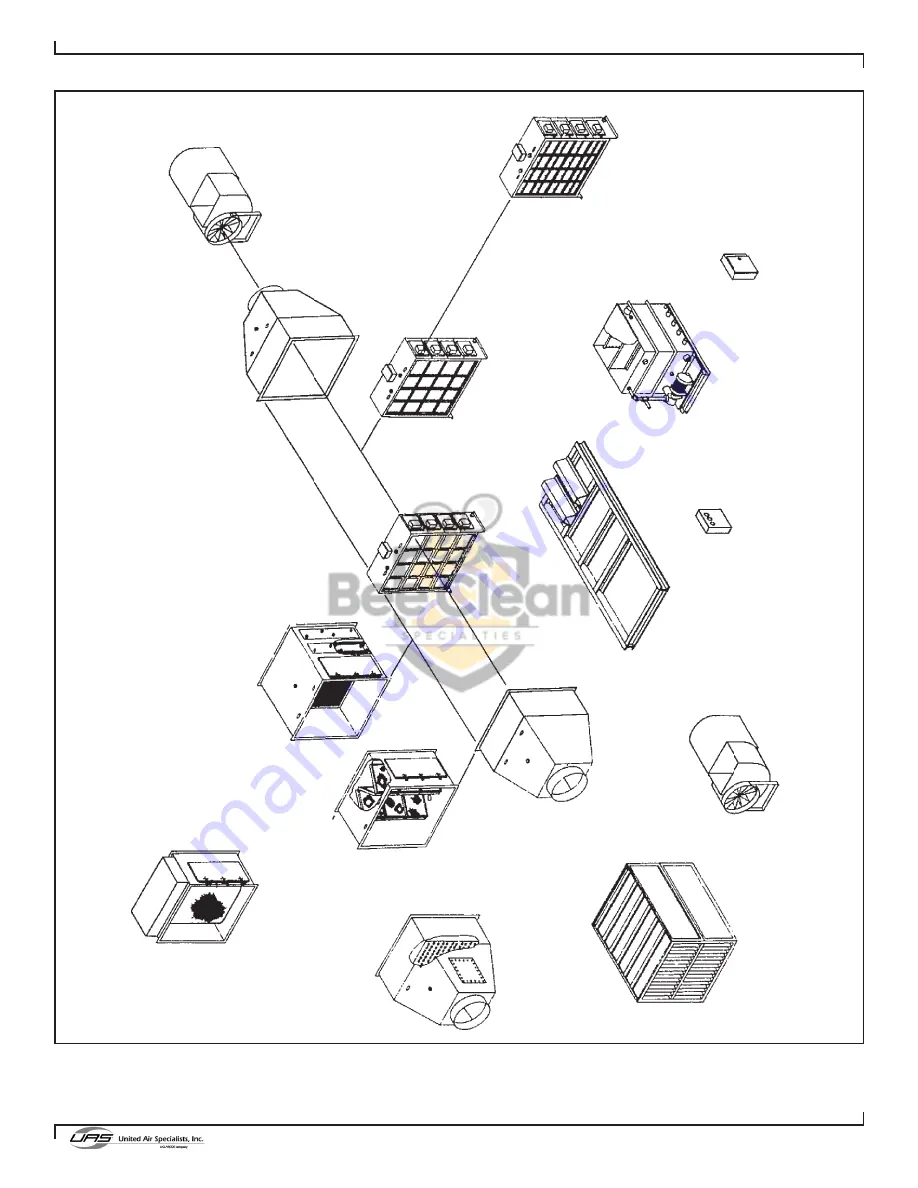
3
revised 10/09
Smog-Hog
PSH Series Model
Figure 4
PSH System Components
indexing
filter
Vee-bank
filter
inlet
Plenum
with
Baf
fle
Dif
fusers
air-to-
air
Heat
exchange
fresh
air
Blower
inlet
Plenum
cooling
coils
with
Plenum
PSH
SYSTEM
COMPONENTS
SM
oG-H
oG®
(e
SP)
Skid
W
ash
control
Panel
Blower
Panel
recirculation
tank
outlet
Plenum
System
Blower
Sno
G-H
oG®
with
in-Place
cleaning
System
(f
ixed
Headers)