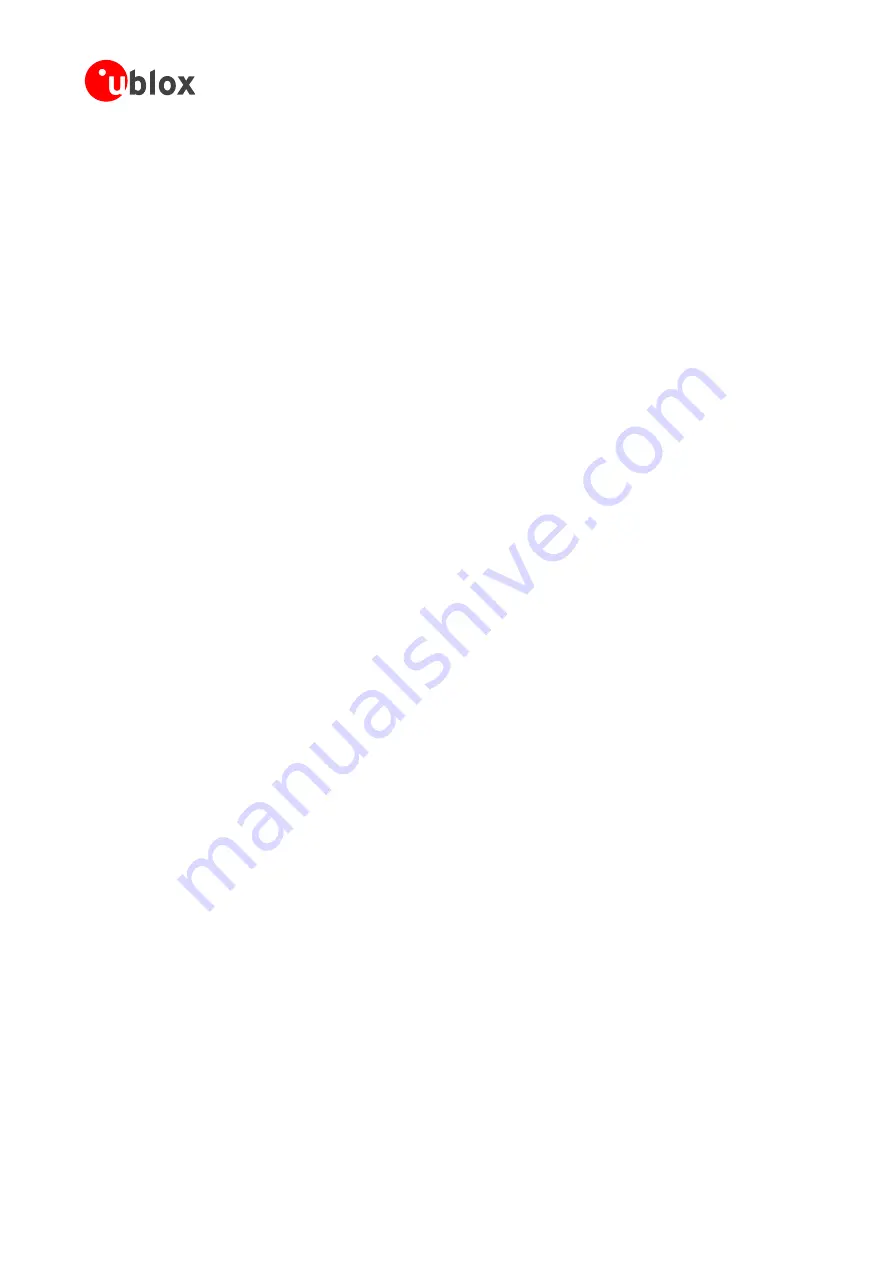
SARA-G3 and SARA-U2 series - System Integration Manual
UBX-13000995 - R26
Design-in
Page 163 of 217
A few hardware techniques may be used to reduce the Module-to-Ambient thermal resistance in the application:
Connect each
GND
pin with solid ground layer of the application board and connect each ground area of
the multilayer application board with complete via stack down to main ground layer
Provide a ground plane as wide as possible on the application board
Optimize antenna return loss, to optimize overall electrical performance of the module including a decrease
of module thermal power
Optimize the thermal design of any high-power component included in the application, as linear regulators
and amplifiers, to optimize overall temperature distribution in the application device
Select the material, the thickness and the surface of the box (i.e. the mechanical enclosure of the application
device that integrates the module) so that it provides good thermal dissipation
Force ventilation air-flow within mechanical enclosure
Provide a heat sink component attached to the module top side, with electrically insulated / high thermal
conductivity adhesive, or on the backside of the application board, below the cellular module, as a large part
of the heat is transported through the GND pads and dissipated over the backside of the application board
For example, after the installation of a robust aluminum heat-sink with forced air ventilation on the back of the
same application board described above, the Module-to-Ambient thermal resistance (R
th,M-A
) is reduced up to
the Module-to-Case thermal resistance (R
th,M-C
) defined in the
SARA-G3
[1] or the
SARA-U2
series Data Sheet
The effect of lower R
th,M-A
due to the installation of a robust heat-sink on the backside of the application board
with forced air ventilation can be seen from the module temperature increase, which now can be summarized as
following for SARA-G3 modules:
~1 °C during a GSM voice call (1 TX slot, 1 RX slot) at the maximum TX power
~2 °C during a GPRS data transfer (2 TX slots, 3 RX slots) at the maximum TX power
Beside the reduction of the Module-to-Ambient thermal resistance implemented by the hardware design of the
application device integrating a SARA-G3 and SARA-U2 series module, the increase of module temperature can
be moderated by the software implementation of the application.
Since the most critical condition concerning module thermal power occurs when module connected mode is
enabled, the actual module thermal power depends, as module current consumption, on the radio access mode,
the operating band and the average TX power.
A few software techniques may be implemented to reduce the module temperature increase in the application:
Select the radio access mode which provides lower temperature increase by means of AT command (see the
u-blox AT Commands Manual
Select by means of AT command the GPRS multi-slot class which provides lower current consumption (see
current consumption values reported in the
SARA-G3
[1] or the
SARA-U2 series Data
Sheet
[2], and the
u-blox AT Commands Manual
[3], +UCLASS command)
Select by means of AT command the operating band which provides lower current consumption (see current
consumption values reported in the
SARA-G3
[1] or the
SARA-U2 series Data Sheet
and the
u-blox AT Commands Manual
[3], +UBANDSEL command)
Enable module connected mode for a given time period and then disable it for a time period enough long to
properly mitigate temperature increase