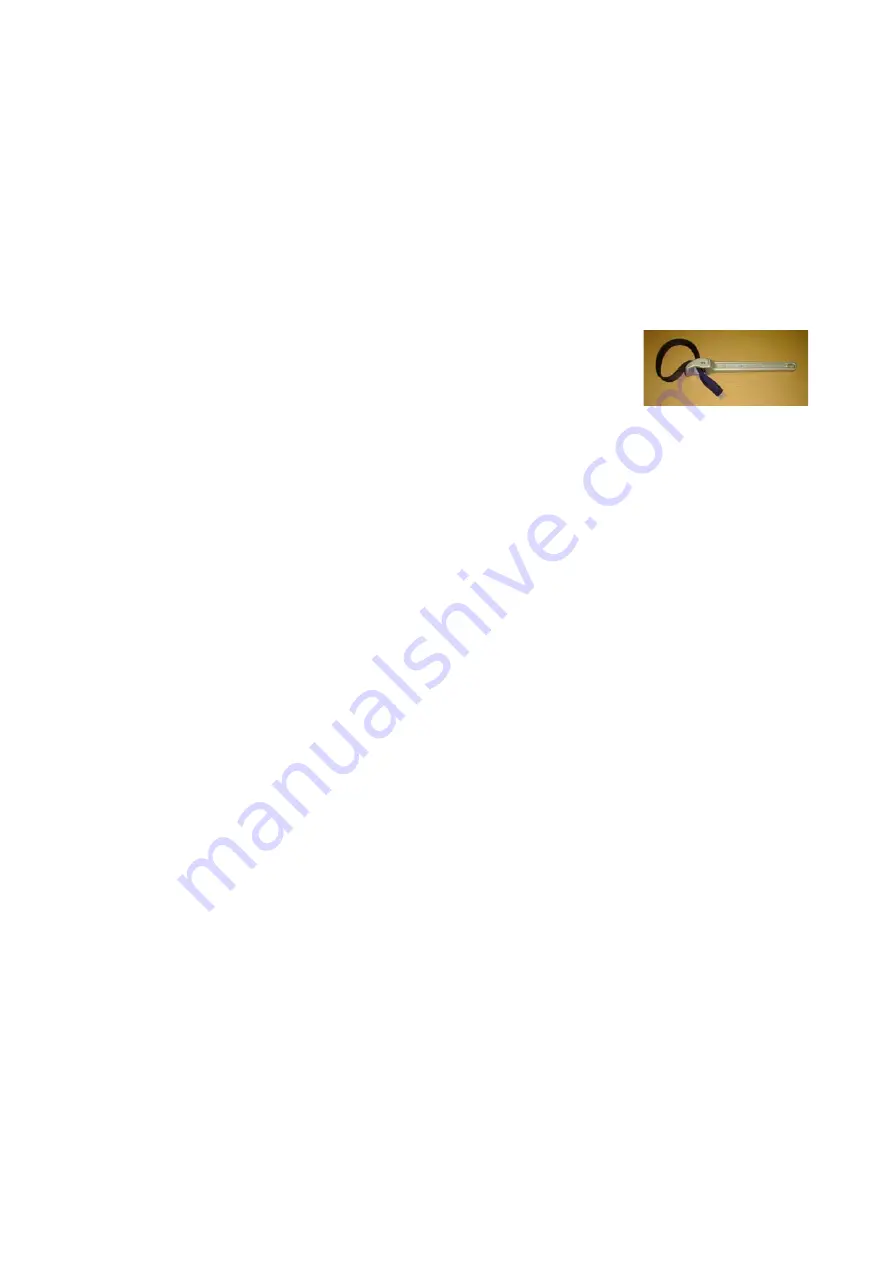
9
Belt wrench
BW-2
(
by Supertool Inc.
)
10-7.
Turn on the power source of the UFO-003, and operate for
a few minutes. Drain all the oil inside.
10-8.
Stop operating after making sure that draining stops
from the drain port.
10-9.
Loosen the upper joint of the filter case and remove
the hose.
10-10.
Remove the filter case by turning it anti-clockwise.
(
If it is stiff, put rubber bands three places
around the case and turn it. It is also easy to turn it
by usin
g a belt wrench. Should not use any other
tools for removing; it might cause damages).
10-11.Remove the element from the housing head.
10-12.After cleaning the inside and outside of the housing
area, place a new element.
10-13.Install the filter case and the hose.
10-14.Install a plug to the drain port.(Be sure to fix with the seal tape around screw area).
10-15.Supply some oil by following the directions on Section 6-2
~
6-7.
Caution
)
If the oil is badly degraded, and frequent replacement
of the element is needed, a drain valve (optional) is
very useful.
11.
Oil Replacement of Vacuum Pump
11-1. For oil draining of the vacuum pump
、
follow the directions on Section
10-2 to 10-8. The Inlet side 3-way valve should face to the
inlet side.
(
The Outlet side 3-way valve is at closed position
)
11-2. For supplying oil into the vacuum pump, follow the directions on
Section 6-2 to 6-7