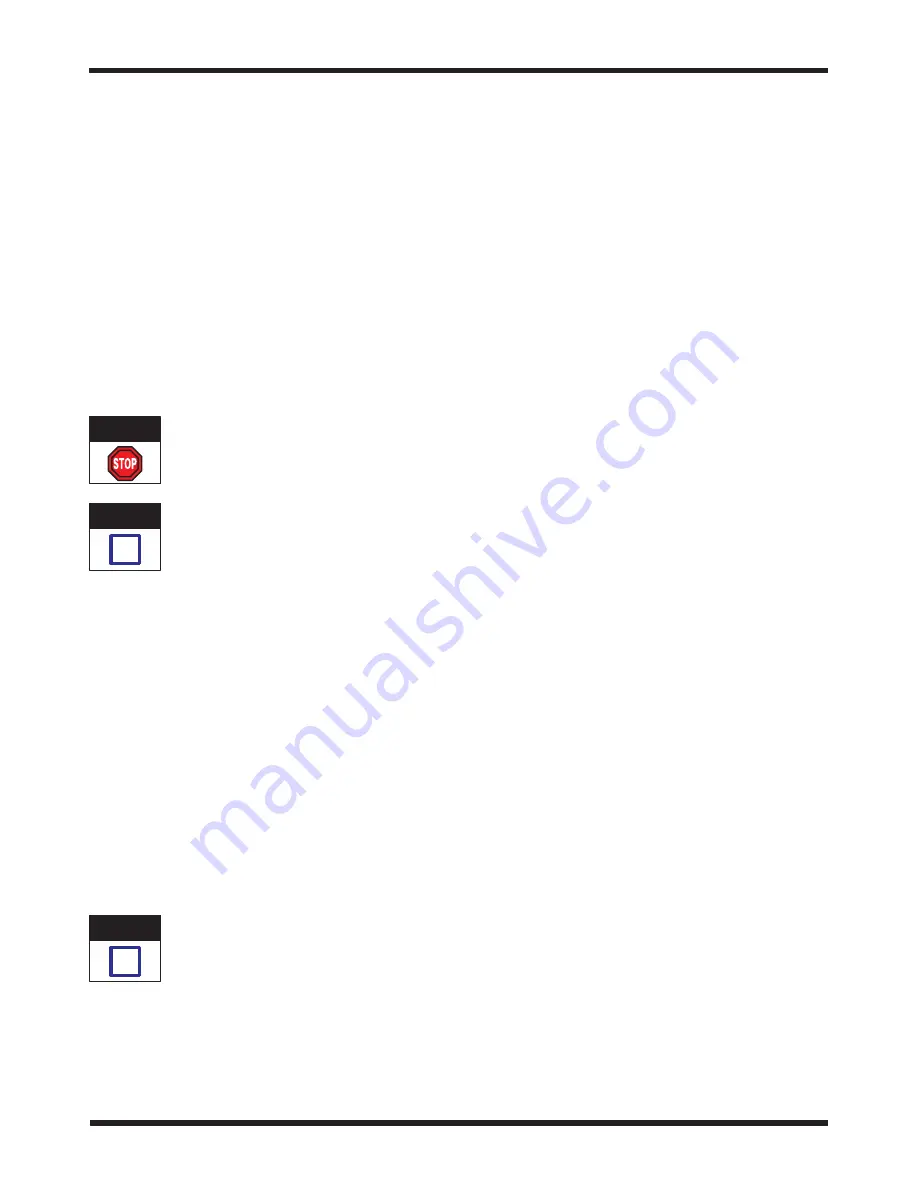
409-5880
Programmer Kit 356484-1 for FFC Terminating Machines 224910-[ ]and 318619-[ ]
Rev B
5 of 13
Tyco Electronics Corporation
C. Function Keys
The four function keys are used to save part numbers, to edit (and save) part numbers, and to move
between screens.
D. RETURN Key
The RETURN key is used to enter the diagnostic mode. Refer to Section 5, DIAGNOSTICS MODE.
E. Directional Keys
The directional keys are not used.
2.3. Internal Controls
Access to an internal display contrast adjustment is provided through a small adjustment shaft in the base of
the control module, near its left–front corner. The contrast of the LCD display can be varied by turning the shaft
clockwise or counterclockwise.
3. PROGRAMMER KIT INSTALLATION
Disconnect machine from electrical outlet before installing control box.
For identification of parts, refer to Figures 3 and 4. Item numbers on these figures refer to parts on Customer Drawing
356484-1 packaged with the programmer kit.
1. Remove the machine cover and guards.
2. Remove the top and bottom terminal guides (items 111, 113, 114, 115, 117) by removing the screws
(item 53).
3. Install the reset switch assembly (item 4) onto the solenoid switch bracket (item 21); and install the
count switch assembly (item 3) onto the switch bracket (item 22) with screws (item 10). Secure the
assemblies to locations on the rear plate with screws (item 27) and washers (item 31). See Figure 3.
4. Clamp the cam mount (item 23) and switch cam (item 24) onto the main shaft (item 211) with screws.
The lobe of the cam must be toward the front of the machine with the mounting screw horizontal with the
center of the main shaft. Refer to Figure 3.
5. Assemble the strip block (item 19), pivot shaft (item 20), return spring (item 16), and retaining rings
(item 29). Connect the pull rod (item 15) to the pivot shaft (item 20). Refer to Figure 4. Re–install the top
and bottom terminal guides (items 111, 113, 114, 115, 117) with screw (item 53).
6. Install the solenoid stop (item 14) and skip solenoid (item 5) with the screws (item 26). Connect the
pull rod (item 15) to the skip solenoid (item 5) with the pin (item 18) and retaining rings (item 29). Refer
to Figure 4.
The solenoid plunger should not extend more than 9.5 mm [.375 in.] from beyond the closed position.
7. Organize the wiring harness into the machine using cable clamp (item 11). Connect the harness to
the programmer solenoid and switches as shown on Drawing Customer 356484.
8. Connect the programmer interface cable to the back of the programmer.
9. Replace the machine guards, and install the solenoid guard (item 30).
DANGER
NOTE
i
NOTE
i