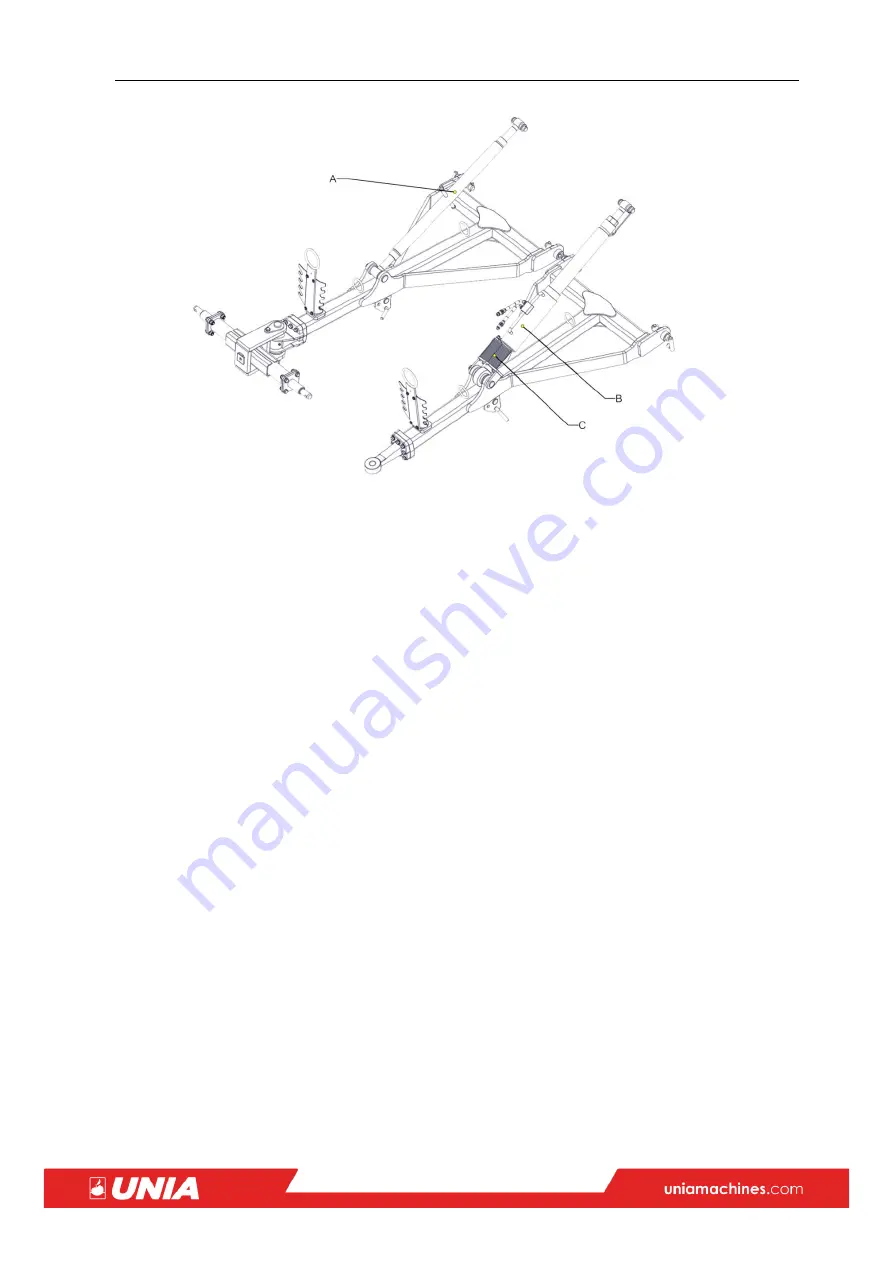
OPERATING AND MAINTENANCE MANUAL ARES P / ARES ROLLER UP
- 20 -
Once the machine working depth is set on the roller in the ARES P unit, adjust also the correct depth
on the drawbar. Parallel position of the frame during work is the determinant.
•
In order to adjust with the turnbuckle, rotate the turnbuckle
[A]
to the left or right, through
which the machine front part is lifted up or lowered down
•
Hydraulic adjustment consists of applying pressure from the tractor cab to the cylinder
[B]
causing its extension. Then, put on the desired number of the stops
[C]
and reapply pressure
to the cylinder
[B]
. The cylinder comes back to the stops
[C]
, through which, the machine is
lifted up or lowered down.
Fig.:10
Depth adjustment on the drawbar
Summary of Contents for ARES P
Page 1: ......
Page 2: ......
Page 4: ......
Page 31: ...OPERATING AND MAINTENANCE MANUAL ARES P ARES ROLLER UP 29 COMMENTS AND NOTE ...
Page 32: ...OPERATING AND MAINTENANCE MANUAL ARES P ARES ROLLER UP 30 COMMENTS AND NOTE ...