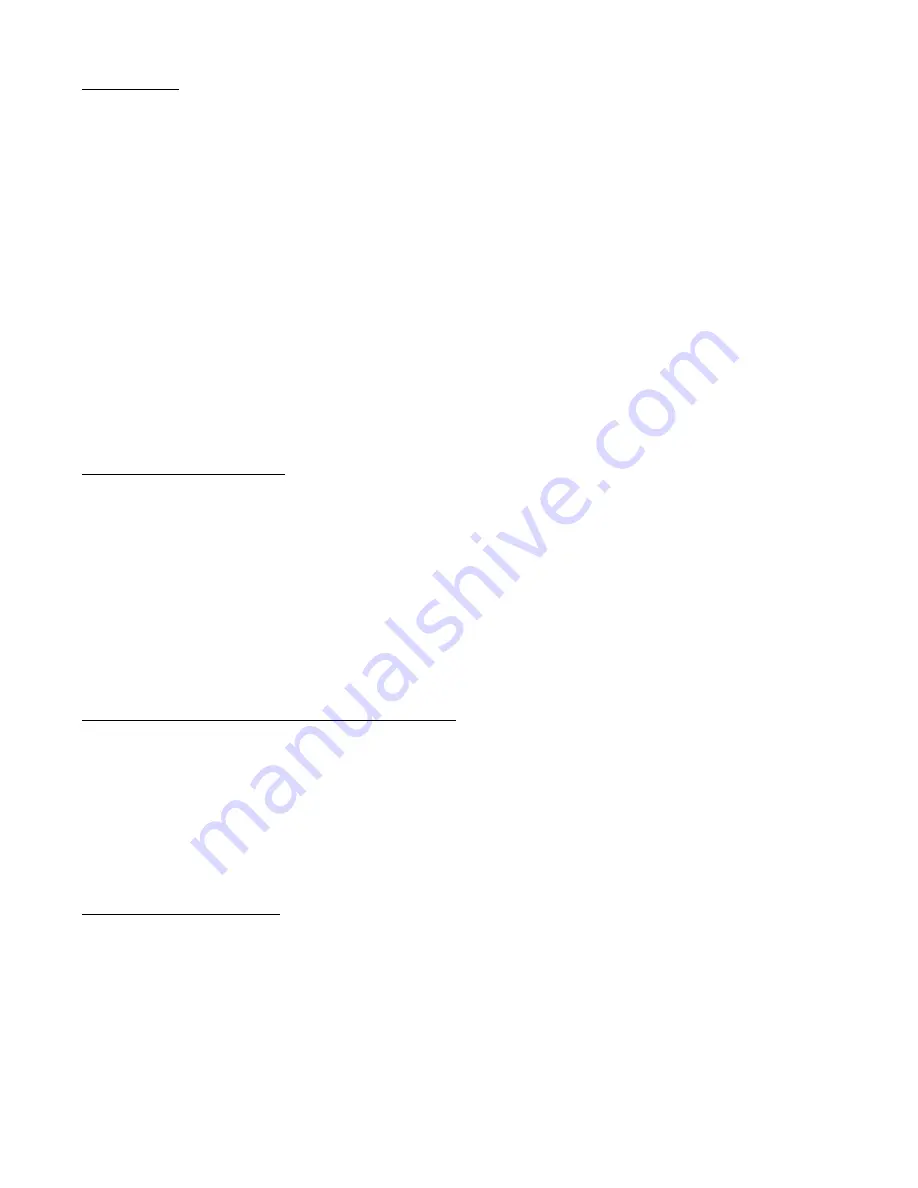
20
107362-01 - 8/17
VII. Venting
A. Vent System Design (continued)
7. Supporting Pipe - Vertical and horizontal sections of pipe must be properly supported. Maximum support spacing is as
follows:
• Support CPVC/PVC horizontally and vertically every 4 feet.
• Support DuraVent PolyPro horizontally near the female end of each straight section of pipe and vertically every 10 feet.
