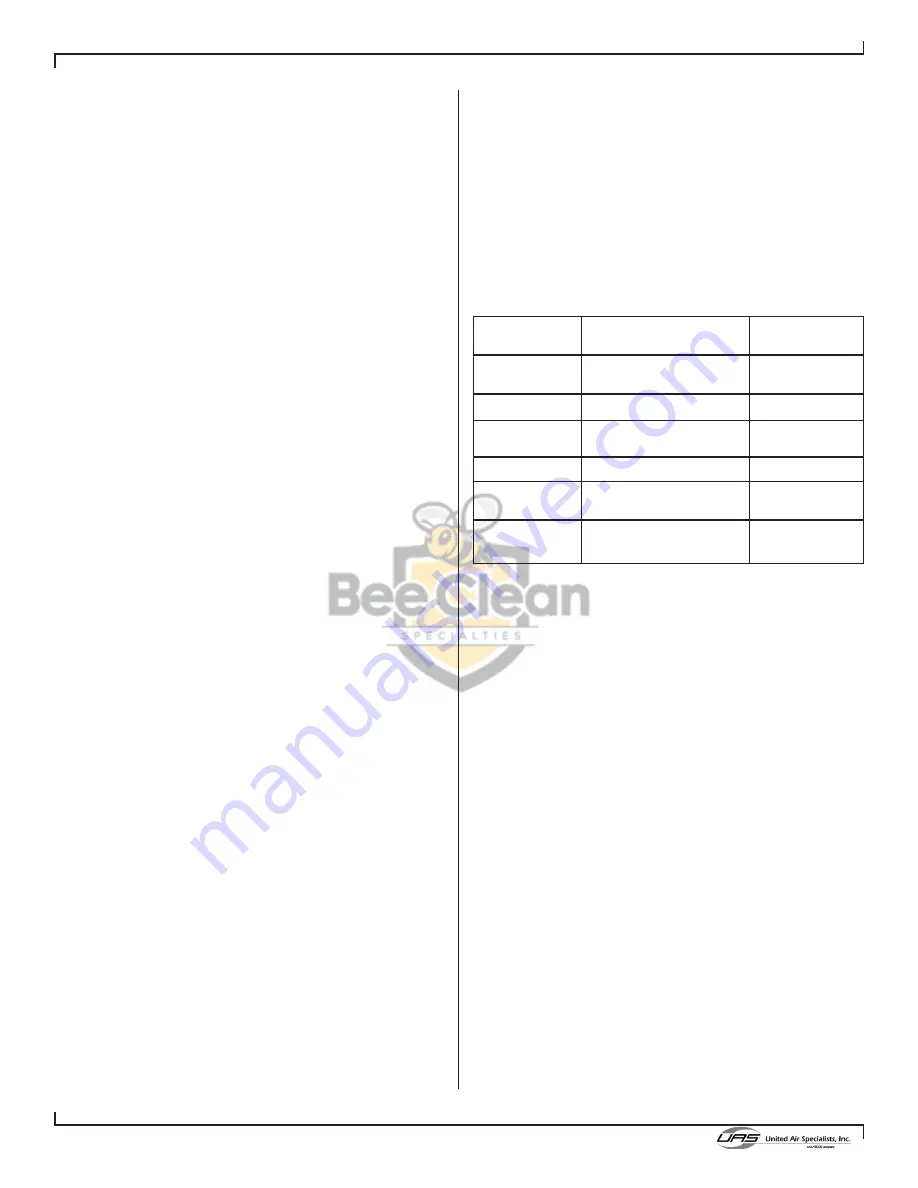
8
revised 10/09
Smog-Hog
PSH Series Model
3.4 Unit Storage or delay
to System Installation
if PSH installation is delayed for an extended period
(one month or more), protect system components as
follows:
1. Store in a cool, dry location. Do not disassemble.
Do not remove components.
2. cover duct and unit openings with plastic
sheeting and duct tape; cover plumbing
openings with plastic hole plugs.
