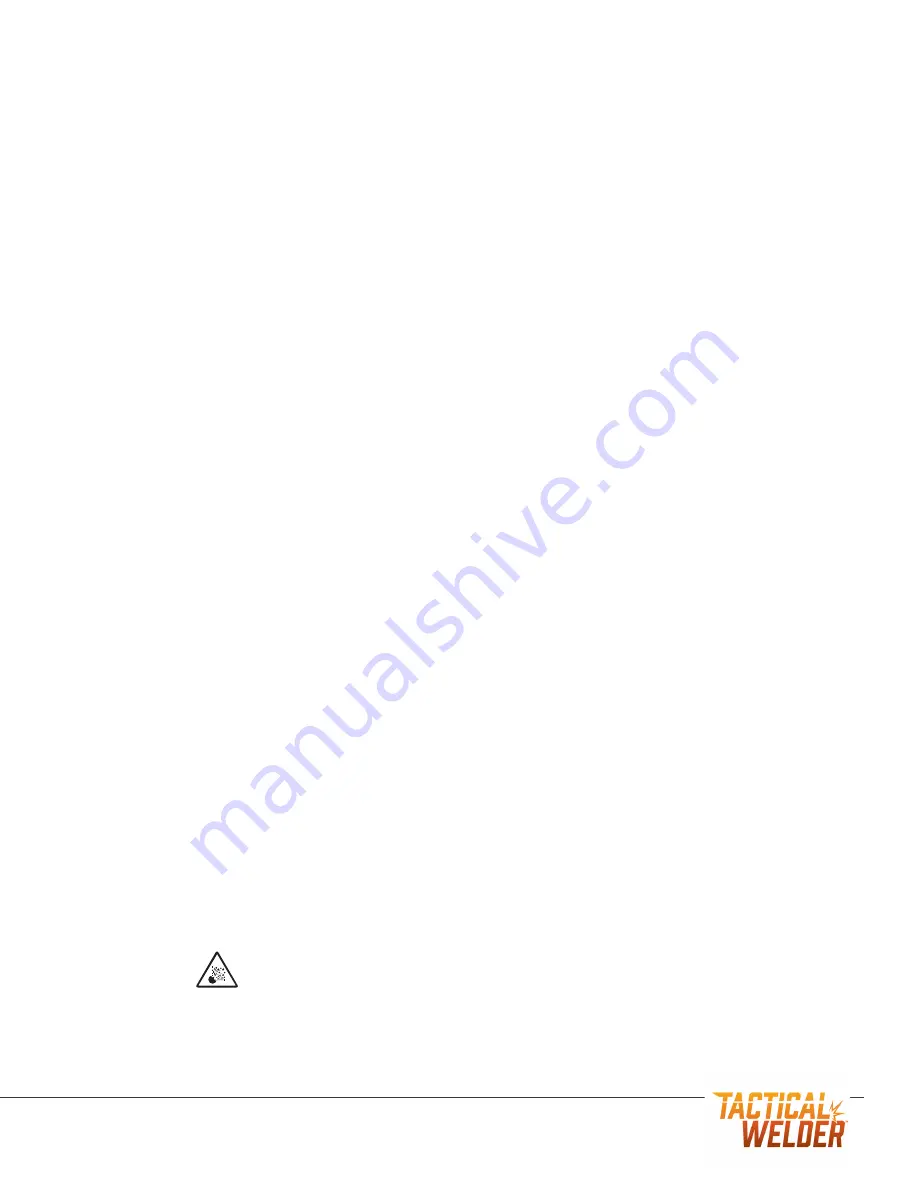
5
arc rays from entering around the helmet. It is important to make
sure others are protected from arc rays and sparks. Approved
shielding curtains and/ or appropriate goggles should be used by
all persons working in close proximity of the welding area to protect
them from arc rays and sparks. Skin should and must be protected
from arc rays, heat and molten metal. The operator must always
wear protective gloves and clothing which will not allow skin to
become exposed. All clothing pockets should be closed and cuffs
sewn shut. Leather aprons, sleeves, leggings, etc. should and must
be worn for out-of-position welding. High top work shoes provide
adequate protection against foot burns; for added protection, use
leather spats. Flammable hair products should not be used when
welding.
