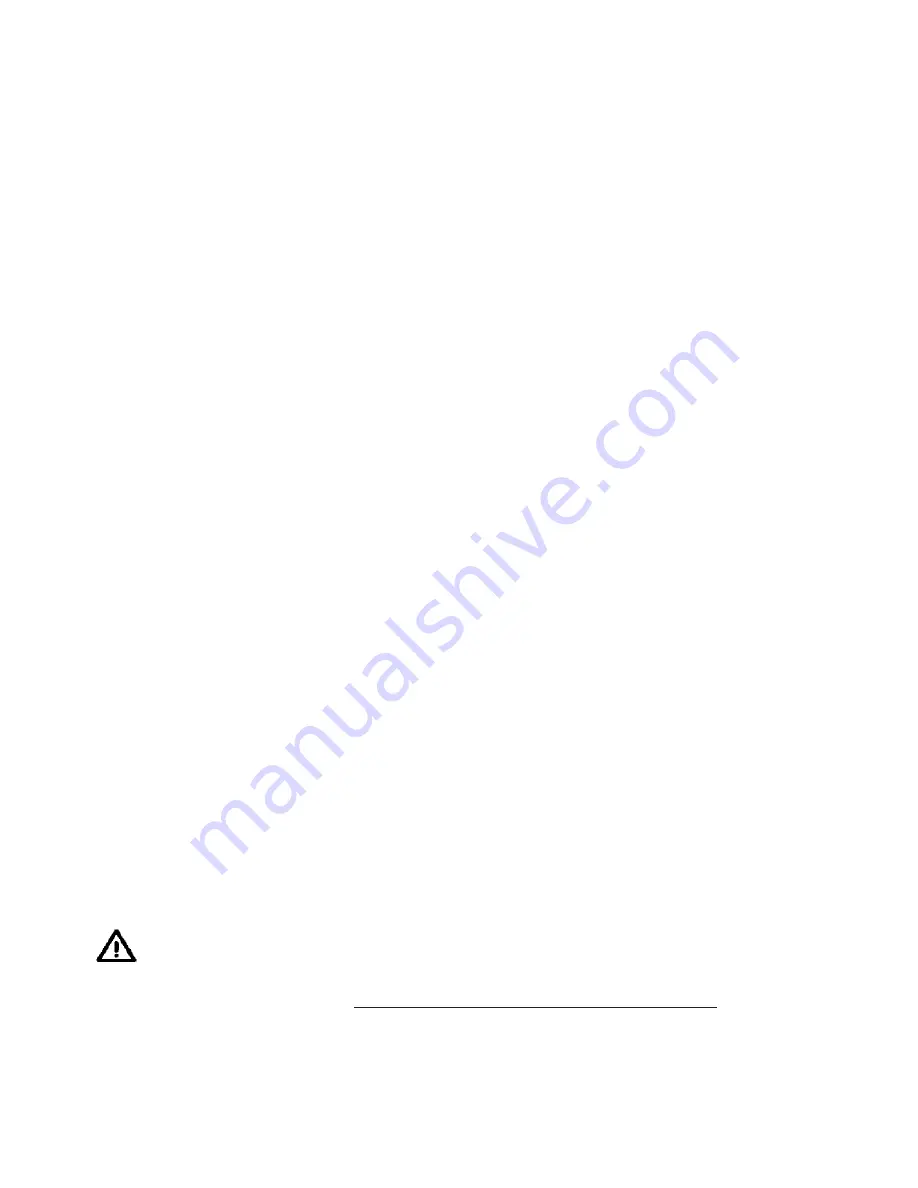
OPERATION
1
Inspect the machine, hoses, and cleaning tools for cleanliness and completeness.
2
Fill the Solution Tank with warm water. Using warm water may be a benefit in cleaning
effectiveness, but do not use hot water (above 130
°
F+/ 54
°
C) in the tank. Add liquid cleaning
solution with a pH value of between 6 and 9. High pH detergents and/or acid rinses will
accelerate the wear of the seals and will void the warranty.
3
Plug in the power cords. Do not connect both cords to the same outlet. If you are certain the
cords are on separate circuits, turn the Heat switch on.
CAUTION:
using the Heat switch
when the cords are on the same circuit may cause the circuit breaker in the wall to trip.
NOTE:
the cord with the red label “H” at the cord retainer supplies power to the heater. The
other cord powers the vacuum, pump, and cooling fan.
4
Attach the spray hose to the solution quick disconnect on the front of the machine and attach
the vacuum hose to the hose barb on the recovery tank. Attach the other ends of the hoses to
the cleaning tool.
5
Allow the heat exchanger two minutes to reach operating temperature.
6
Turn the pump on. Turn the vacuum on.
NOTE:
the pump has a built in pressure switch; the
pump runs only when you are spraying.
7
Begin cleaning using the correct hoses and tool.
8
Use defoamer in the recovery tank any time foaming occurs.
9
Monitor the water level in the solution tank. Do not let the pump run dry.
10
When the solution tank gets low, turn off the pump, fill the solution tank, empty and clean the
recovery tank.
11
When finished with the job, remove any unused solution from the solution tank, and run a few
gallons of clean water through the system to rinse out any detergent.
BALL FLOAT VACUUM SHUT-OFF
Prior to using the machine, always check that the float filter is clean and the ball can travel freely.
When the recovery tank is full, the ball float will rise and will shut off the vacuum flow to prevent any
more water from entering the tank. Turn off the vacuum, and empty the recovery tank.
NOTE: if foam is present or if the ball float is prevented from rising, the float will not be able to stop
the air flow, and the tank may over fill.
CAUTION!
To avoid vacuum motor damage, always make sure the float filter is clean and the ball can travel
freely prior to using the machine. And always use a defoamer when foaming occurs.