• Support Centrotherm InnoFlue horizontally every 39 inches with additional supports at elbows and vertically every 78".
• Support 2" Selkirk Polyflue horizontally every 30". Support 3" Polyflue horizontally every 39". Support vertical runs of
both 2" and 3" Polyflue every 16 ft.
• Support DuraVent FasNSeal horizontally every 6 ft. or less. Support vertical runs at the base and every 12 ft. or less.
These instructions for the installation of the venting system shall specify that the horizontal portions of the venting system
shall be supported to prevent sagging; the methods of and intervals for support shall be specified. These instructions shall also
specify that the venting system:
• For category II and IV boilers, be installed so as to prevent accumulation of condensate.
• For category II and IV boilers, where necessary, have means provided for drainage of condensate.
Les instructions d´installation du système d´évacuation doivent préciser que les sections horizontales doivent être
supportées pour prévenir le fléchissement. Les méthodes et les intervalles de support doivent être spécifiés. Les
instructions divent aussi indiquer les renseignements suivants:
• les chaudières de catégories II et IV doivent être installées de façon à empêcher l´accumulation de condensat:
• et si nécessaire, les chaudières de catégories II et IV doivent être pourvues de dispositifs d´évacuation du condensat.
8. Allowing for Thermal Expansion -
• For CPVC/PVC pipe design the vent system to allow 3/8" of thermal expansion for every 10ft of CPVC/PVC pipe.
The boiler will always act as an anchor to one end of the vent system. If at all possible, select and install hangers and
wall thimbles so that the vent system can expand towards the terminal. When a straight run of pipe exceeds 20ft and
must be restrained at both ends, an offset or expansion loop must be provided (Figures 7.3a, 7.3b). When a straight
horizontal run of pipe exceeds 20ft and is restrained at one end with an elbow at the other, avoid putting a hanger or
guide less than “Y” inches from the elbow in the adjoining straight section (Figure 7.3c). Thermal expansion fittings
are not permitted.
• When properly assembled expansion of PolyPro, Polyflue and InnoFlue vent systems is accommodated at the joints. See
Part VII-F, G & H of this manual for details.
• Stainless steel vent systems must be free to expand and contact in accordance with manufacturer's installation
instructions.
9. Running PVC Vent Pipe Inside Enclosures and Through Walls - PVC vent pipe must be installed in a manner that permits
adequate air circulation around the outside of the pipe:
• Do not enclose PVC venting - Use CPVC in enclosed spaces, even if PVC is installed upstream.
• PVC venting may not be used to penetrate combustible or non-combustible walls unless all of the following conditions are
met:
a. The wall penetration is at least 66 inches from the boiler as measured along the vent.
b. The wall is 12" thick or less
c. An airspace of at least that shown in Figure 7.4 is maintained around the OD of the vent.
If any of these conditions cannot be met, use CPVC for the wall penetration.
10.
Vent Manufacturer’s Instructions
– The vent system manufacturer may have additional vent system design requirements.
Read and follow the vent manufacturer’s instructions in addition to those shown here. Where a conflict arises between the
two sets of instructions, the more restrictive requirements shall govern.
Summary of Contents for ASPEN ASPN-085
Page 94: ...94 107362 01 8 17 Figure 10 5 Internal Wiring Ladder Diagram X Wiring continued...
Page 95: ...95 107362 01 8 17 PAGE LEFT INTENTIONALLY BLANK...
Page 96: ...96 107362 01 8 17 X Wiring continued CONDENSATE FLOAT SWITCH...
Page 97: ...97 107362 01 8 17 X Wiring continued Figure 10 6 Internal Wiring Connections Diagram...
Page 106: ...106 107362 01 8 17 Operating Instructions XI Start Up and Checkout continued...
Page 160: ...160 107362 01 8 17 XV Service Parts continued All models 5G 5F 5B 5A 5D 5E 5C 5D...
Page 179: ...179 107362 01 8 17...