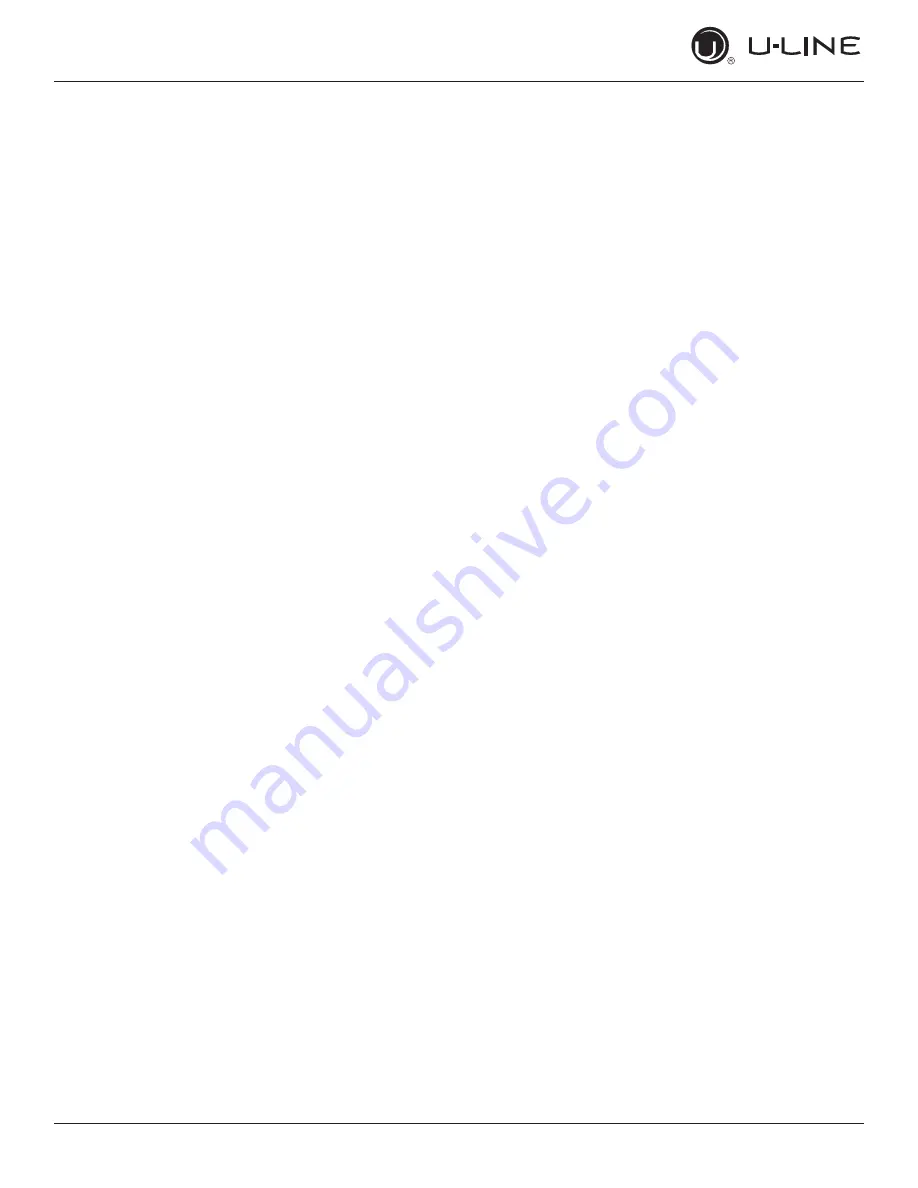
USER GUIDE
u-line.com
u-line.com
Troubleshooting
ICE QUALITY
Odor, grey color, or off taste in the ice:
• Is there mineral scale build up on the evaporator
plate?
The ice machine needs cleaning. See “Cleaning the Ice
Machine”.
• Is there a high mineral content in the water?
The water may need to be filtered.
• Are food items being stored in the ice bin?
Remove food from the ice bin.
• Unpleasant Odors may require the use of a char-
coal filter on the water supply line.
Clumps of ice:
• Are there clumps of ice in the bin?
If the ice isn’t used on a regular basis it will melt and form
into clumps. Break up the ice clumps with the ice scoop.
Ice cubes are too big or too small:
• Is there low ice consumption?
Ice is slowly melting in the ice bin which will affect the size
of the cubes. This is normal. When the ice bin needs to be
replenished, cubes will return to the regular size.
• Is the ice slab releasing?
Clean the evaporator. See “Cleaning the Ice Machine”
• Is the distributor tube restricted?
Check the water line to the ice machine to make sure
there are no restrictions or kinks in the line. Check all
filters to make sure they are not restricted. Check that the
water flows evenly out of the distributor tube, if not, clean
the ice machine. See “Cleaning the Ice Machine”.
PLUMBING PROBLEMS
• Is the drain hose aligned over the drain?
Move the ice machine to align the drain.
• Is the ice machine draining properly?
Check that there are no kinks or restrictions in the drain
lines; this can cause water to back up in the ice bin.
Check that foreign material is not blocking the ice bin drain
located at the right rear corner of the ice bin. Check the
drain pump discharge and vent line or any restrictions or
kinks. Check that the drain pump is level.
NOTE:
If there are plumbing issues outside of the ice
machine, they cannot be repaired by the service
technician. A qualified plumber will have to be
called.
TROUBLESHOOTING THE DRAIN PUMP
NOTE:
If the drain pump reservoir (not the ice machine
bin) reaches overfill condition, the power to the
ice machine will be shut off.
If the ice machine is not working, check the
following:
• Make sure there is power at the receptacle.
• Make sure the ice machine is turned on.
• Make sure the ice bin is not full.
Then check the drain pump:
The pump does not run:
• Make sure the pump is plugged in and there is power
to the receptacle.
• Check the inlet to the drain pump for debris and clean
as needed. Remove clamps and inlet tube from drain
pump to check for and remove debris.
• Make certain the vent line is free of kinks/sharp bends
or restrictions.
• Make certain there is enough water to activate the
drain pump. It will take at least one (1) quart (.95
liters)of water to activate the drain pump.
The pump runs, but no water is pumped out:
• Check that the vent is clear and free of restrictions.
• Check the discharge line to make certain there are no
restrictions.
• Make sure that the discharge tubing has not exceeded
the maximum lift of eight (8) feet (2.44 meters) and
the horizontal run is not greater than twenty (20) feet
(6.1 meters).
The pump runs and then quickly turns off
repeatedly:
• Check to make certain the drain pump is level.
• Check that the vent is clear and free of restrictions.
The ice machine is running but not producing ice:
• Check to make sure water is not backing up in the ice
bin.
30