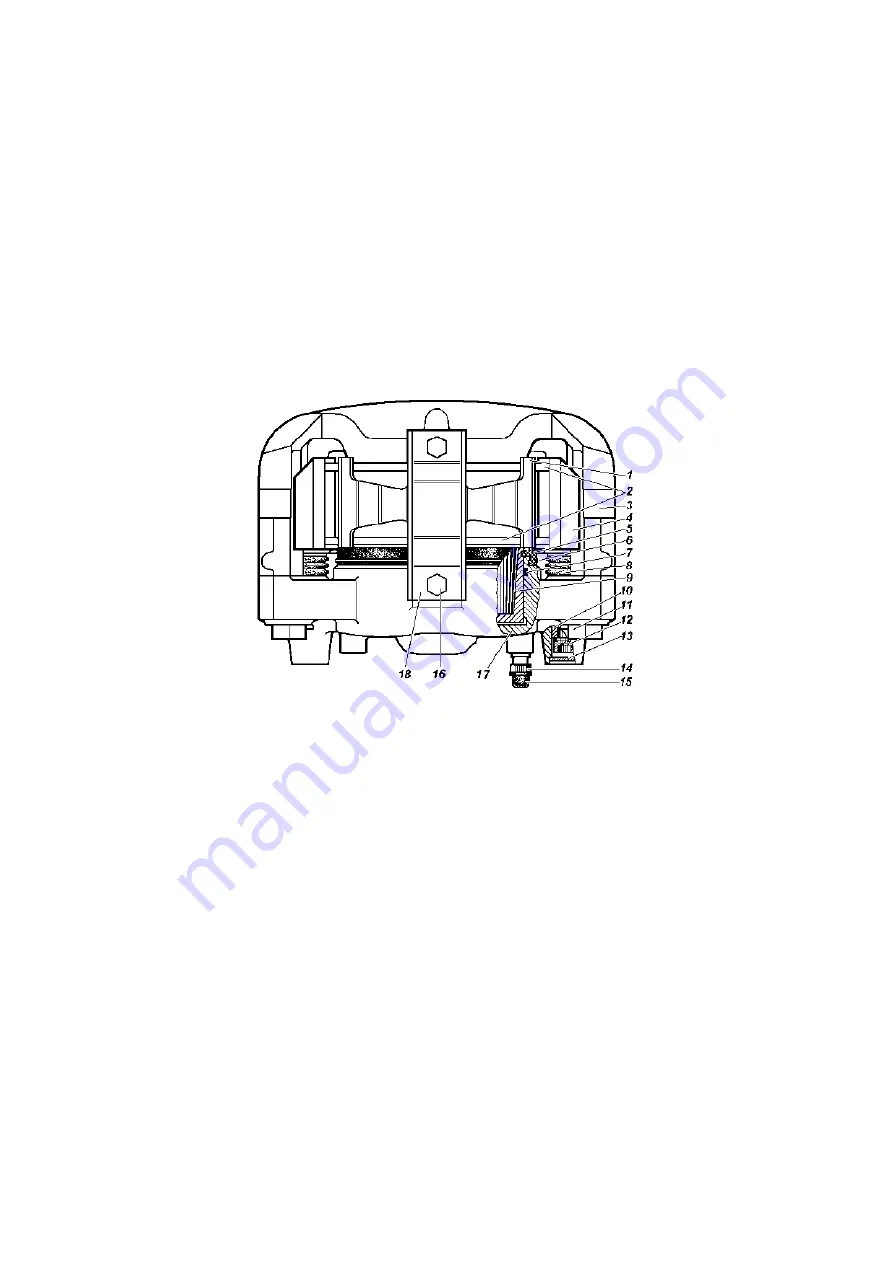
64
Disc brakes of front wheels.
To inspect brake shoes 2 (Fig. 9.28), place the vehicle on a level ground and set the
parking brake. Inspect the pads through the window in caliper 4. If the linings wear to the thickness of 1.5
–
2.0 mm,
replace the pads by the new one. Replace the pads on both front brakes.
On vehicles which brakes are furnished
with pads with a wear alarm, replace the pads when a rattle (ringing) appears, indicating that the pads are worn.
When replacing these pads, be sure to install them correctly. The pads equipped with a wear sound indicator are not
interchangeable for the left and right brakes. These pads shall be installed on the side of the brake pistons so that the wear
indicator is located at the top of the pad (brakes). On the outer side of both brakes install the pads without a signaling
device.
To replace the brake pads, unscrew the bolts 16, remove the holder 18 and the spring 1.
Check the condition of the brake disc. If brake disc surface has deep notches and burrs, remove it from vehicle, clean
and grind. If the disc is worn to a thickness of 20.4 mm, replace it with a new one.
Check for leaks from the cylinder block.
Check the protective caps 5 and covers 8, which shall be without damage and properly installed in the seats, and
replace them if necessary.
Check the outer surface of bushings 10 in the area of boots 8 for grease and lubricate them with UNIOL 2M/1 TU
38.5901243-92 grease, if necessary.
Fig. 9.28 Front disk brakes.
1 - spring; 2 - pads; 3 - clip; 4 - support; 5 - protective cap; 6 - snap ring; 7 - sealing ring; 8 - protective cover; 9 - piston; 10 - bushing;
11 - bolt; 12 - screw; 13 - plug; 14 - blow-off valve; 15 - cap; 16 - spring carrier bolts; 17 - cylinder block; 18 - spring retainer
Move clip 3 until pistons 9 rest in the inner surface of cylinder block 17 Blow-off valve 14 can be opened to ease the
fluid displacement from cylinder block 17. Close valve 14 as soon as pistons 9 completely sink into the cylinder block.
Before moving clip 3, remove the cap of the master cylinder reservoir and do not let the fluid overflow while moving the
clip.
CAUTION! It is prohibited to use the tire iron in order to recess the pistons, as this will lead to the deformation of
the guide sleeves 10, the failure of the clip 3 and the rupture of the cover 8.
Replace worn brake pads with new ones. Replace the pads completely on both sides of the front axle. To place the
pads against the disc, press the brake pedal 2-3 times.
Install spring 1, spring carrier 18 and screw bolts 16.
CAUTION! Since the spring holder 18 has an asymmetrical shape, make sure that it is properly installed. A
properly mounted holder provides clamp of both pads by spring 1.
During further operation, the necessary clearance between the pads and the brake disc is maintained automatically.
CAUTION! The fasteners of the disc brake, the pipe tee, the parts of the parking brake actuator, the regulator drive
and the regulator itself are fixed against loosening with adhesive-sealant (without spring washers). In case of loosening
these bolts and nuts add glue-sealant.
Rear wheel drum brakes
(Fig.9.29). Remove brake drums periodically and clean the brake parts from dust and dirt.
The frequency of this operation depends on vehicle operation conditions. Cleaning shall be done more often in the
summer and when driving on dirty roads, and less frequently - in the winter.
After removing the drum, check that the wheel cylinder components are securely attached to the shields. Pay
attention to the condition of the wheel cylinders, protective caps 7, as well as the condition of the brake drum.
Protective caps must be tightly installed in the piston and cylinder seats and must not be damaged.
If on the working surface of the drum there are deep risks, scuffs or uneven wear, then produce a drum rebore, based
on the central hole of the drum.
The maximum permissible diameter of the working re-bored brake drum is 281 mm.