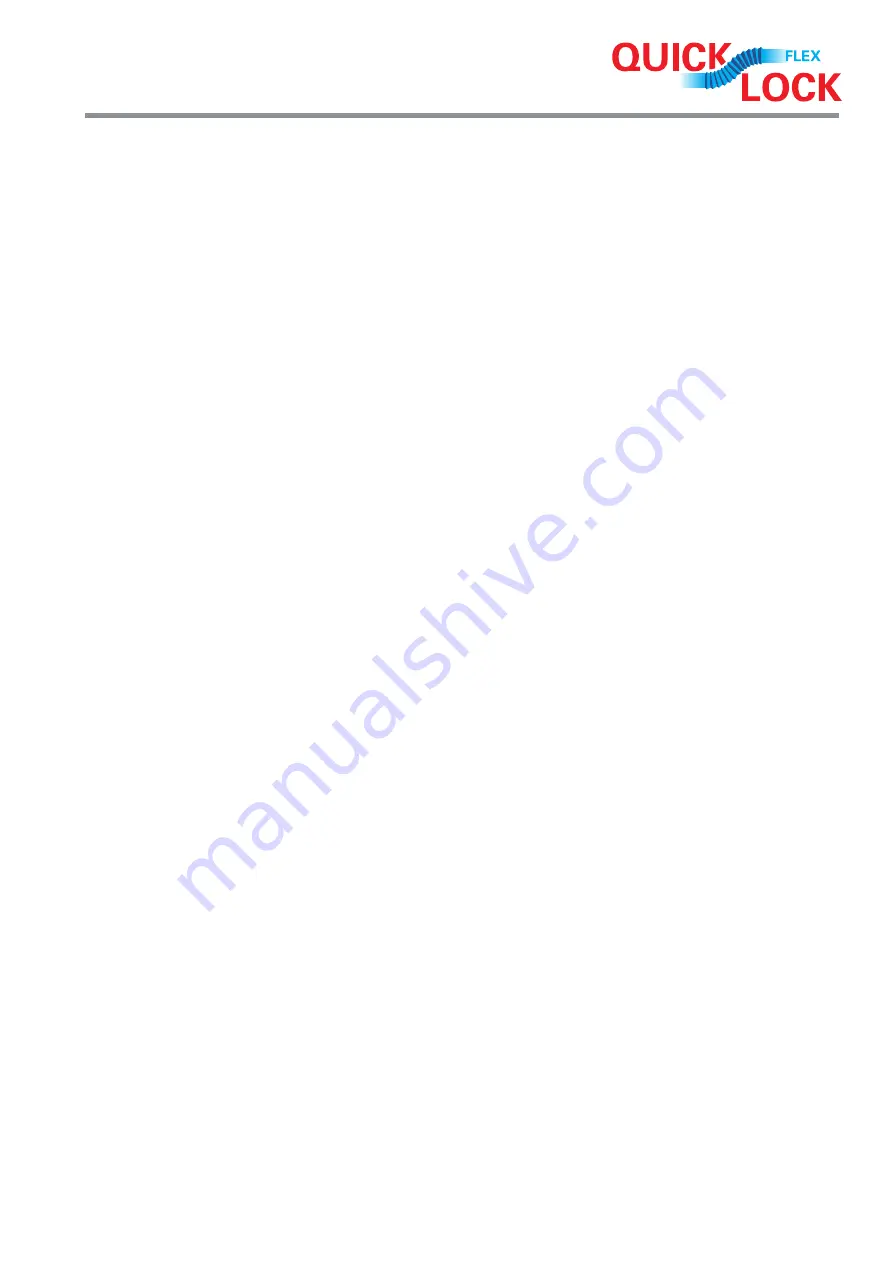
10
3.3.2. Installation
• Position the QL Flex sleeve on the front of the packer.
• Grip the sleeve by inflating the packer balloon to a holding pressure of
approximately
0,5 bar.
• This prevents the sleeve from slipping off.
• The holding pressure of 0.5 bar may vary slightly depending on the
compressed air unit, the pipe nominal diameter and the packer. We
recommend that you identify the correct pressure for your system yourself.
• The holding pressure is correct when the sleeve is firmly held on the packer
does not start to expand.
• Now transport the packer with the QL Flex sleeve to the damaged area.
• Position the QL Flex sleeve so that its centre is located in the centre of the
damaged area.
Positioning pressure
• Press the packer with a positioning pressure of approximately
1.0-1.5 bar so that the sleeve is positioned over the offset in the pipe wall.
• Now allow the sleeve some time to expand. Apply pressure to the sleeve
slowly and intermittently and wait until it has reached full expansion.
Reducing the pressure
• Deflate the packer balloon so that you can reposition the packer.
Aligning with the locks
• Align the packer with the middle of the rear lock.
Application pressure
• Application pressure application pressure of 3.0 - 5.0 bar [Appendix 2] to
make sure that the rear QL Flex is completely compressed against the
pipe wall in the undamaged area of the pipe.
Reducing the pressure
• Deflate the packer balloon so that you can reposition it.
Aligning with the locks
• Align the packer with the middle of the front lock.
Application pressure
• Apply an application pressure of 3.0 - 5.0 bar [Appendix 2] again to make
sure that the front QL Flex is completely compressed against the pipe wall in
the undamaged area of the pipe.