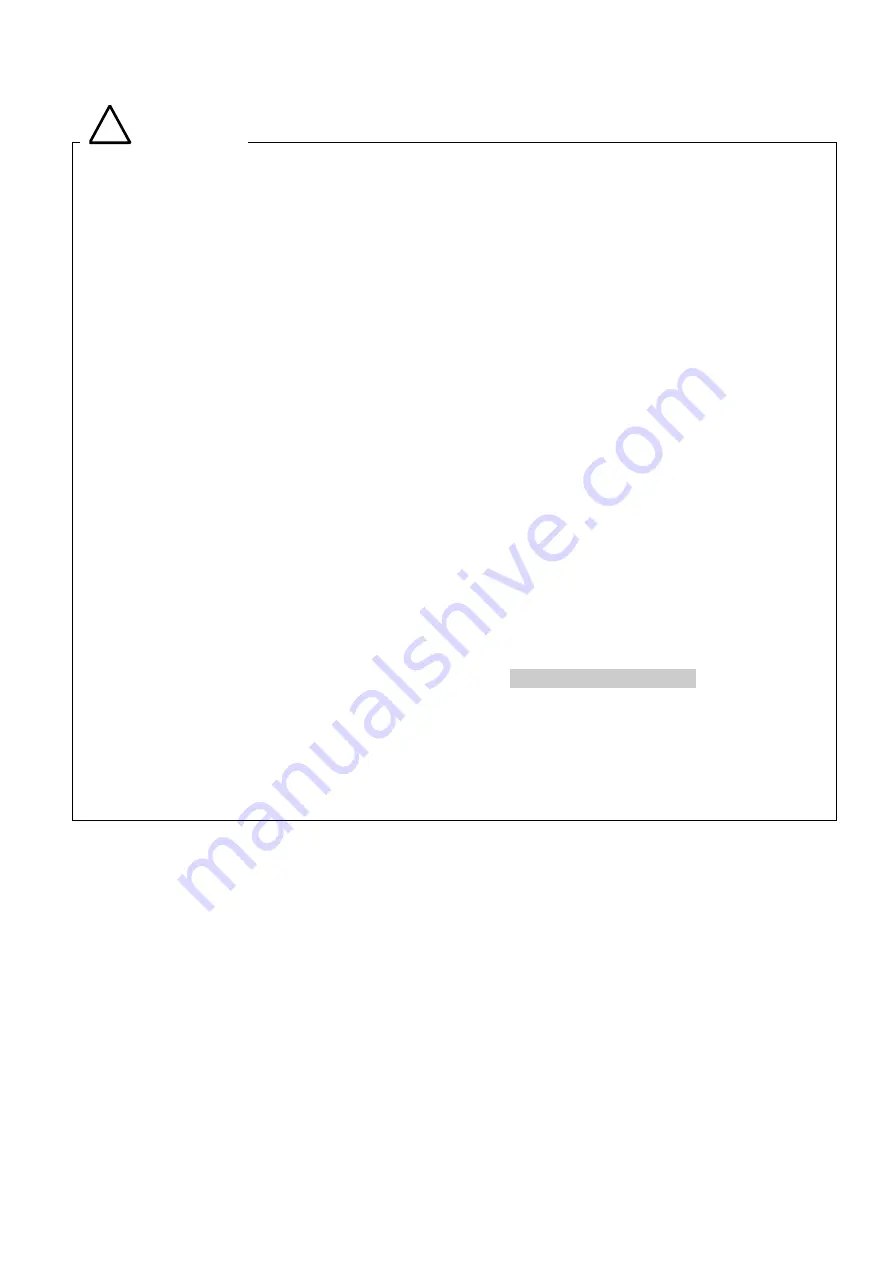
6
Installation
(1) The fine clearances used in this pump require that the following conditions be satisfied
during storage, installation, and operation.
1. Ambient temperature, relative humidity: 7~40°C, 85% RH or less during operation.
Height above sea level during storage and installation 1000m or less.
2. Other conditions for storage and operation.
a) Horizontal floor of sufficient strength.
Do not install the pump either vertically or facing downwards.
b) No condensation.
c) Free of dust.
Ensure that water or dust does not enter the pump or motor during assembly.
d) Free of soot and oil.
e) Free of splashing or flooding.
f) Environment free of explosive gas.
g) Not subject to direct sunlight.
h) No danger of fire.
i) When storing the pump, or when operating it within other equipment, ensure that
the temperature in the vicinity of the pump does not exceed 40°C.
j) When installing the pump, avoid mounting a vacuum pump directly on the base.
Employ anti-vibration rubber between the base and the vacuum pump.
k) Store the pump inside in well ventilated conditions. When the pump is operated
outside, ensure that it is installed in accordance with a) - j) above.
(2) There is a risk of hurting lower back. Lift the pump with both hands definitely to move and
conduct work.
Abrasive particles of diaphragm may drain from the exhaust vent and pollute the room.
Exhaust it to out of the chamber by connecting pipes if necessary.
(3) Install the main disconnection (suitable plug or switch/circuit breaker) device for safety.
!
Caution