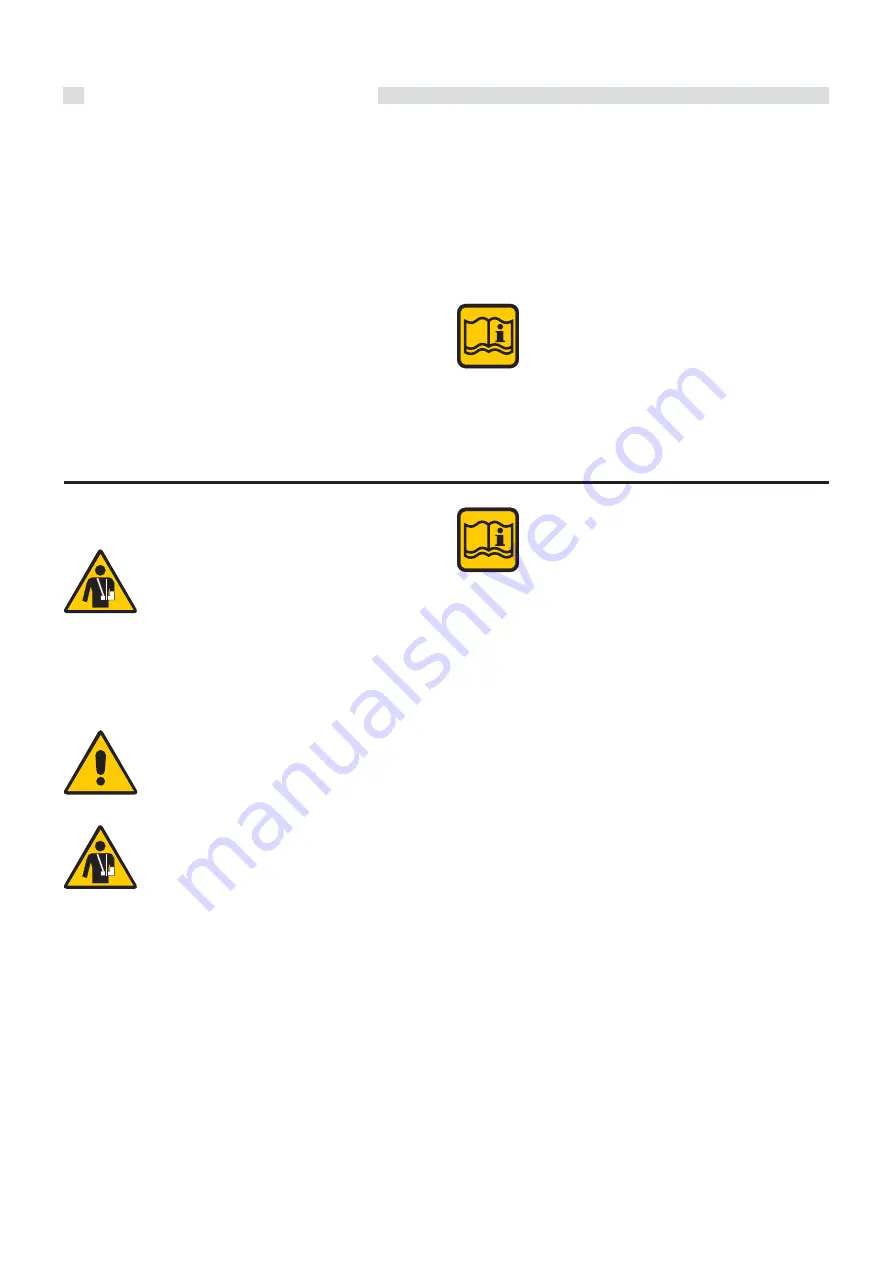
16
Instruction for the installer
3.6 - GAS CONNECTION
DANGER!
The gas connection must be carried out only
by a qualified engineer who will have to
respect and comply to the regulations in
force and to the requirements indicated by
the local gas supplier. An incorrect
installation could cause injury to persons,
animals or damage to property. The
manufacturer shall not be held liable for any
injury and/or damage.
Before installing the boiler it is
recommended to thoroughly clean all the
fuel feed pipework in order to remove any
eventual residual grime which could
compromise the boilers correct functioning.
If you smell gas:
a. Do not turn on or off electrical switches,
use the telephone or any other object
which can provoke sparks;
b. Open all doors and windows in order to
allow fresh air to enter and purify the
room;
c. Close all gas cocks;
d. Contact a service engineer, qualified
installer or the gas supply company.
3.5 - BOILER INSTALLATION
Before connecting the boiler to the heating system the following
requirements must be carried out by competent and qualified
engineers:
a) The system is flushed out with a suitable product in order to
eliminate any metallic tooling or welding residues and oil
and grime which could reach the boiler and affect the proper
running of the boiler;
b) Check that the boiler has been preset for operating with the
gas type available.
This is verifiable via the indication on the packaging and on
the data badge;
c) Check that the chimney/flue pipe has an adequate draught,
does not have any constrictions, and that no other
appliance’s flue outlets have been fitted, unless the chimney
is serving more than one heating appliance, according to
the specific standards and regulations in force. The
connection between the boiler and chimney/flue outlet can
be made only after this verification has been carried out.
For fitting the boiler:
- Place the steel mounting template on to the wall.
- Determine the position of the holes for fixing the support
bracket.
- Drill the holes and fix the support bracket using the fixing
screws as indicated on page 14.
- Engage the boiler on to the support bracket.
- Mark the positions of the gas, cold water supply, hot water
outlet, CH flow and return, pressure relief valve and/or
condensate drain.
Note: The appliances are equipped with
expansion vessels. Before installing the
appliance check that the vessel’s capacity is
sufficient; if this is not the case, provision
must be made to fit an additional expansion
vessel.
As a safety measure against gas leaks, Unical
recommends installing a surveillance and
protective system composed of a gas leakage
detector combined with an on-off selenoid
valve fitted on the gas supply line.
The gas supply pipe must have a section which is identical or
greater then the one used on the boiler and must assure a
correct gas pressure.
It is however important to comply with the “General installation
standards” indicated in the standards UNI 7129, UNI 7131 and
UNI 1137-1.
Before commissioning an internal gas distribution system and
therefore before connecting it to the gas meter, the complete
installation must be tested for gas soundness.
If any part of the system is concealed from view the gas
soundness test must be carried out before covering the pipes.
Before connecting the pipework the system must be tested
with air or inert gas at a pressure of at least 100mbar.
Before commissioning the boiler ensure that the following
operations are carried out:
- Open the gas meter cock and vent the air contained in the
piping and subsequently proceed to vent device by device.
- Check, with the gas cock turned off, that there are no gas
leaks. During the 2
nd
quarter of the hour from the start of the
test, no pressure reduction should be detected by the
pressure gauge. Any gas leaks must be found by using only
water soap solutions, or an equivalent product, and
eliminated.
Never look for gas leaks using a naked flame
.
Summary of Contents for ALKON R 24
Page 47: ......