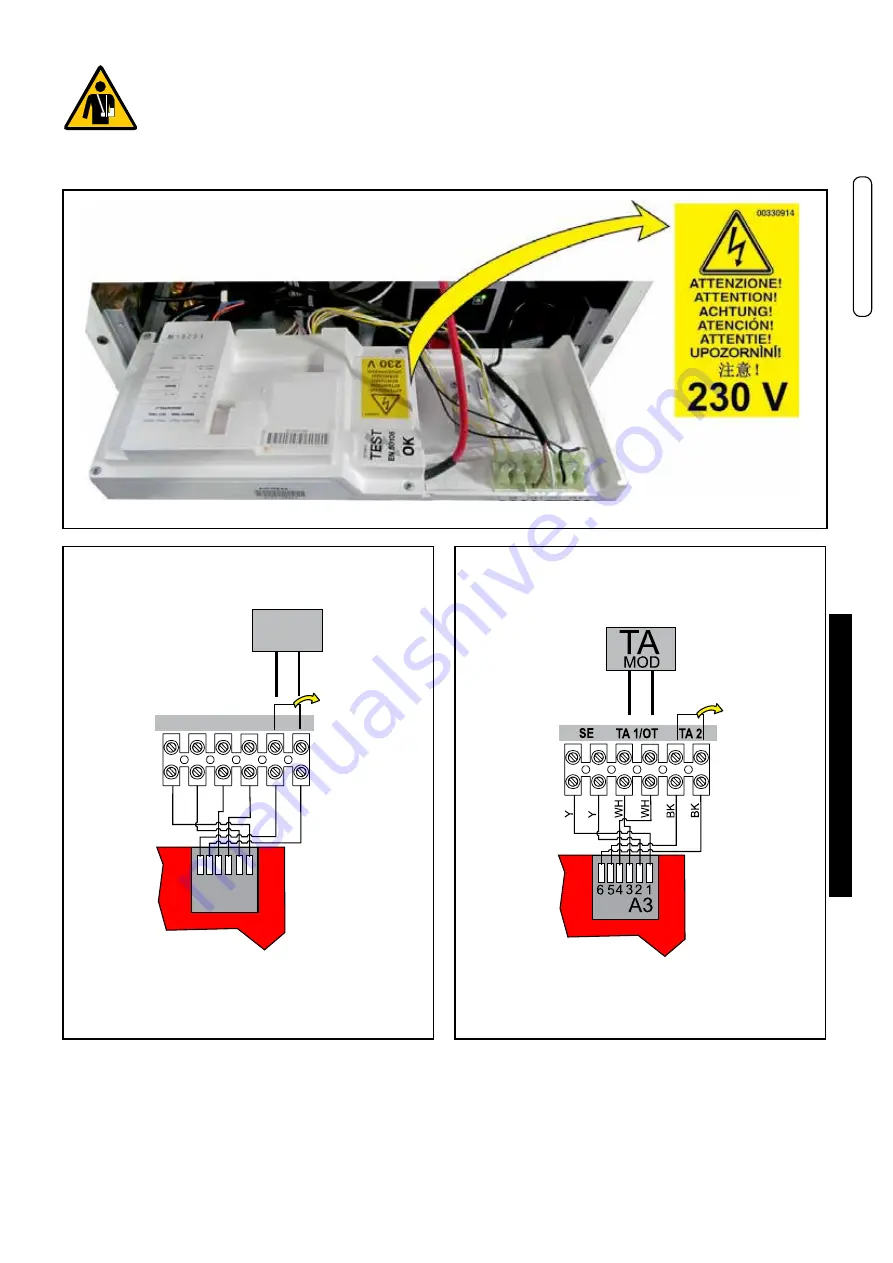
23
ENGLISH
Installation Instructions
ON/OFF room
thermostat connection (*)
- Remove the jumper and connect the room ther
-
mostat wires between terminals TA 2.
- Connect the modulating thermostat wire between
terminals
TA1/OT
after having removed the jumper.
ON/OFF room thermostat connection
RT/OT (*)
A3
4 3 2 1
6 5
SE
TA 1/OT
TA 2
WH
WH
Y
Y
BK
BK
TA
ON-OFF
Danger!
Only a qualified technician may per
-
form the electrical installation.
Before performing connections or
3.9 - ELECTRICAL CONNECTIONS
any type of operation on electrical parts, always
disconnect electrical power and make sure that
it cannot be reconnected accidentally.