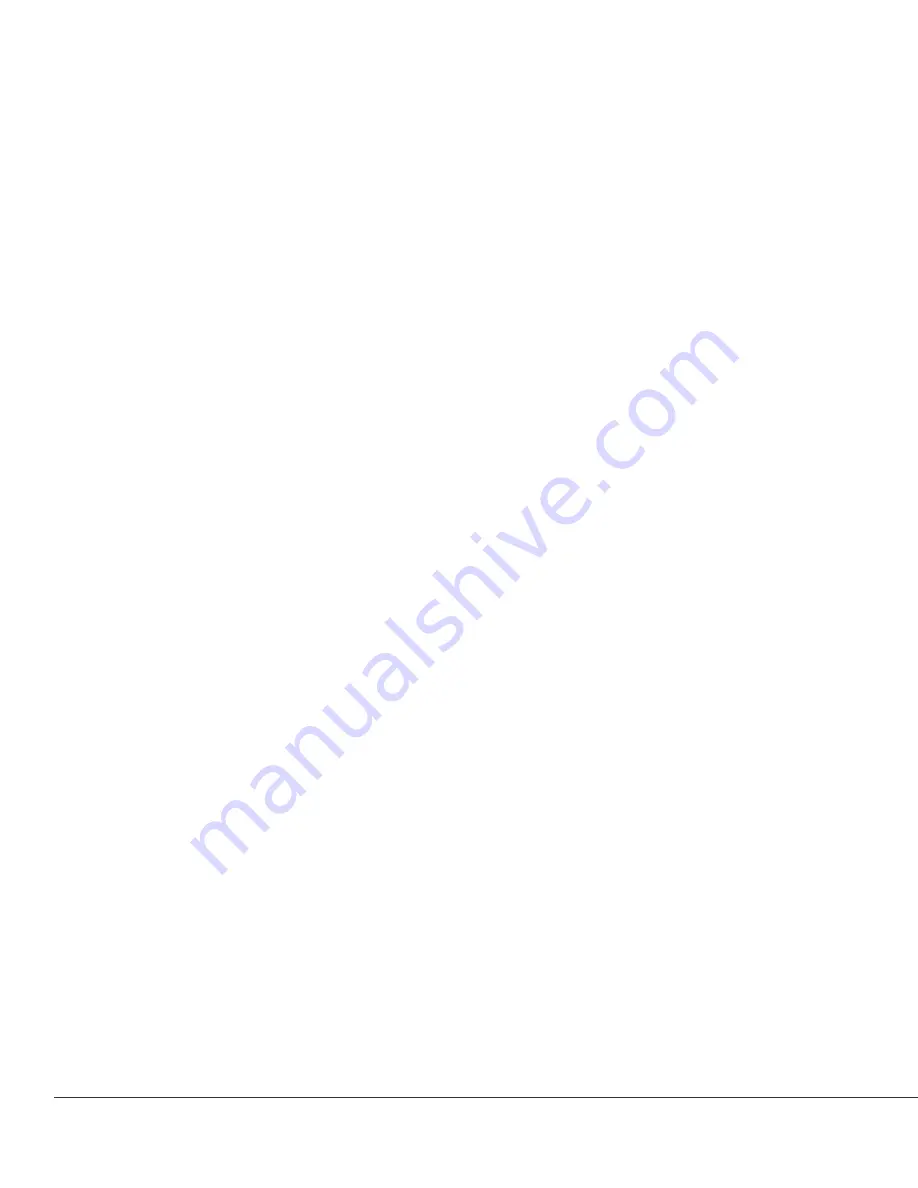
1-904-292-1611 · tacticalwelder.com
14
Thin Metal Welding
Aluminum Welding
1. Use the Smallest Diameter of Feed Wire Available of the Type
Desired.
The smaller the diameter of wire the less current it can
conduct, therefore use the smallest diameter feed wire you can
in any given application to cool down the bead to reduce melt-
through. Solid steel, stainless and aluminum wires come in .023”
diameter and will require the use of gas. Flux-Core wire comes in
.030”, typically as a minimum.
2. Use Increased Wire “Stick-Out” Length to Cool the Bead.
The
greater the distance from the end of the contact tip to the bead,
the greater the resistance faced by the arc current. Increasing
wire “stick-out” works best flux-cored wire since you will not be
concerned about keeping any shielding gas focused on the bead
area.
3. “Stitch Welding” Mode.
The use of this mode of welding should
allow you to successfully weld thin sheet metal using the Tactical
Welder without melt-through problems. By producing a series of
small, cooler beads, rather than a continuous bead, the stitch
mode process prevents the bead area from getting hot enough
to melt the surrounding metal. To use this process, turn the
welding gun’s wire feed speed control know to the “off” position
and then slowly advance it until the electrode wire just starts to
feed slowly out of the contact tip. Release the trigger and cut off
the excess wire which has been fed out. Aim the welding gun at
the thin metal you wish to weld and pull the trigger while allowing
for the maximum acceptable amount of wire “stick-out”. Keep
the trigger pulled during the entire stitch mode welding process.
When the feed wire makes contact and creates a small bead, the
feed wire will momentarily melt back to the point that the arc is
broken. The feed wire will feed out to the point that another bead
is formed where the previous bead ended. Repeat this process of
connecting small sequential beads until the job is complete. By
using the maximum wire “stick-out” you can reduce the likelihood
of wire “burn-back” clogging the contact tip.
4. Increase External Resistance.
This will lower the output and can
be done in several different ways such as longer cable, smaller
cable or by attaching a piece of chain to the work piece and
adjusting the ground clamp up or down the chain, be aware that
increased resistance causes greater heat.
General Points
When welding aluminum, be sure to use a contact tip which is
.005” larger than the wire diameter itself, and extend out from the
nozzle approximately 3/8”, this helps reduce burn back (i.e. melting
the wire in the tip). As aluminum conducts heat so rapidly, some
operators find it preferable to increase wire speed and move more
quickly across the metal being welded, especially on thin aluminum
of 1/8” and less. Please consult application chart.
Preheating aluminum over 1/4” thick to approximately 250 degrees
F., is a widely recognized practice and helps on the start of the bead
while increasing penetration. Using a heat sink steel plate on the
back side of aluminum can help prevent burn through. Please note:
When welding, thin aluminum wire will help to reduce the voltage
and amperage. When welding on 1/8” thick aluminum or less, the
travel rate must be faster than on steel and movement must be
similar to drawing a line on a piece of paper. When the wire speed is
adjusted correctly there should be no spatter and the weld process
should be very quiet, similar to the sound of a gas leak. HINT: The
proper travel is to push with aluminum usually right to left if you’re
right handed, left to right if you’re left handed.
Ready to Weld with Aluminum
You are now ready to establish an arc and weld aluminum.
Depending on the thickness, and mass of aluminum to be welded,
a slight preheat in the area where you are going to start will help
provide a uniform weld bead. Your welding position should be with a
slight tilt of the welding gun into the direction of travel; this is called
the forehand technique. When you are ready to establish the arc,
hold the gun nozzle about 1/4” away from the grounded work piece.
Slowly depress the gun trigger to start the flow of argon shield
gas. Set the argon shield gas to 25-30 psi. Now pull the gun trigger
and establish the arc. The weld wire should burn off slightly above
the grounded work piece. If excess spatter or crackling sound are
detected, slow the wire speed just slightly until a quiet smooth-
running arc is achieved. If you are welding lighter gauge aluminum,
increasing travel speeds will help avoid burning through.
Summary of Contents for Tactical Welder 4800
Page 9: ...9...