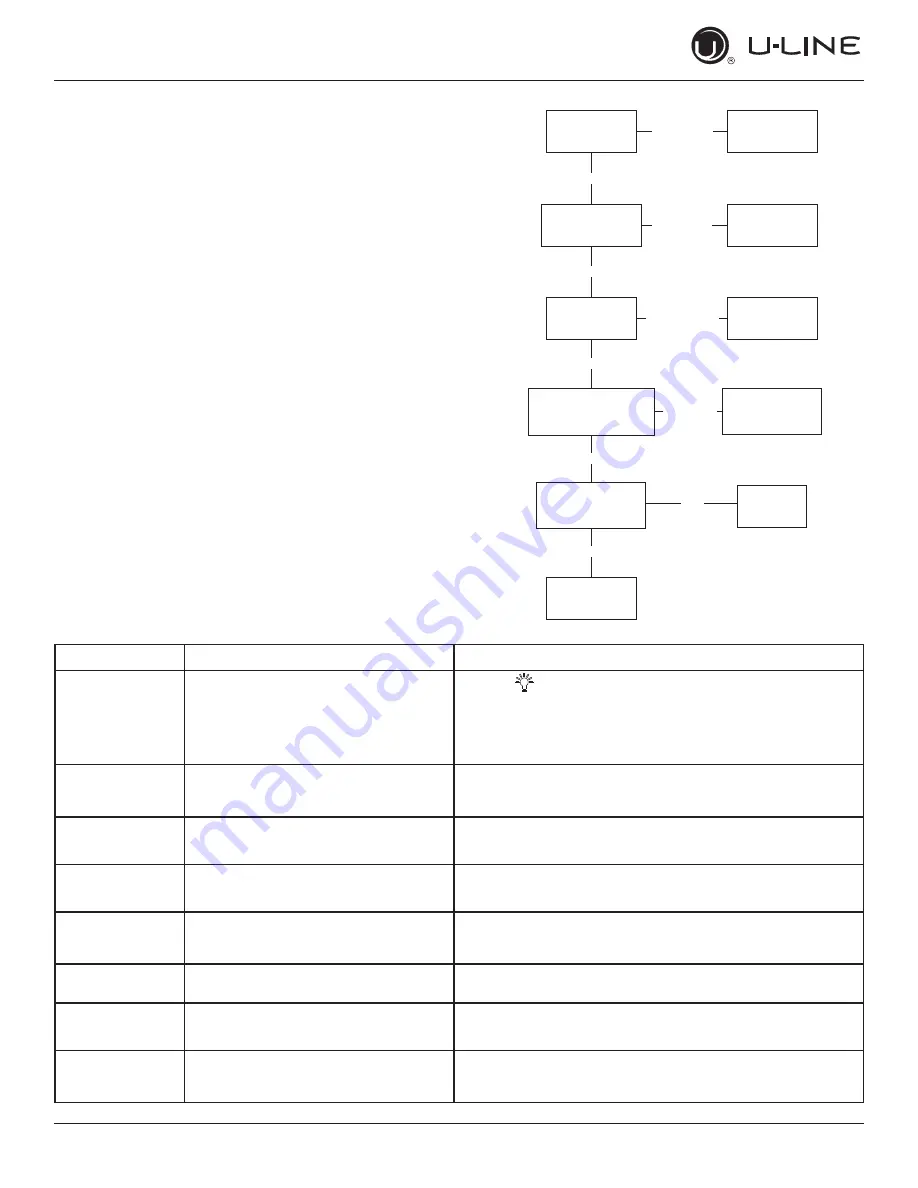
USER GUIDE
u-line.com
Troubleshooting Extended
MAIN CONTROL
The main control board is very robust and is rarely the
cause of system issues. It is important to fully diagnose
the board for any suspected failures before attempting
to remove the board for replacement or service. Follow
the guidelines below to fully test and diagnose the main
control.
Power Fault
If the unit does not (or seems to not) power on, follow the
flow chart below to help diagnose the issue. Before begin
-
ning it is important to first verify the unit is not simply set
to sabbath mode.
Check Voltage
At Wall Outlet
Verify Voltage At
Main Control
Voltage Input
Check Fuse F1
For Continuity
Replace
Reed Switch
Replace Main
Board
Replace
Fuse
Replace
Power Cord
Alert Customer
Of Power Failure
Is the Reed
Switch Operating
Properly?
Inspect
Customer UI
and Data Cable
Connect Test Display
Cycle Power And Check
For Operation
No Voltage
No Voltage
Voltage
Continuity
Operating
Not Operating
No Continuity
No
Yes
Voltage
TROUBLESHOOTING GUIDE
Concern
Potential Causes
Action
No Display or
Interior Lights
Unit may be in Sabbath mode
•
Tap to turn off Sabbath mode, test the door switch
circuit
• Unplug unit, wait 5 seconds, plug back in. If main board
does not beep, check for 120V at black and white cables
on power cord.
No Interior Light
Light may be set to OFF
Check LED strip for power
Defective door switch
Use component testing in service mode and test light circuit,
manually test door switch
Condensation on
exterior of unit
Is unit exposed to high humidity or high
ambient temps?
Moisture will dissipate as ambient temp. and humidity levels
fall. Keep exterior of unit well polished to protect surface.
No Ice
Production
Is the unit getting water?
Go to component testing and turn on fill valve and verify
120V at the valve.
Low Ice
Production
Dirty evaporator, dirty condenser, faulty
bin thermistor
Clean the evaporator using U-Line cleaner, clean the
condenser coil if needed, check bin thermistor reading in
service mode.
Alert light
flashing
Check error log
View errors in service mode, review error and take corrective
action to resolve
Ice is too dense/
not dense enough
Dirty evaporator, water starvation
Clean the evaporator if needed, check water supply, test
harvest mode, adjust ice thickness
Standing Water in
Ice Bin
Drain hose is restricted, debris in bin
drain hole, failed drain pump failed
dump valve
Make sure drain hose run is as straight as possible. Remove
any kinks or tight bends, pour 1/2 gallon of water into bin to
test drain.
40