below:
- Place the appliance in rooms protected from frost.
- Avoid installation in rooms with a corrosive or very
dusty atmosphere.
- The appliance must only be installed on a vertical
and solid wall which can support its weight.
- The wall must not be made of flammable material.
Since the temperature of the wall on which the boil-
er is installed and the temperature of the coaxial
exhaust pipe do not exceed, in normal operating
conditions, a room temperature beyond 60 K, it is
not necessary to observe the minimum distances
from flammable walls.
For boilers with double intake and exhaust pipes, in
the event of crossing flammable walls, insert insula
-
tion between the wall and the flue gas exhaust pipe.