Keep all persons, especially children, out of the work area while any
devices are in operation or welding is in progress. If however, there
are people in the vicinity,
• Make them aware of the dangers (risk of dazzling by the arc,
injury from flying sparks, inhaling welding fumes, noise, possible
danger from mains or welding current, etc.).
• Provide suitable protective equipment or
• Erect suitable safety screens/curtains.
• Danger from Toxic Welding Fumes
• The fumes produced during welding contain harmful gases and
vapors.
• Welding fumes contain substances that may, under certain
circumstance cause birth defects or cancer.
• Keep your face away from welding fumes and gases.
• Fumes and hazardous gases
· Must not be breathed in
· Must be extracted from work area using appropriate methods
• Ensure an adequate supply of fresh air with a ventilation rate of
at least 20 cubic meters/hour.
• Otherwise, a protective mask with an air supply must be worn.
• Close the shielding gas cylinder valve or main gas supply if no
welding is taking place.
• If there is any doubt about whether the extraction capacity
is sufficient, the measured toxic emission values should be
compared with the permissible limit values.
Specific Areas of Risk
BE AWARE, WELDING SPARKS CAN AND DO CAUSE FIRES AND
EXPLOSIONS
Causes of fire and explosions are: combustibles reached by the
arc, flame, flying sparks, hot slag, or heated materials. Remove
combustible materials and items from the work area and/or
provide a fire watch. Avoid oily or greasy clothing as a spark can
ignite them. It is necessary and required that the operator have
a fire extinguisher nearby and have knowledge and training in its
use. Be aware and alert to the danger of conduction or radiation.
For example, if welding is to be done on a metal wall or partition,
ceiling or roof, precautions must be taken to prevent ignition of
combustibles on the other side. Do not weld near combustible or
containers that have combustibles. All hollow spaces, cavities and
containers should and must be vented prior to welding to permit the
escape or air or gases. Purging with inert gas is recommended. Use
only inert gases or inert gas mixtures as required by the process. Use
of combustible compressed gases can cause explosions resulting
in personal injury or death. Arcing against any compressed gases
can cause explosions resulting in personal injury or death.
A high risk of injury exists when the welding wire emerges from the
welding gun (piercing of the hand, injuries to the face and eyes,
etc.). Always keep the gun well away from the body, and wear
suitable protective goggles.
Never touch the work piece during or after welding – risk of burns.
Slag can sometimes fly off work pieces as they cool down. The
specified protective equipment must therefore also be worn when
reworking work pieces, and steps must be taken to ensure that
other people are also adequately protected. Welding guns, torches
and other parts with high operating temperature must be allowed to
cool down before handling.
Safety and Operation References
1. Code of Federal Regulations, (OSHA) Section 29 Part 1910.95, 251-254
and 1000. U.S. Government Printing Office, Washington, D.C. 20402
2. ANSI Z49.1 “Safety in Welding and Cutting” American National Standard
Institute, 1430 Broadway, New York, NY 10018
3. ANSI Z87.1 “Practice of Occupational and Education Eye and Face
Protection” American National Standard Institute, 1430 Broadway,
New York, NY 10018
4. ANSI Z88.2 “Standard Practice for Respiratory Protection” American
National Standard Institute, 1430 Broadway, New York, NY 10018
5. AWS F4.1 “ Recommended Safe Practices for Welding and Cutting
Containers” The American Welding Society 550 NW Lejeune Road PO
Box 351040, Miami, FL 33135
6. NFPA-51B “ Fire Prevention in Cutting and Welding Processes” National
Fire Protection Association, Battery Park, Quincy, MA 02269
7. NFPA-7 “National Electrical Code” National Fire Protection Association,
Battery Park, Quincy, MA 02269
8. CSA Standard W117.2 “Safety in Welding, Cutting and Allied Processes”
Canadian Standards Association, 178 Rexdale, Ontario, Canada M9W
1R3
Summary of Contents for Tactical Welder 4800
Page 9: ...9...