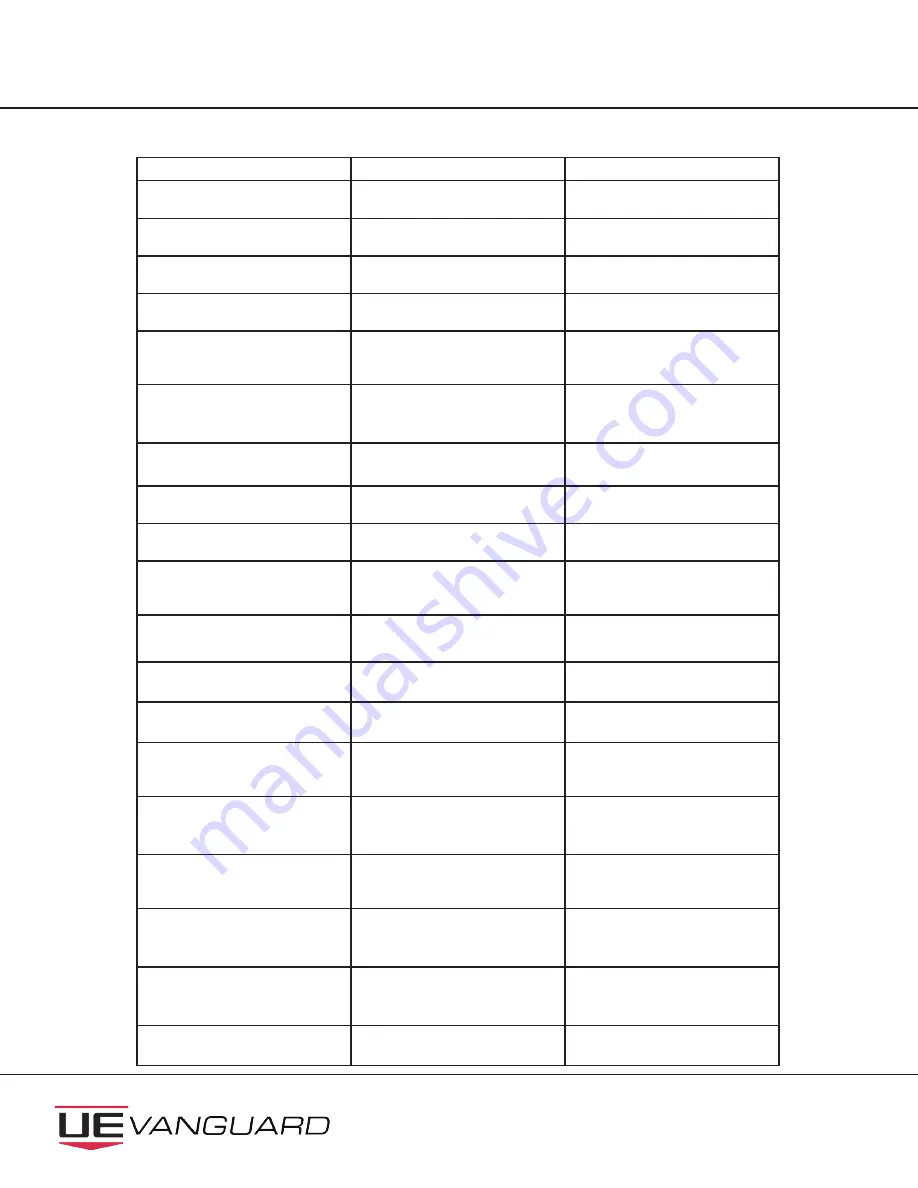
WirelessHART Toxic & Combustible Gas Detector
IM_TCD50-05
www.ueonline.com/vanguard
5
Standard
Issue Date
Title
Conform to IEC 60079-0:2011
2011/06/22 (6th Edition)
Explosive Atmospheres - Part 0: Equipment
General Requirements
Conform to IEC 60079-1:2014
2014/06/27 (7th Edition)
Explosive Atmospheres - Part 1: Equipment
Protection by Flameproof Enclosures “d”
Conform to IEC 60079-11:2011
2011/06/30 (6th Edition)
Explosive Atmospheres - Part 11:
Equipment protection by intrinsic safety “i”
Conform to IEC 60086-4:2014
2014/09/03 (4th Edition)
Primary batteries - Part 4: Safety of lithium
batteries
Conform to IEC 61010-1
2010
Electrical equipment for measurement,
control, and laboratory use; Part 1: General
requirements
Conform to EN 55011:2009+A1:2010
2010/01/31
Industrial, scientific and medical equipment.
Radio-frequency disturbance characteristics.
Limits and methods of measurement
Conform to EN 60079-0
2011/06/22 (6th Edition)
Explosive Atmospheres - Part 0: Equipment
General Requirements
Conform to EN 60079-1:2014
2014/06/27 (7th Edition)
Explosive Atmospheres - Part 1: Equipment
Protection by Flameproof Enclosures “d”
Conform to EN 60079-11:2012
2012/01/31 (6th Edition)
Explosive Atmospheres - Part 11:
Equipment Protection by intrinsic safety “i”
Conform to EN 61326-1:2013
2013/02/28
Electrical equipment for measurement,
control and laboratory use. EMC
requirements. General requirements
Certified to CSA C22. 2 60079-0
2011/12/01
Explosive Atmospheres Part 0: Equipment
General requirements
Certified to CSA C22.2 60079-1
2011/12/01
Explosive Atmospheres Part 11: Equipment
protection by intrinsic safety “d”
Certified to CSA C22.2 60079-11
2011/12/01
Explosive Atmospheres Part 11: Equipment
protection by intrinsic safety “i”
Certified to CSA C22.2 61010-1-12
2012/5/11
Electrical equipment for measurement,
control, and laboratory use; Part 1: General
requirements
Conform to UL 60079-1
2009/04/10 (Edition 6)
UL standard for safety electrical apparatus
for explosive gas atmospheres Part 1:
Flameproof Enclosures “d”
Conform to UL 913
2013/12/06 (Edition 8)
Intrinsically safe apparatus and associated
apparatus for use in Class I, II and III,
Division I Hazardous (Classified) Locations
Conform to UL 1203
2013/11/22 (Edition 5)
Explosion Proof and Dust Ignition proof
electrical equipment for use in hazardous
(Classified) Locations.
Conform to UL 61010-1
2012/5/11 (Edition 3)
Electrical equipment for measurement,
control, and laboratory use; Part 1: General
requirements
FCC Rule Part 15b
Declaration of Conformity (DoC) &
Verification
The device has been certified in accordance with the applicable requirements of the following standards:
Table 1