3. cover skidded systems with plastic sheeting
and seal with duct tape. Do not use black plastic
sheeting. When removing components from
storage, check gaskets, seals and electrical
components for long term effects of exposure
to moisture and dust before proceeding with
installation.
4. the system exhaust blower should be protected
from the weather. failure to do so could damage
the motor, bearings, belts, and electrical
components. the following are guidelines.
• Store in an area with no vibration.
• Cover blower with a tarp do not use
a black tarp, which will promote
condensation.
• Remove drive belts.
• Rotate fan wheel monthly
also consult the blower manufacturer for storage
and start up recommendations.
3.5 Installing The System
Skidded PSH systems arrive from the factory ready for
final plumbing and wiring, with proper planning refer to
Section 2, installation Planning final installation should
be straightforward. When PSH sub-assemblies are to
be installed on customer’s structure, further instructions
are in order.
3.5.1 PSH SYSTEMS
the majority of skidded systems are shipped with
ionizers, collector cells and filters installed. the
system may be lifted into place without removing the
ionizers, collector cells and filters. However, when job
circumstances and or shipping requirements dictate,
ionizers, collector cells and filters are shipped on a
separate skid. these components should not be in-
stalled until the system is in place. individual PSH units
should be rigidly mounted, with front-to-back bearing
support in the direction of airflow. refer to figure 8.
clearance for plumbing access should be provided
under each unit, refer to installation Planning. the PSH
main drain pipe should have a drain trap and multiple
passes require drain connection(s) to be manifolded for
each pass. Structural field installed support channels
should not interfere with proposed plumbing and wiring.
Where the PSH is to be suspended, refer uaS System
Layout Drawing. Do not support ducting, plumbing or
other field hardware from the PSH.
3.5.2 GASKETS
When PSH systems are shipped in sections for field
assembly, required gasketing and mounting hardware
are provided. care is required in preparing surfaces,
attaching gasketing and in sealing corners to prevent
leaks. Surfaces to be gasketed should be confirmed as
smooth and free of rust and dirt. Gasket corners may be
abutted, but the method shown in figure 9 is a superior
method. a sealant resistant to process contaminants
and liquids (including cleaning compounds) should be
used where gaskets interface. note that temperatures
above 250
o
f exceed the limits of most common gasket
materials. only materials like viton and teflon have a
proven long-term life.
3.5.3 INLET/OUTLET PLENUMS
as supplied by uaS, transition plenums have all-welded
seams and reinforced flanges to assure tight gasket
sealing. inlet plenums include diffusers to promote even
air distribution across subsequent system components.
Mounting hole patterns exactly match adjacent
flanges. Sheet metal plenums and ducting should be
made to the same quality standards to ensure system
performance.
3.5.4 MOTOR/BLOWERS
Motor/blower assemblies installed in the field should
be equipped with vibration isolators and adequate
structural support. When supplied by others, the
motor/blower assemblies should meet air volume
specifications to the PSH model; refer to uaS System
Layout Drawing.
3.5.5 PRE-CONdITIONING EQUIPMENT
for the PSH to operate at peak efficiency, certain
pre-conditioning equipment may be required. When
supplied by uaS, this equipment should be installed
per uaS System Layout Drawing and uaS electrical
Drawings. incorrect installation of such devices as
cooling coils or other equipment may alter system
performance and void the uaS warranty.
3.5.6 ORdER OF INSTALLATION
When the PSH is shipped in sections refer to the uaS
System Layout Drawing for proper installation.
GASKET
MATERIAL
Buna N
Rubber
Pure EPdM
Buna AP
Silicone
Viton
Teflon
GOOd RESISTANCE
TO
Most mineral oils
and process oils
Most plasticizers
Most plasticizers
mineral oils
Selected oils
Most plasticizers, oils,
solvents
Most plasticizers, oils,
solvents
TEMPERATURE
LIMITS (F
o
)
250
250
250
250
500-700
700