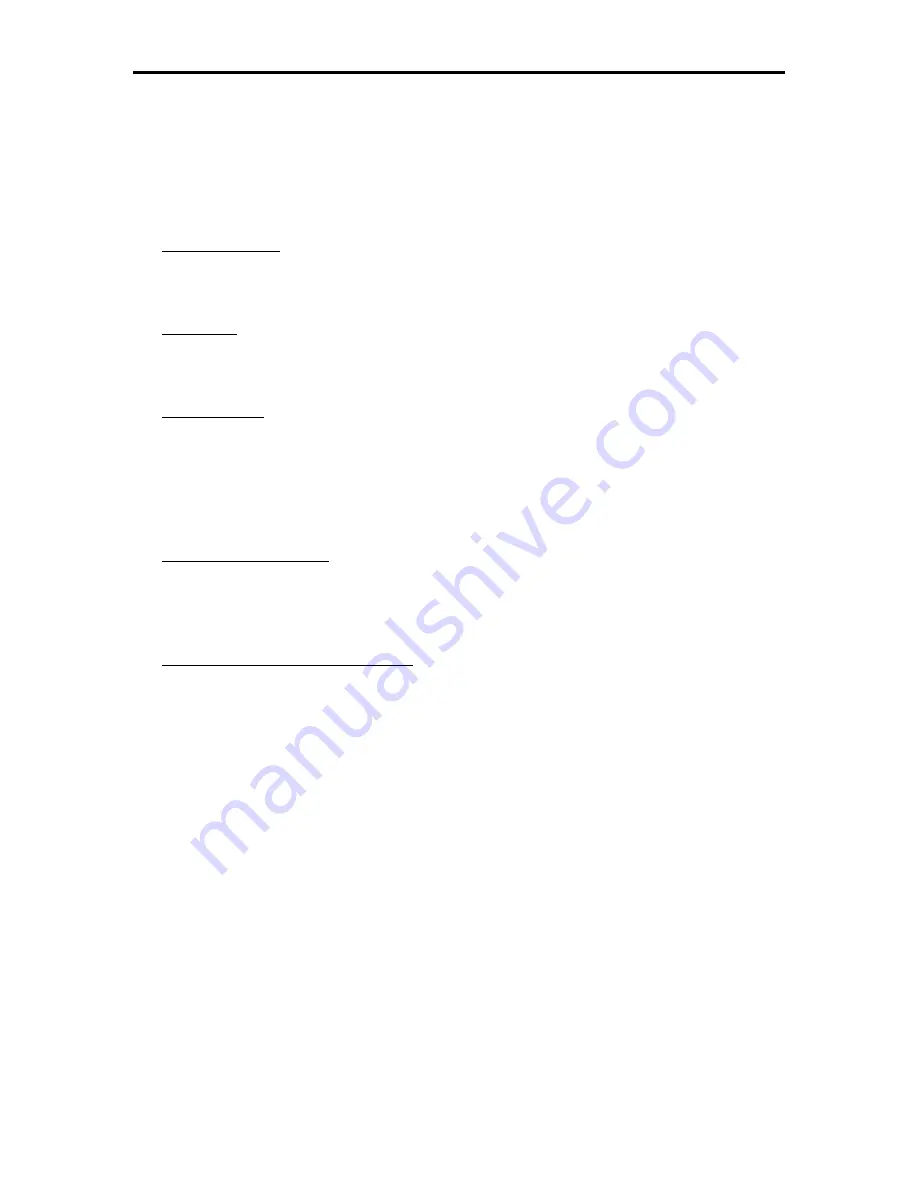
UltraSonic LLC. Model Ultra 3200FA
11
Temperatures above can decrease the ultrasonic action. Consideration needs to be
given to the cleaning agent used when determining the proper temperature.
NOTE:
Always check the MSDS for the cleaning agent and note its boiling point or flash
point. Operation near or above the boiling point/flash point is hazardous and can
cause noxious fumes.
Cleaning Agent - Cleaning agents can enhance or decrease the performance of the
ultrasonic action and speed of cleaning. Always use UltraSonic LLC recommended
cleaning agents at their proper concentrations.
Degassing - Liquids containing air and dissolved gases can interfere with the
formation of cavitation bubbles necessary for ultrasonic cleaning. Follow the
procedure in the installation section to ensure liquid is ready for cleaning.
Part Exposure - In order for a surface to be cleaned, it must be exposed to the liquid.
This requires proper placement of the parts in the parts basket. Do not overload
baskets with small parts that prevent the middle layers from getting proper exposure
to the liquid. Also, improper placement of parts with blind holes or cavities can result
in air pockets, where no cleaning action occurs. In general, clean large numbers of
parts a few at a time using shorter cleaning cycles.
Contaminated Solution - As contaminants build up in the solution the ultrasonic
performance drops. The cavitation bubbles waste their energy imploding on the
contaminants and not on the part surface. It is important that you change the solution
on a regular basis.
Parts Materials and Contamination - Certain materials absorb ultrasonic energy,
generally these are soft materials like rubber, fabric, gaskets and heavy grease.
Ultrasonics is extremely effective with a hard surface to impact against. Therefore,
parts contaminated with heavy amounts of grease or soft materials should be pre-
cleaned prior to exposure to the ultrasonic tank.