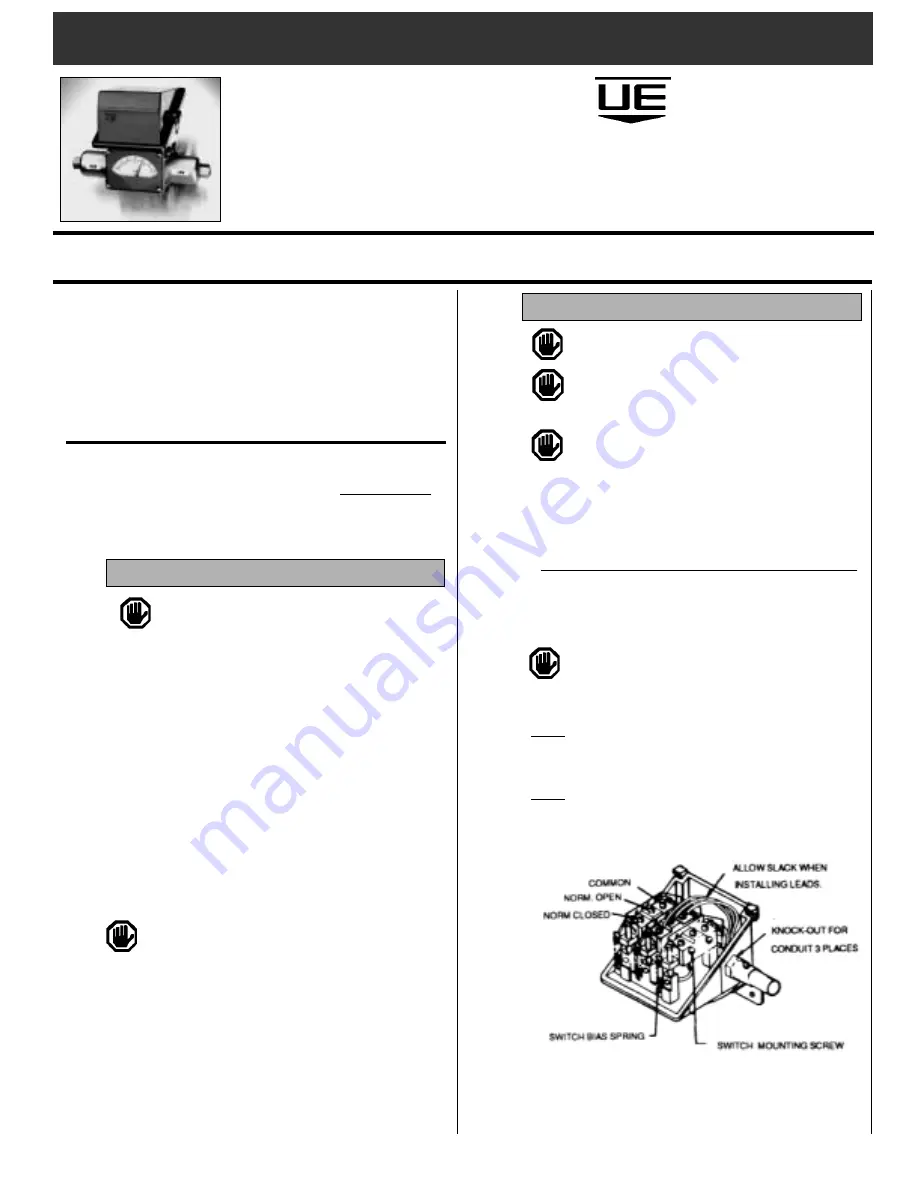
GENERAL
Pressure variations are sensed by a bellows, diaphragm or piston sensor
which either actuates or de-actuates one, two or three snap-acting switches
at a pre-determined set point(s). Set point(s) is adjusted by turning an
internal knob and pointer (H types) or internal screw (J types).
Tools Needed
Screwdriver
Hammer
Adjustable wrench
MOUNTING
I
NSTALL UNIT WHERE SHOCK, VIBRATION AND TEMPERA-
TURE FLUCTUATIONS ARE MINIMAL. ORIENT UNIT SO THAT
MOISTURE IS PREVENTED FROM ENTERING THE ENCLO-
SURE. IF UNIT IS BEING INSTALLED WHERE HEAVY CONDENSATION
IS EXPECTED, VERTICAL MOUNTING (PRESSURE CONNECTION
DOWN) IS REQUIRED. DO NOT MOUNT UNIT IN AMBIENT TEMPERA-
TURES EXCEEDING PUBLISHED LIMITS.
400 Series pressure controls can be mounted in any position, provided the
electrical conduit is not facing up. The preferred mounting position is ver-
tical (pressure connection down).
The cast-in knockouts for 3/4” electrical conduit are located on the side
and rear of the enclosure. These can easily be knocked out by placing the
blade of a screwdriver in the groove and rapping sharply with a hammer.
Mount the unit via the (2) 1/4” screw clearance holes on the enclosure.
See Dimensions. Units may also be mounted via the NPT pressure con-
nection.
ALWAYS HOLD A WRENCH ON THE PRESSURE HOUSING HEX
WHEN MOUNTING UNIT. DO NOT TIGHTEN BY TURNING
ENCLOSURE. THIS WILL DAMAGE SENSOR AND WEAKEN
SOLDER OR WELDED JOINTS.
U N I T E D E L E C T R I C
C O N T R O L S
Installation and Maintenance
Instructions
IMP400-07
Please read all instructional literature carefully and thoroughly before starting. Refer to the final page for the listing of Recommended Practices,
Liabilities and Warrantees.
400 Series
Pressure Controls
Types: H400, H402, H403,
H400K, H402K, J400, J402,
J403, J400K, J402K
Part I - Installation
WIRING
DISCONNECT ALL SUPPLY CIRCUITS BEFORE WIRING.
ELECTRICAL RATINGS STATED IN LITERATURE AND ON NAME-
PLATE SHOULD NEVER BE EXCEEDED. OVER-LOAD ON A
SWITCH CAN CAUSE FAILURE ON THE FIRST CYCLE.
WIRE UNITS ACCORDING TO LOCAL AND NATIONAL ELECTRI-
CAL CODES. MAXIMUM RECOMMENDED WIRE SIZE IS 14 AWG.
Connect conduit to the case and wire directly to the switch terminals accord-
ing to local and national electrical codes. Bring the wires up to terminals
from the rear of the case. (See fig. 1.) If manual reset switch or DPDT options
are used, lead wires are supplied, color coded as follows:
ALLOW ENOUGH SLACK SO AS NOT TO AFFECT SWITCH MOVE-
MENT WHEN MAKING SETTING ADJUSTMENTS AND ENSURE
THAT THE WIRES ARE NOT TOUCHING THE COVER WHEN
INSTALLED.
NOTE: For larger wire gauges, a one time shift may be experienced or
expected due to space limitations within the enclosure. Verify setpoint after
installation.
NOTE: The middle switch assembly is omitted for dual switch controllers.
The outer switch assemblies are omitted for single switch controllers. Type
“J” controls have internal screw adjustments and type “H” have cam assem-
blies for internal calibrated adjustments.
Switch 1
Switch 2
Common
Violet
Yellow
Normally Open
Blue
Orange
Normally Closed
Black
Red
Figure 1